As Broadcom’s “Go-To” Analytics Platform, Incorta Speeds Access to Information and Improves Employee Productivity
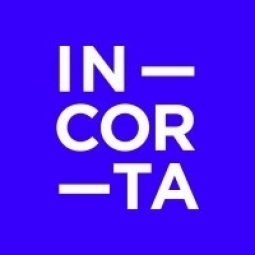
Customer Company Size
Large Corporate
Region
- America
Country
- United States
Product
- Incorta Analytics Platform
Tech Stack
- Oracle ERP
- Microsoft Excel
- Workday
- Model N
- Oracle Demantra
Implementation Scale
- Enterprise-wide Deployment
Impact Metrics
- Productivity Improvements
- Cost Savings
Technology Category
- Analytics & Modeling - Real Time Analytics
Applicable Industries
- Semiconductors
Applicable Functions
- Business Operation
Use Cases
- Real-Time Location System (RTLS)
- Predictive Quality Analytics
Services
- Data Science Services
About The Customer
Broadcom is a global communications semiconductor powerhouse built on 50 years of innovation, collaboration, and engineering excellence. As a leading designer, developer, and supplier of a broad range of digital and analog semiconductor connectivity solutions, Broadcom serves the wired infrastructure, wireless communications, enterprise storage, and industrial markets. Broadcom has built a reputation as a true innovator, not only in how they’ve aggressively grown their business, but also in how they tackle the challenges of running their internal systems to keep pace with that growth. Multiple business units at Broadcom make decisions relying on information housed in a variety of software solutions, including Workday, Oracle ERP, Model N, Oracle Demantra, and Microsoft Excel.
The Challenge
Broadcom, a global communications semiconductor powerhouse, was facing challenges in generating new analytical dashboards or reports based on data from various software solutions, including Workday, Oracle ERP, Model N, Oracle Demantra, and Microsoft Excel. The process was time-consuming, taking up to twelve weeks. As technology advanced, Broadcom sought to shorten this dashboard and report development cycle and reduce report run times. The company was looking for a solution that could integrate with other applications, especially Microsoft Excel, which is used by 90% of the company. The solution also needed to be cost-effective, easy to maintain, and minimize the number of peripheral technologies required for solution support.
The Solution
Broadcom found a solution in Incorta’s analytics platform. Incorta easily combines data from crucial enterprise systems, enables access to point solutions like Excel, and accelerates the creation of new analytical applications while also reducing report run times. Incorta’s innovative Direct Data Mapping architecture aggregates complex business data in real-time, eliminating the need for a data warehouse and traditional star schema approach. By completely removing the need for costly join operations, Incorta reduces report run times from hours to seconds and lets users create new reports and dashboards in days instead of months. Incorta simplifies security by offering single sign-on and the ability to retain other applications’ security parameters—including row-level security for data access.
Operational Impact
Quantitative Benefit
Case Study missing?
Start adding your own!
Register with your work email and create a new case study profile for your business.
Related Case Studies.
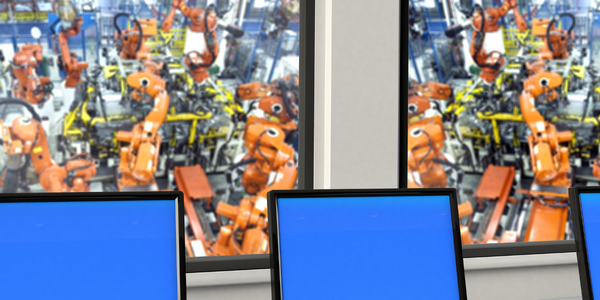
Case Study
KINESYS Semiconductor Factory Automation Software
KINESYS Software provides both Integrated Device Manufacturer (IDM) and Original Equipment Manufacturer (OEM) customers world-class software products and solutions for advanced wafer and device traceability and process management. KINESYS offers state of the art database technology with a core focus on SEMI standards. KINESYS’ challenge was to make back-end processing failure-free and easy to use for clients while supporting licensing models more adaptable to changing industry needs.
