Technology Category
- Analytics & Modeling - Digital Twin / Simulation
- Sensors - Autonomous Driving Sensors
Applicable Industries
- Automotive
- Metals
Applicable Functions
- Product Research & Development
- Quality Assurance
Use Cases
- Virtual Prototyping & Product Testing
- Virtual Reality
Services
- System Integration
- Testing & Certification
About The Customer
PWO Germany (Progress-Werk Oberkirch AG) is a leading supplier of high-precision metal components for the automotive industry, specializing in vehicle safety and comfort. The company has nearly ninety years of expertise in metal forming and joining technologies. PWO's German production site in Oberkirch employs around 1,100 people, and with additional sites in the Czech Republic, China, Mexico, and Canada, the company has a global presence with a total workforce of around 1,900 employees. PWO acts as a partner to the automotive industry in the development and production of innovative products, manufacturing millions of components on a just-in-time and zero-defect basis.
The Challenge
In 2008, PWO Germany was tasked with the development and production of a new steel automotive cross car beam (CCB) for the dashboard of a new car. The challenge was to develop this component based on the CAD model, design space definition, and other pre-defined standards provided by the customer. The component had to meet various specifications related to modal analyses and dynamic loads, which were determined by the expected use of the component. For instance, the eigenfrequency of the cross car beam, when connected to the steering wheel, could not exceed a certain preset value to avoid undesirable vibrations within the vehicle at certain speeds. Other specifications were related to crash and vehicle safety. The challenge was to meet these often conflicting specifications while developing the component in a timely and cost-effective manner.
The Solution
PWO used the HyperWorks Suite to develop the component. HyperMesh was used to convert the CAD model into a FEA model, which was then used for dedicated analysis and simulation tasks. To meet the requirements for crash and modal analysis, OptiStruct was used to optimize the component, while RADIOSS and other external solvers were used to run the calculations. HyperView was used for post-processing, and HyperForm was used to check the production feasibility of the individual components and for metal forming simulation tasks. The entire system was analyzed and specifications were met before a prototype was built. The results were validated with physical testing, which showed a very good correlation with the simulation results.
Operational Impact
Quantitative Benefit
Case Study missing?
Start adding your own!
Register with your work email and create a new case study profile for your business.
Related Case Studies.
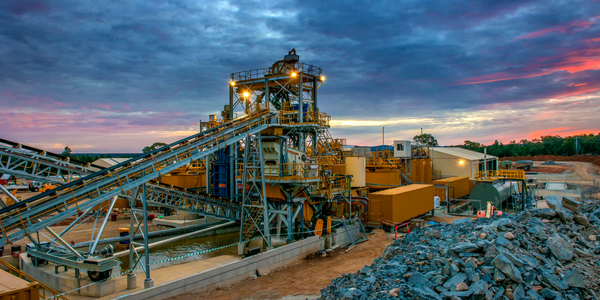
Case Study
Goldcorp: Internet of Things Enables the Mine of the Future
Goldcorp is committed to responsible mining practices and maintaining maximum safety for its workers. At the same time, the firm is constantly exploring ways to improve the efficiency of its operations, extend the life of its assets, and control costs. Goldcorp needed technology that can maximize production efficiency by tracking all mining operations, keep employees safe with remote operations and monitoring of hazardous work areas and control production costs through better asset and site management.
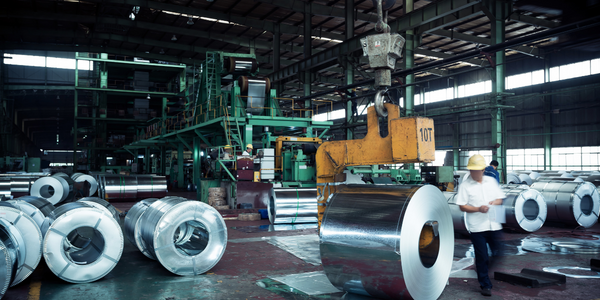
Case Study
KSP Steel Decentralized Control Room
While on-site in Pavlodar, Kazakhstan, the DAQRI team of Business Development and Solutions Architecture personnel worked closely with KSP Steel’s production leadership to understand the steel production process, operational challenges, and worker pain points.
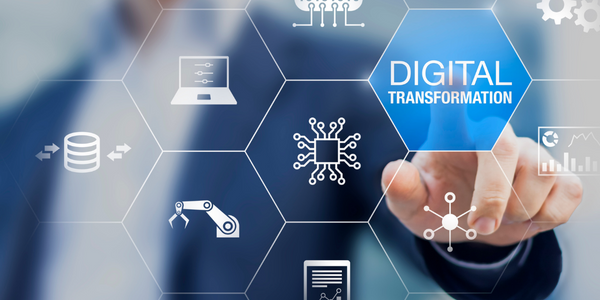
Case Study
Bluescope Steel on Path to Digitally Transform Operations and IT
Increasing competition and fluctuations in the construction market prompted BlueScope Steel to look toward digital transformation of its four businesses, including modern core applications and IT infrastructure. BlueScope needed to modernize its infrastructure and adopt new technologies to improve operations and supply chain efficiency while maintaining and updating an aging application portfolio.
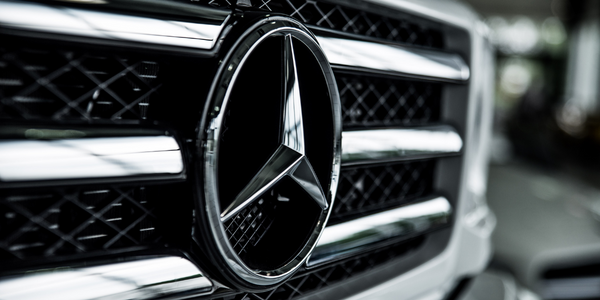
Case Study
Integral Plant Maintenance
Mercedes-Benz and his partner GAZ chose Siemens to be its maintenance partner at a new engine plant in Yaroslavl, Russia. The new plant offers a capacity to manufacture diesel engines for the Russian market, for locally produced Sprinter Classic. In addition to engines for the local market, the Yaroslavl plant will also produce spare parts. Mercedes-Benz Russia and his partner needed a service partner in order to ensure the operation of these lines in a maintenance partnership arrangement. The challenges included coordinating the entire maintenance management operation, in particular inspections, corrective and predictive maintenance activities, and the optimizing spare parts management. Siemens developed a customized maintenance solution that includes all electronic and mechanical maintenance activities (Integral Plant Maintenance).
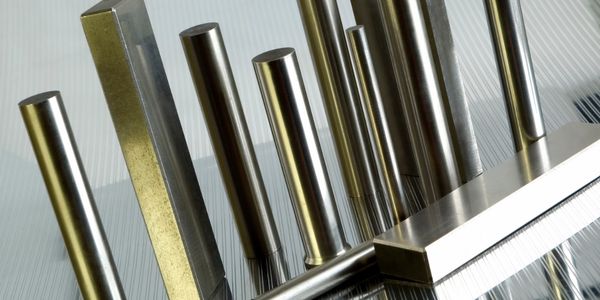
Case Study
RobotStudio Case Study: Benteler Automobiltechnik
Benteler has a small pipe business area for which they produce fuel lines and coolant lines made of aluminum for Porsche and other car manufacturers. One of the problems in production was that when Benteler added new products, production had too much downtime.