Customer Company Size
Large Corporate
Region
- America
Country
- United States
Product
- Gathr
Tech Stack
- IoT
- Machine Learning
- Real-time Data Processing
Implementation Scale
- Enterprise-wide Deployment
Impact Metrics
- Productivity Improvements
- Cost Savings
Technology Category
- Analytics & Modeling - Predictive Analytics
Applicable Industries
- Automotive
Applicable Functions
- Maintenance
- Discrete Manufacturing
Use Cases
- Predictive Maintenance
- Real-Time Location System (RTLS)
Services
- Data Science Services
- System Integration
About The Customer
The customer is a Fortune 500 American multinational automaker. They are one of the world's largest automotive manufacturers, with thousands of machines in their manufacturing unit generating millions of events every minute. The company was looking for a solution that could predict faults in their auto parts to proactively ensure fault-free production. This would not only save maintenance time but also improve the customer experience. The company needed a solution that could handle data from multiple discrete systems, process it in real-time, and provide alerts to floor operators and the downstream application.
The Challenge
A Fortune 500 American multinational automaker was seeking a solution to predict faults in their auto parts to proactively ensure fault-free production, thereby saving maintenance time and improving the customer experience. The company faced several challenges. Data was being generated from multiple discrete systems, all of which had to be processed simultaneously to get a complete picture. The data was in different formats like JSON, CSV, and other proprietary formats. The cutting tools had to be replaced before they reached end-of-life, affecting the production quality. Therefore, the automaker was looking for a solution that would predict in real-time, giving them enough time to replace the waned cutting tools. The data collected from multiple systems had several quality issues and missing records. This data had to be formatted, cleansed, and prepared before it could be fed into the predictive analytics models. The manufacturing unit had thousands of machines generating millions of events every minute. The automaker needed to process this massive amount of data in real-time using a single solution and shared infrastructure. Real-time alerts to floor operators and the downstream application was a crucial component. Any failure or delay in these alerts had a direct impact on the quality of parts produced.
The Solution
The automaker deployed Gathr in their auto-parts manufacturing division to collect data from various sources, combine them, and predict the life of the cutting tools used to create auto parts. Gathr enabled the client to implement an end-to-end predictive maintenance solution leveraging out-of-the-box drag-and-drop operators. It helped them effortlessly design a complete solution with the following ready-to-use capabilities: Reading data from various sources, Out-of-the-box data-wrangling transformations, Data quality management, Rule-based, Scalable scoring of trained models, Data aggregation, Data profiling, Monitoring and reporting. To build a predictive maintenance solution for tool replacement, Gathr implemented a five-stage approach: Real-time data ingestion, Data cleansing and integration, Data transformation and online scoring, Real-time alerts, Monitoring and dashboard.
Operational Impact
Quantitative Benefit
Case Study missing?
Start adding your own!
Register with your work email and create a new case study profile for your business.
Related Case Studies.
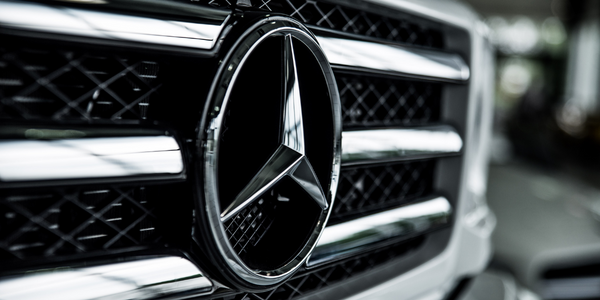
Case Study
Integral Plant Maintenance
Mercedes-Benz and his partner GAZ chose Siemens to be its maintenance partner at a new engine plant in Yaroslavl, Russia. The new plant offers a capacity to manufacture diesel engines for the Russian market, for locally produced Sprinter Classic. In addition to engines for the local market, the Yaroslavl plant will also produce spare parts. Mercedes-Benz Russia and his partner needed a service partner in order to ensure the operation of these lines in a maintenance partnership arrangement. The challenges included coordinating the entire maintenance management operation, in particular inspections, corrective and predictive maintenance activities, and the optimizing spare parts management. Siemens developed a customized maintenance solution that includes all electronic and mechanical maintenance activities (Integral Plant Maintenance).
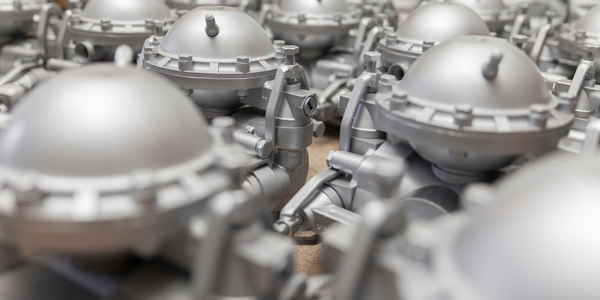
Case Study
Monitoring of Pressure Pumps in Automotive Industry
A large German/American producer of auto parts uses high-pressure pumps to deburr machined parts as a part of its production and quality check process. They decided to monitor these pumps to make sure they work properly and that they can see any indications leading to a potential failure before it affects their process.