Asahi Kasei Plastics North America Leverages eMaint X5 and Power BI for Enhanced Maintenance Management
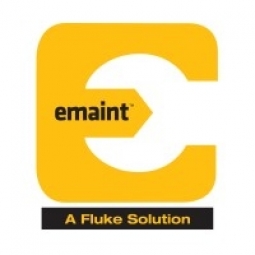
Technology Category
- Application Infrastructure & Middleware - Data Visualization
- Functional Applications - Computerized Maintenance Management Systems (CMMS)
Applicable Industries
- Automotive
- Plastics
Applicable Functions
- Facility Management
- Maintenance
Use Cases
- Machine Condition Monitoring
- Track & Trace of Assets
Services
- System Integration
About The Customer
Asahi Kasei Plastics North America, headquartered in Fowlerville, Michigan, is a leading plastics compounder that manufactures plastic pellets for automotive manufacturing, healthcare, and other industries. Most cars on the road feature their plastic. The company has multiple facilities and manages approximately 2,000 assets. The company began using eMaint more than 10 years ago and has 45 people using eMaint X5, including maintenance technicians and lab workers. The company's customers rely on them for the reliable delivery of plastic pellets and need assurance that equipment is being properly maintained and that critical spare parts are kept on hand in case of a failure.
The Challenge
Asahi Kasei Plastics North America, a leading plastics compounder, was facing several challenges in managing preventive maintenance across its multiple facilities in Fowlerville, Michigan, and Athens, Alabama. The company had to manage around 2,000 assets, including extruders, feeders, hoppers, and plant support equipment. The plant support equipment was critical as it serviced multiple lines, and its downtime could halt multiple production lines. The company needed a Computerized Maintenance Management System (CMMS) that could seamlessly manage multiple plants on one system. Another challenge was customer audits. Asahi Kasei's customers needed assurance that equipment was being properly maintained and that critical spare parts were available in case of a failure. The company was looking for a more streamlined alternative to pencil and paper to manage preventive maintenance on their equipment.
The Solution
Asahi Kasei Plastics North America adopted eMaint X5, a CMMS solution that allowed them to manage multiple plants on one system. The solution offered visibility and transparency to internal and external stakeholders through centralized dashboards and reports, helping the team stay on track with their preventive maintenance tasks. The company primarily used eMaint to track work orders and completion reports, and for quarterly cycle counts of their inventory to ensure that their physical on-hand inventory matches. Lab technicians also used it to maintain calibration tasks at the right frequency. The company integrated eMaint with their existing software systems and tools, including Power BI, a data visualization tool from Microsoft. With Power BI and eMaint, the team could review work order completion rates, compare metrics from both the team as a whole and at the individual technician level, and review late metrics and downtime.
Operational Impact
Quantitative Benefit
Case Study missing?
Start adding your own!
Register with your work email and create a new case study profile for your business.
Related Case Studies.
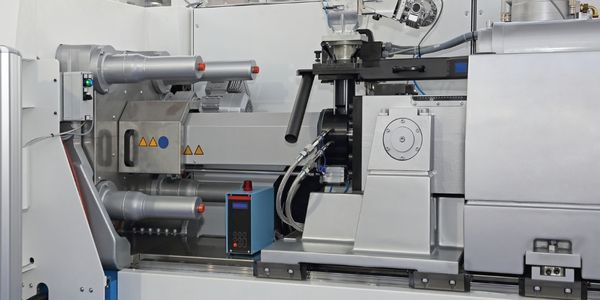
Case Study
Plastic Spoons Case study: Injection Moulding
In order to meet customer expectations by supplying a wide variety of packaging units, from 36 to 1000 spoons per package, a new production and packaging line needed to be built. DeSter wanted to achieve higher production capacity, lower cycle time and a high degree of operator friendliness with this new production line.
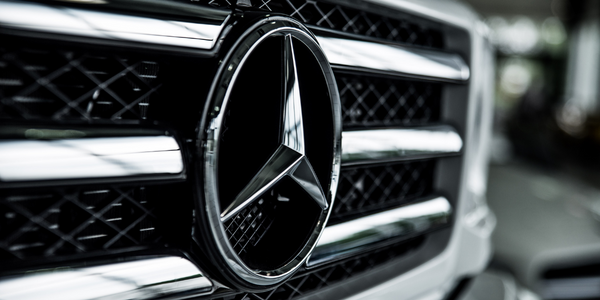
Case Study
Integral Plant Maintenance
Mercedes-Benz and his partner GAZ chose Siemens to be its maintenance partner at a new engine plant in Yaroslavl, Russia. The new plant offers a capacity to manufacture diesel engines for the Russian market, for locally produced Sprinter Classic. In addition to engines for the local market, the Yaroslavl plant will also produce spare parts. Mercedes-Benz Russia and his partner needed a service partner in order to ensure the operation of these lines in a maintenance partnership arrangement. The challenges included coordinating the entire maintenance management operation, in particular inspections, corrective and predictive maintenance activities, and the optimizing spare parts management. Siemens developed a customized maintenance solution that includes all electronic and mechanical maintenance activities (Integral Plant Maintenance).
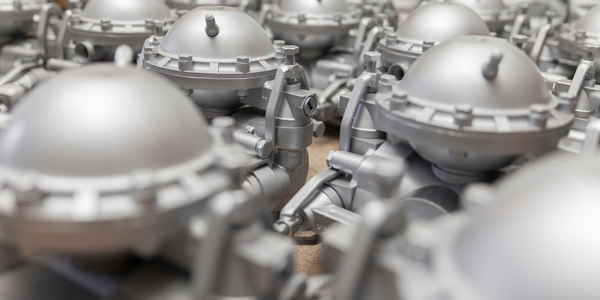
Case Study
Monitoring of Pressure Pumps in Automotive Industry
A large German/American producer of auto parts uses high-pressure pumps to deburr machined parts as a part of its production and quality check process. They decided to monitor these pumps to make sure they work properly and that they can see any indications leading to a potential failure before it affects their process.