Auto Parts Maker Wins Productivity Race with NComputing
Customer Company Size
Mid-size Company
Region
- America
Country
- United States
Product
- NComputing L-series
- NComputing virtualization software
Tech Stack
- Virtual Desktop Infrastructure
- Wireless Network Integration
Implementation Scale
- Enterprise-wide Deployment
Impact Metrics
- Cost Savings
- Productivity Improvements
- Environmental Impact Reduction
Technology Category
- Platform as a Service (PaaS) - Device Management Platforms
- Networks & Connectivity - Wireless Local Area Network
Applicable Industries
- Automotive
Applicable Functions
- Facility Management
- Business Operation
Use Cases
- Factory Operations Visibility & Intelligence
- Remote Asset Management
Services
- System Integration
- Hardware Design & Engineering Services
About The Customer
BLD Products is a manufacturer specializing in quality emission and engine control products for automobiles and trucks. The company supplies parts to both original equipment manufacturers and the aftermarket. Based in Holland, Michigan, BLD's manufacturing operations encompass light assembly, machining, welding, injection molding, and stamping. Operating in the intensely competitive global parts business, BLD relies heavily on factory automation to drive productivity and quality. The company faces the challenge of maintaining high uptime to meet production goals while managing tight industry margins. As a mid-sized company, BLD is focused on cost-effectively upgrading its computing infrastructure to support its manufacturing processes.
The Challenge
BLD Products, a manufacturer of emission and engine control products, faced the challenge of upgrading their outdated computing infrastructure. Their existing PCs were nearly six years old, running obsolete operating systems, and were not cost-effective to replace entirely. The company needed a solution that would ensure high uptime in their harsh manufacturing environment while keeping computing costs under control. They considered a thin-client solution but found the upfront costs for servers, software, and network equipment to be prohibitive. BLD sought an affordable alternative that could meet their specific needs and improve their factory automation systems.
The Solution
BLD Products partnered with GHA Technologies, an NComputing solution partner, to deploy the NComputing L-series virtual desktop solution. This solution allowed BLD to use a ratio of four L-series devices per shared PC, effectively leveraging the unused capacity of modern PCs. The NComputing devices, which have no CPU, memory, or moving parts, are rugged and easy to maintain, making them suitable for BLD's harsh manufacturing environment. GHA Technologies conducted tests to ensure compatibility with BLD's wireless environment and USB-based barcode scanners. The tests confirmed that the NComputing solution worked well with the existing network and peripherals. The deployment of the L-series devices enabled BLD to replace only a quarter of their PCs, significantly reducing costs and increasing productivity.
Operational Impact
Quantitative Benefit
Case Study missing?
Start adding your own!
Register with your work email and create a new case study profile for your business.
Related Case Studies.
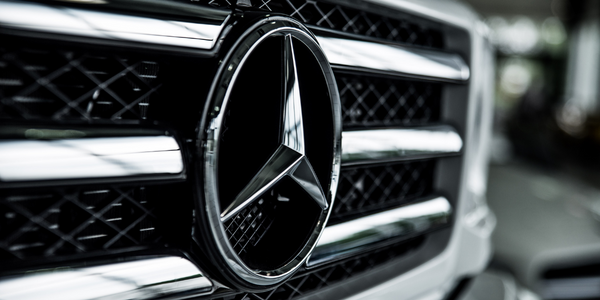
Case Study
Integral Plant Maintenance
Mercedes-Benz and his partner GAZ chose Siemens to be its maintenance partner at a new engine plant in Yaroslavl, Russia. The new plant offers a capacity to manufacture diesel engines for the Russian market, for locally produced Sprinter Classic. In addition to engines for the local market, the Yaroslavl plant will also produce spare parts. Mercedes-Benz Russia and his partner needed a service partner in order to ensure the operation of these lines in a maintenance partnership arrangement. The challenges included coordinating the entire maintenance management operation, in particular inspections, corrective and predictive maintenance activities, and the optimizing spare parts management. Siemens developed a customized maintenance solution that includes all electronic and mechanical maintenance activities (Integral Plant Maintenance).
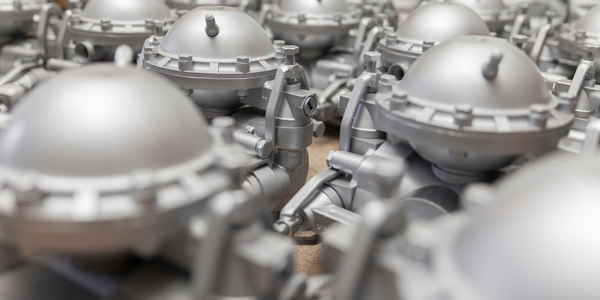
Case Study
Monitoring of Pressure Pumps in Automotive Industry
A large German/American producer of auto parts uses high-pressure pumps to deburr machined parts as a part of its production and quality check process. They decided to monitor these pumps to make sure they work properly and that they can see any indications leading to a potential failure before it affects their process.