SUNGJIN FO-MA's Use of AFDEX for Improved Quality and Productivity in Automobile Component Precision Forgings
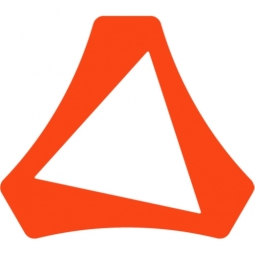
Technology Category
- Analytics & Modeling - Digital Twin / Simulation
Applicable Industries
- Automotive
Applicable Functions
- Product Research & Development
- Quality Assurance
Use Cases
- Digital Twin
- Virtual Reality
Services
- Testing & Certification
About The Customer
SUNGJIN FO-MA Inc. is a global company that specializes in cold forging. The company, established in 1986, prioritizes customer satisfaction and believes in constant and strategic innovation for sustainable growth. It has received the SQ Mark certificate from Hyundai and Kia Motors – Forging in 2001 and the INNO-BIZ certificate from the Korean government due to its heavy emphasis on innovation and expertise in forging technology. Over the years, SUNGJIN FO-MA has received various technical excellence awards and strongly advocates the use of simulation technology to achieve the best quality at a competitive price. The company attributes its long-term success to its consumers, employees, and technology.
The Challenge
SUNGJIN FO-MA Inc., a global company specializing in cold forging, faced a significant challenge in the prediction of precision forging processes with springback. Precision forging is a process where tight tolerances are a must, and the phenomenon of springback has a significant influence on the final shape of the product. Conventional forging processes are followed by cutting or trimming to achieve the final shape of the desired product. However, in precision forging, the springback phenomenon has to be considered during process design. The company was particularly concerned with the forging process of the intermediate yoke, a critical steering component, where the springback phenomenon is predominant in the region between the two ears.
The Solution
To tackle this challenge, SUNGJIN FO-MA turned to the elasto-plastic module of AFDEX through the Altair Partner Alliance. The company had realized the importance of FEM simulation of forging processes long back and now wanted to accurately predict the springback phenomenon. The intermediate yoke's forging process was simulated using AFDEX. During the unloading of the punch (5th stage), the two ears came closer towards each other due to springback. This springback amount was predicted and compared with experiments, and it was found that the simulation results matched very well. The use of AFDEX allowed SUNGJIN FO-MA to better design their process, increase productivity, and produce high-quality components.
Operational Impact
Quantitative Benefit
Case Study missing?
Start adding your own!
Register with your work email and create a new case study profile for your business.
Related Case Studies.
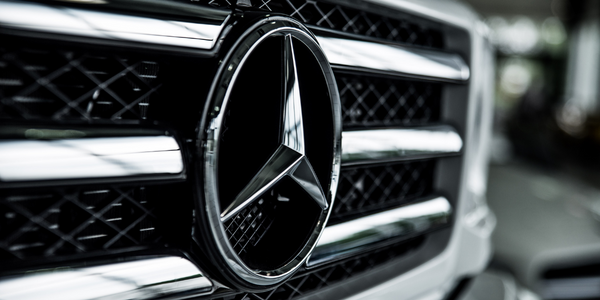
Case Study
Integral Plant Maintenance
Mercedes-Benz and his partner GAZ chose Siemens to be its maintenance partner at a new engine plant in Yaroslavl, Russia. The new plant offers a capacity to manufacture diesel engines for the Russian market, for locally produced Sprinter Classic. In addition to engines for the local market, the Yaroslavl plant will also produce spare parts. Mercedes-Benz Russia and his partner needed a service partner in order to ensure the operation of these lines in a maintenance partnership arrangement. The challenges included coordinating the entire maintenance management operation, in particular inspections, corrective and predictive maintenance activities, and the optimizing spare parts management. Siemens developed a customized maintenance solution that includes all electronic and mechanical maintenance activities (Integral Plant Maintenance).
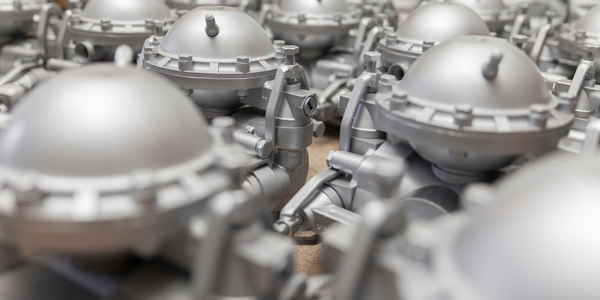
Case Study
Monitoring of Pressure Pumps in Automotive Industry
A large German/American producer of auto parts uses high-pressure pumps to deburr machined parts as a part of its production and quality check process. They decided to monitor these pumps to make sure they work properly and that they can see any indications leading to a potential failure before it affects their process.