Technology Category
- Functional Applications - Computerized Maintenance Management Systems (CMMS)
- Networks & Connectivity - WiFi
Applicable Industries
- Paper & Pulp
- Telecommunications
Applicable Functions
- Maintenance
Use Cases
- Asset Health Management (AHM)
- Predictive Maintenance
Services
- Training
About The Customer
Addison-HVAC is a well-established manufacturer of dedicated outdoor air systems (DOAS) based in Orlando, Florida. The company specializes in HVAC cooling and dehumidification equipment for commercial and industrial applications, offering a variety of energy-efficient options. The maintenance team at Addison-HVAC consists of five technicians, including a maintenance supervisor. The team previously relied on manual processes for managing maintenance activities, which were inefficient and messy due to the nature of their work.
The Challenge
Addison-HVAC, a leading DOAS manufacturer based in Orlando, Florida, faced significant challenges in managing their maintenance activities. The company employed a team of five technicians, including a maintenance supervisor, who relied on a physical paper request box and an Excel spreadsheet for managing maintenance tasks. This manual process was not only time-consuming but also messy, as technicians often had grease on their hands from working. Moreover, the team had limited Wi-Fi or internet access about 70% of the time due to spotty coverage inside the facility and remote work locations. This lack of consistent internet access posed a significant challenge to the efficient execution and recording of maintenance tasks.
The Solution
The implementation of UpKeep's new offline mobile capabilities revolutionized Addison-HVAC's maintenance operations. The solution allowed for the creation of digital work orders that could be systematically reviewed, assigned, and completed. The offline mobile capabilities provided a seamless transition between offline and online situations, enabling technicians to work uninterrupted even without Wi-Fi or internet access. All necessary information, such as pictures and checklists, was automatically available offline, and work orders would sync once a Wi-Fi connection was re-established. The solution was intuitive and user-friendly, requiring no additional training for the team.
Operational Impact
Quantitative Benefit
Case Study missing?
Start adding your own!
Register with your work email and create a new case study profile for your business.
Related Case Studies.
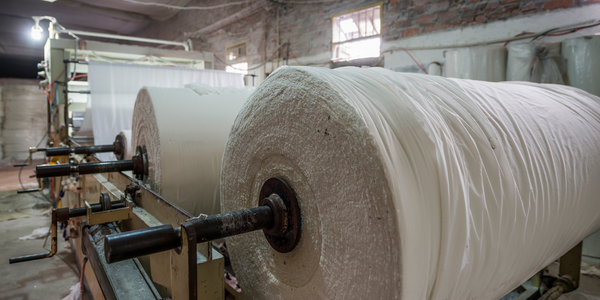
Case Study
Wireless Improves Efficiency in Compressed Air Systems
Hollingsworth and Vose wanted to improve the efficiency of their compressed air system, lower the electricity expense component of manufacturing cost in their commodity industry, and conserve energy leading to lowered greenhouse gas emissions. Compressed air systems degrade over time and become leaky and inefficient. Hollingsworth and Vose wanted to increase the frequency of system inspections without paying the high cost of manual labor.
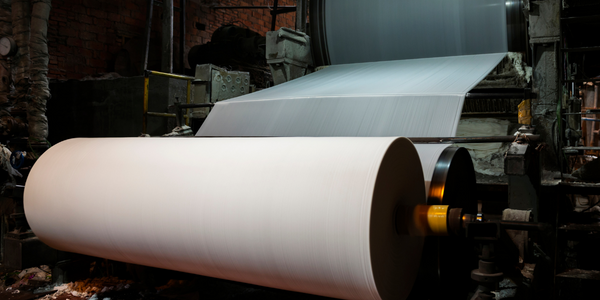
Case Study
Process Predictive Analysis in Pulp and Paper Mill
Common paper breaks consequently lead up to 60 minutes of downtime, delaying a potential $10K per hour of production value process. Thus, defective products cause financial and damage company's reputation. Improving quality and reducing defect rates can generate millions of dollars of revenue per year for your company.
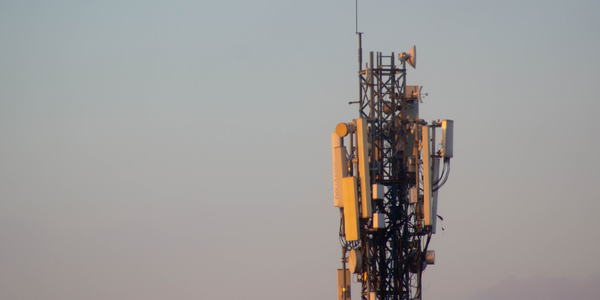
Case Study
Vodafone Hosted On AWS
Vodafone found that traffic for the applications peak during the four-month period when the international cricket season is at its height in Australia. During the 2011/2012 cricket season, 700,000 consumers downloaded the Cricket Live Australia application. Vodafone needed to be able to meet customer demand, but didn’t want to invest in additional resources that would be underutilized during cricket’s off-season.