Technology Category
- Cybersecurity & Privacy - Security Compliance
- Networks & Connectivity - 5G
Applicable Industries
- Cement
- Railway & Metro
Applicable Functions
- Maintenance
- Quality Assurance
Use Cases
- Construction Management
- Inventory Management
Services
- Testing & Certification
About The Customer
Network Certification Body (NCB) is a leading industry expert in railway assurance and certification on infrastructure, vehicle, and freight projects, both in the UK and worldwide. NCB works with clients to minimize compliance risk and adherence to rail infrastructure standards. It is driven by exceptional standards of safety and excellence to provide assurance and certification solutions. Accredited as a Notified Body, Designated Body, Assessment Body, Plant Assessment Body and an Entities in Charge of Maintenance Certification Body, NCB provides an unrivaled level of services across the railway system.
The Challenge
Network Certification Body (NCB), a leading provider of railway assurance and certification on infrastructure, vehicle, and freight projects in the UK and worldwide, was facing a challenge with its existing IT systems. With an average of 200 rail projects being delivered at any one time, safety was its first priority. However, the existing systems for managing assessment service delivery were inefficient. NCB needed to replace largely manual information management with automated document generation, while supporting the NCB’s Progressive Assurance Methodology. The new solution would need to administer complex document templates and facilitate efficient and effective client communications between NCB and its clients.
The Solution
The solution came in the form of the NCB Portal, built in low-code, which allowed NCB engineers to focus on assessment service delivery rather than administration activities. The portal improved compliance control and provided easier ways to manage information and ensure speedy assessment reporting. The Liberty on-premise adapter (OPA) provided functionality for complex document generation, merging personalized content with pre-defined Microsoft Word templates and allowing for large pdf generation. The NCB Portal also improved cost control and ensured templates were centrally managed. The new portal improved the flow of information between clients and assessors, enabling the project status to be clearly understood at any point in the project lifecycle. The NCB Portal gave all stakeholders visibility of assessment in real-time, enabling clients access to key assessment risks and findings.
Operational Impact
Quantitative Benefit
Case Study missing?
Start adding your own!
Register with your work email and create a new case study profile for your business.
Related Case Studies.
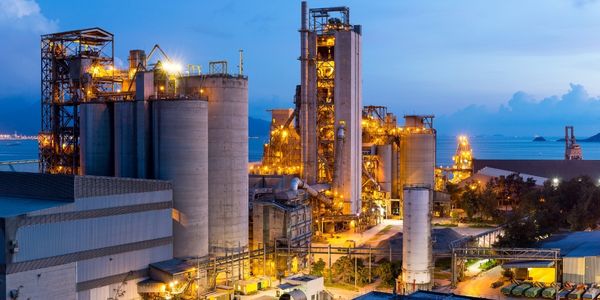
Case Study
System 800xA at Indian Cement Plants
Chettinad Cement recognized that further efficiencies could be achieved in its cement manufacturing process. It looked to investing in comprehensive operational and control technologies to manage and derive productivity and energy efficiency gains from the assets on Line 2, their second plant in India.
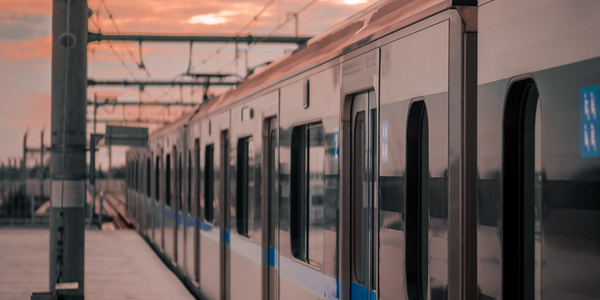
Case Study
Building Smart IoT-Connected Railways
• Difficult environment. Communications equipment on trains must function properly in harsh conditions, such as environment temperatures ranging from -25°C to +85°C, according to the EU standard EN50155.• Railway regulations. All products in a train must adhere to strict standards, relating to working vibration, power consumption, and lifetime.• Lengthy process. Time to market in the railway industry can take years from concept to mass production, so product design requires a solid long term vision.
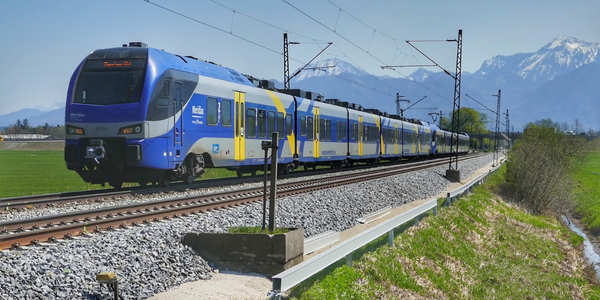
Case Study
Connected Transportation: A Smarter Brain for Your Train with Intel
A modern locomotive, for example, has as many as 200 sensors generating more than a billion data points per second. Vibration sensors surround critical components, video cameras scan the track and cab, while other sensors monitor RPM, power, temperature, the fuel mix, exhaust characteristics, and more.Most of today’s locomotives lack sufficient on-board processing power to make full use of all this data. To make matters worse, the data from different subsystems, such as the brakes, fuel system, and engine, remain separate, stored in isolated “boxes” that prevent unified analysis. The data is available, but the technology needed to process it in the most effective manner is not. As new sensors are added to the machine, the problem escalates.
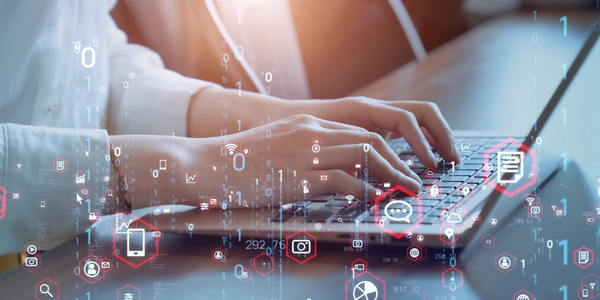
Case Study
Digital Transformation of Atlanta Grout & Tile: An IoT Case Study
Atlanta Grout & Tile, a Tile, Stone & Grout restoration company based in Woodstock, Georgia, was facing challenges with its traditional business model. Despite steady growth over the years, the company was falling behind the web revolution and missing out on the opportunity to tap into a new consumer base. They were using independent software from different vendors for each of their department information and workforce management. This resulted in a lot of manual work on excel and the need to export/import data between different systems. This not only increased overhead costs but also slowed down their response to clients. The company also had to prepare numerous reports manually and lacked access to customer trends for effective business decision-making.
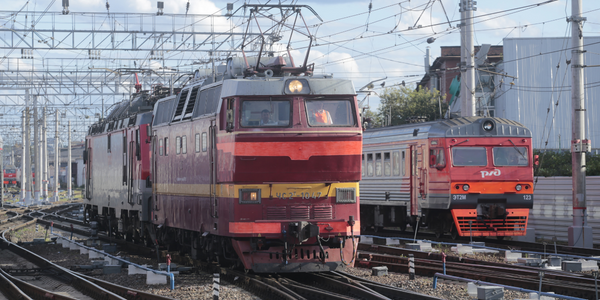
Case Study
Using LonWorks to Keep Acela Trains Zip Along
Canadian transportation company, Bombardier was tasked with building a bullet train system on rails that were designed for lower speed trains. In addition, they had to ensure safe and optimal operation at high speeds, maximize train uptime and enhance communication with passengers.