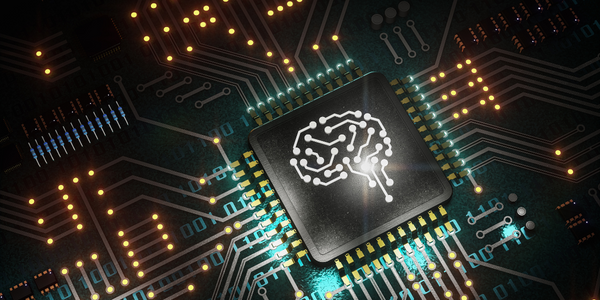
Case Study
Modular AI Defect Inspection Solution for Efficient Semiconductor Equipment Upgrades
Smasoft Technology Co., Ltd., a System Integrator that develops industrial automation software and offers AI application solutions, was commissioned by a semiconductor equipment manufacturer to implement AI inspection features into their Extreme Ultraviolet Light (EUV) pod inspection machines. The existing AOI software in the EUV pod inspection machines could only identify defective products but could not trace the cause of the defects. The manufacturer wanted to upgrade their machines with AI features to make the products more useful. The AI solution needed to complete the analysis of 380 images for a single pod within two minutes and inspect different materials simultaneously. This required multiple sets of AI models for interpretation. The solution also needed to be installed in a cabinet in the lower half of the machines, which posed a challenge due to the limited space. Smasoft needed to purchase a hardware solution with strong computing performance, stable operation, compact size, and flexible configuration to overcome these challenges.
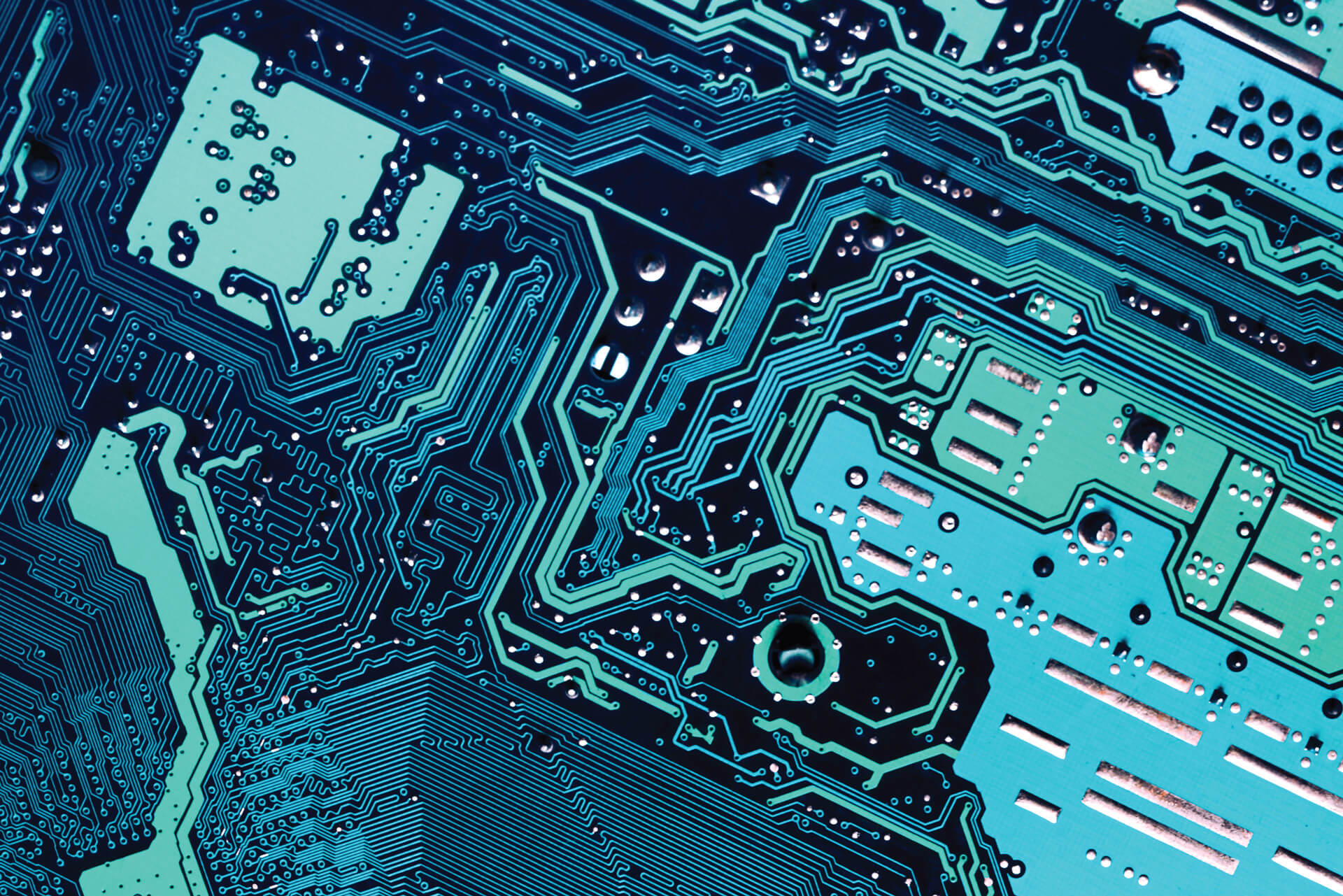
Case Study
Optimizing Semiconductor Manufacturing Yield with IoT
A large U.S.-based manufacturer of high-performance semiconductors was facing a significant challenge in optimizing the manufacturing process of its wireless products. The company, which designs and delivers a broad set of cutting-edge products including radio frequency filters, amplifiers, modulators, attenuators, and more, was experiencing lower than expected overall yield in some of its most complex products. This was affecting the company's productivity and profitability, and there was a need for a solution that could predict low-yield wafers early in the process and identify process improvements to increase overall yield.
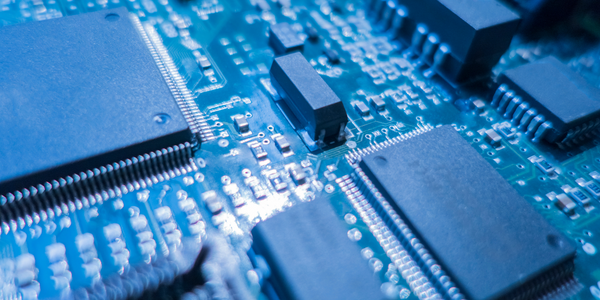
Case Study
