Customer Company Size
Startup
Region
- America
Country
- Canada
Product
- E2 Manufacturing System
Implementation Scale
- Enterprise-wide Deployment
Impact Metrics
- Productivity Improvements
- Cost Savings
Technology Category
- Functional Applications - Manufacturing Execution Systems (MES)
Applicable Industries
- Oil & Gas
Applicable Functions
- Discrete Manufacturing
Use Cases
- Manufacturing System Automation
Services
- System Integration
About The Customer
Bhurjee Industries is a small job shop based in Edmonton, Alberta, Canada. The company is run by Raj Bhurjee, the Operations Manager, who comes from a long line of machinists, shop owners, and tech-savvy engineers. The company has a strong focus on technological advancement, a trait Raj attributes to his father's love of technology. Bhurjee Industries specializes in creating customized mounting kits for the oil and gas industry. These kits are designed to fit a wide variety of valves and actuators, providing a versatile solution for their customers. Despite the small size of the company, with just 8 employees, Bhurjee Industries is described as strong, advanced, flexible, and innovative.
The Challenge
Bhurjee Industries, a small job shop in Edmonton, Alberta, Canada, faced a significant challenge during the economic downturn in 2014. Many shops in their area were closing, and the company was struggling to keep up with the influx of work. The company was also transitioning to focus on their own product, customized mounting kits for the oil and gas industry. These kits required multi-fit parts that could accommodate a wide variety of valve and actuator brands. Managing the ins and outs of 300-400 jobs at a time was proving to be a logistical nightmare.
The Solution
In the midst of the economic downturn, Bhurjee Industries made the decision to invest in the E2 Manufacturing System. This management software system allowed the company to keep up with the increased workload resulting from other shops in the area closing. The E2 Manufacturing System also provided significant benefits in managing the production of their customized mounting kits. The Quality Module of the system helped with ISO audits and ensured the delivery of quality products on time. The system also provided accurate estimates of job costs and timing, ensuring competitiveness in the market. The E2 Manufacturing System enabled Bhurjee Industries to develop into a self-assemble shop, effectively managing the numerous jobs running at any given time.
Operational Impact
Case Study missing?
Start adding your own!
Register with your work email and create a new case study profile for your business.
Related Case Studies.
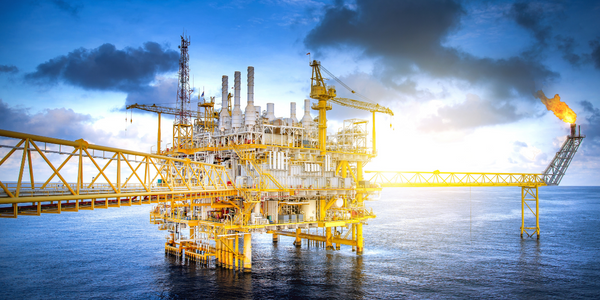
Case Study
Taking Oil and Gas Exploration to the Next Level
DownUnder GeoSolutions (DUG) wanted to increase computing performance by 5 to 10 times to improve seismic processing. The solution must build on current architecture software investments without sacrificing existing software and scale computing without scaling IT infrastructure costs.
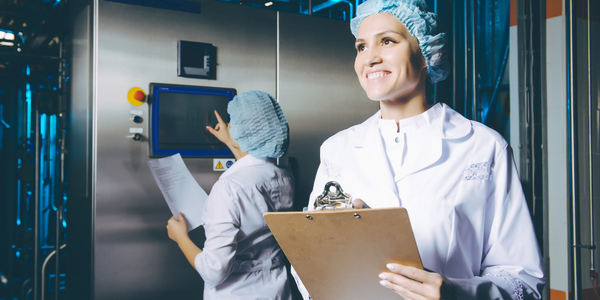
Case Study
Remote Wellhead Monitoring
Each wellhead was equipped with various sensors and meters that needed to be monitored and controlled from a central HMI, often miles away from the assets in the field. Redundant solar and wind generators were installed at each wellhead to support the electrical needs of the pumpstations, temperature meters, cameras, and cellular modules. In addition to asset management and remote control capabilities, data logging for remote surveillance and alarm notifications was a key demand from the customer. Terra Ferma’s solution needed to be power efficient, reliable, and capable of supporting high-bandwidth data-feeds. They needed a multi-link cellular connection to a central server that sustained reliable and redundant monitoring and control of flow meters, temperature sensors, power supply, and event-logging; including video and image files. This open-standard network needed to interface with the existing SCADA and proprietary network management software.
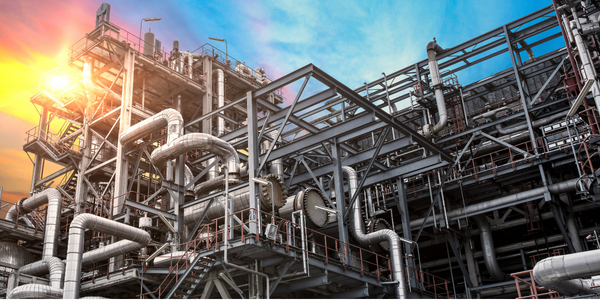
Case Study
Refinery Saves Over $700,000 with Smart Wireless
One of the largest petroleum refineries in the world is equipped to refine various types of crude oil and manufacture various grades of fuel from motor gasoline to Aviation Turbine Fuel. Due to wear and tear, eight hydrogen valves in each refinery were leaking, and each cost $1800 per ton of hydrogen vented. The plant also had leakage on nearly 30 flare control hydrocarbon valves. The refinery wanted a continuous, online monitoring system that could catch leaks early, minimize hydrogen and hydrocarbon production losses, and improve safety for maintenance.