Technology Category
- Sensors - Autonomous Driving Sensors
Applicable Industries
- Automotive
- Electronics
Applicable Functions
- Product Research & Development
- Sales & Marketing
Use Cases
- Smart Parking
- Vehicle-to-Infrastructure
Services
- Testing & Certification
About The Customer
The Auburn University SAE Racing Team, founded in 1996, is dedicated to designing and building formula-style racing cars. The team has a 21-year history of successfully building 20 cars and participating in SAE-sponsored events in the United States, Germany, and Australia. Their current and future car designs feature a carbon fiber monocoque structure, combustion powertrain, and chassis control, and full aerodynamic surfacing. The team is divided into three system development areas - powertrain, chassis, electronics - each led by a lead engineer who manages a team of development engineers. All team members work closely with a faculty advisor and marketing team, led by a marketing director. The Auburn Team is affiliated with the College of Engineering Department of Mechanical Engineering.
The Challenge
Auburn University's Formula SAE team, with a history of designing and building formula-style racing cars, faced a significant challenge in optimizing their racecar design while adhering to constraints related to mass and SAE racecar specifications. The team aimed to improve the car's performance by focusing on components that promised mass reduction with equal or increased stiffness. The monocoque chassis was one such area of focus. The team aimed to reduce the mass while increasing the monocoque suspension stiffness to enhance the racecar's handling. However, achieving this design objective was not straightforward. The student team members had to consider concurrent development design goals and meet demanding build deadlines.
The Solution
To overcome the design challenge, the Auburn Formula SAE Team utilized the HyperWorks suite of computational tools to implement a simulation-driven design process. HyperMesh was used to generate finite element models, and OptiStruct was employed to solve and optimize the design, focusing on optimizing the stiffness-to-mass ratio of components. HyperView was used to view and understand the optimized structure. For the monocoque suspension mass optimization, CAD geometry was initially imported into HyperMesh to create a meshed model. After assigning composite material properties to the primary monocoque structure and aluminum properties to the bonded end cap, design and non-design regions of the model were specified. Loads were input, and the maximum monocoque displacement was constrained to a maximum allowed value. A three-step OptiStruct optimization process for composite structures was then applied to minimize the monocoque volume. The optimized results were analyzed in HyperView, and a manufacturable geometry was created, which was subsequently evaluated using linear finite element analysis to ensure all design requirements were met.
Operational Impact
Quantitative Benefit
Case Study missing?
Start adding your own!
Register with your work email and create a new case study profile for your business.
Related Case Studies.
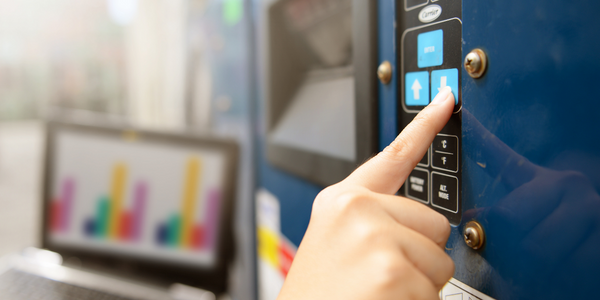
Case Study
Remote Temperature Monitoring of Perishable Goods Saves Money
RMONI was facing temperature monitoring challenges in a cold chain business. A cold chain must be established and maintained to ensure goods have been properly refrigerated during every step of the process, making temperature monitoring a critical business function. Manual registration practice can be very costly, labor intensive and prone to mistakes.
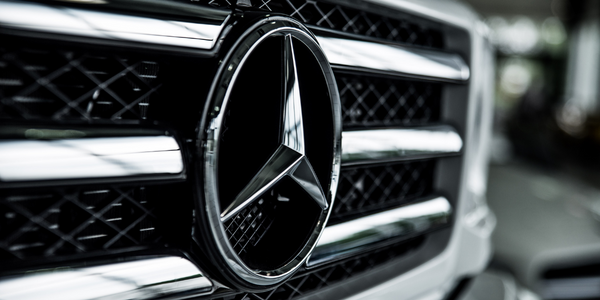
Case Study
Integral Plant Maintenance
Mercedes-Benz and his partner GAZ chose Siemens to be its maintenance partner at a new engine plant in Yaroslavl, Russia. The new plant offers a capacity to manufacture diesel engines for the Russian market, for locally produced Sprinter Classic. In addition to engines for the local market, the Yaroslavl plant will also produce spare parts. Mercedes-Benz Russia and his partner needed a service partner in order to ensure the operation of these lines in a maintenance partnership arrangement. The challenges included coordinating the entire maintenance management operation, in particular inspections, corrective and predictive maintenance activities, and the optimizing spare parts management. Siemens developed a customized maintenance solution that includes all electronic and mechanical maintenance activities (Integral Plant Maintenance).