Rapid Hybrid Services Deployment for Global Semiconductor Company
The U.S. manufacturer of engineered materials, optoelectronic components, and semiconductors was focused on growth through mergers and acquisitions (M&As). In 2019–2020, it acquired a global electronics firm and needed immediate connectivity and visibility into the acquired firm’s geo-distributed operations. The company had a highly compressed timeline, with only days to integrate the firm’s DDI operations, while deferring a full network migration to a future date. The company was actively engaged in acquiring and merging strategically aligned companies as a key global growth strategy. The company needed to rapidly integrate its new operations, which included significant remote locations in Asia. The company turned to Infoblox to quickly design a highly secure, available, and reliable solution that could deliver full visibility into new sites. It needed dynamic scalability to accommodate its growing operations and the ability to unify a disparate, geo-diverse infrastructure.
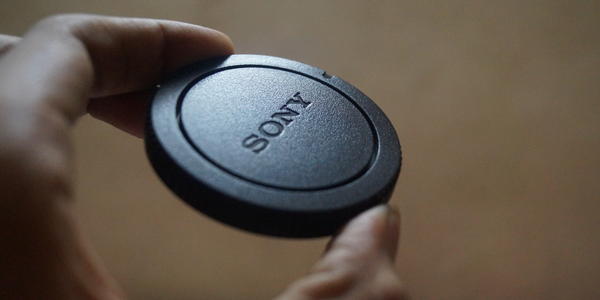
Case Study
Sony Italia's Server Consolidation: A Cost-Saving Success
Sony Italia, a branch of the global electronics giant Sony Corporation, was facing a significant challenge with its IT infrastructure. The company had consolidated most of its IT infrastructure into two data centers in the U.K, but Sony Italia opted to maintain its local server infrastructure for high performance and ease of maintenance. However, as data volumes and user numbers grew, the servers began to experience reduced performance and reliability. The company had 30 physical servers, but with limited budgets, replacing all of them was not feasible. Additionally, Sony Italia was concerned about the increasing heat output and electricity consumption in the data center. The company had already virtualized about half of its infrastructure, but needed a more cost-effective solution to extend these benefits.