Boosting Warranty Reimbursements by 990%: A Case Study on Heyl Truck Lines
Technology Category
- Functional Applications - Computerized Maintenance Management Systems (CMMS)
- Functional Applications - Fleet Management Systems (FMS)
Applicable Industries
- Automotive
- Specialty Vehicles
Applicable Functions
- Logistics & Transportation
- Maintenance
Use Cases
- Fleet Management
- Transportation Simulation
Services
- System Integration
About The Customer
Heyl Truck Lines is an award-winning truck carrier based in Akron, Iowa. The company operates a fleet of 1,700 assets and specializes in hauling freight across the United States and Canada. Their freight primarily consists of temperature-controlled commodities and dry freight. In 2020, they embarked on a mission to find a software system that could integrate with their existing fleet management software solution, McLeod Loadmaster, and extend their maintenance automation capabilities. The company was particularly interested in improving their predictive and preventive maintenance process, warranty reimbursements, and repair and productivity visibility.
The Challenge
Heyl Truck Lines, an award-winning truck carrier based in Akron, Iowa, was in search of a maintenance software system that could integrate with their existing fleet management software, McLeod Loadmaster, and enhance their maintenance automation capabilities. The company, which operates a fleet of 1,700 assets and specializes in temperature-controlled commodities and dry freight, aimed to improve in three key areas: predictive and preventive maintenance process, warranty reimbursements, and repair and productivity visibility. Prior to implementing the Cetaris fleet maintenance software, Heyl was relying on a manual and memory-based system to flag and process warranty claims. This system was not only inefficient but also prone to human error, leading to missed warranty claims whenever the Service Writer forgot to flag them. Additionally, the manual system required road breakdown and shop personnel to understand warranty agreements across multiple suppliers, increasing the risk of warranty dollars slipping through the cracks unclaimed.
The Solution
Heyl Truck Lines adopted the Cetaris fleet maintenance software to address their challenges. The software has helped the company to continuously increase profitability across multiple areas, with the warranty module being a significant contributor. The Cetaris software has automated the process of flagging and processing warranty claims, eliminating the risk of human error and ensuring that no warranty dollars go unclaimed. A year after implementing the Cetaris warranty module, Heyl has seen a staggering 990% increase in warranty reimbursement between OEM, extended, and policy warranty. The company continues to explore new ways to fine-tune their maintenance operations, increase connectivity with integration, and improve their ROI with Cetaris. They are also preparing to implement part replacement warranty to further enhance warranty gains.
Operational Impact
Quantitative Benefit
Case Study missing?
Start adding your own!
Register with your work email and create a new case study profile for your business.
Related Case Studies.
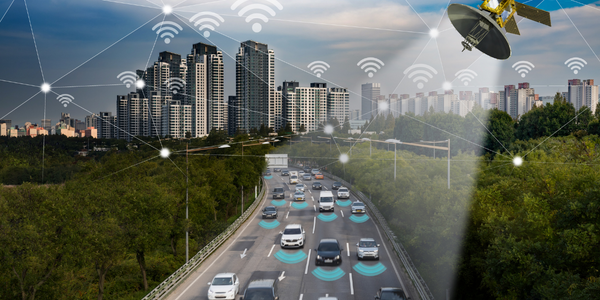
Case Study
Transformation for IoT Business Model in Connected Industrial Vehicles
CNH Industrial wanted to put IoT-enabled viechles onto the market. Whether monitoring a single machine or integrating an entire fleet, operators are able to track the status, speed, and movement of machines and their performance and also receive alerts on issues that may require service by a qualified technician to improve uptime and overall effectiveness of the vehicle.
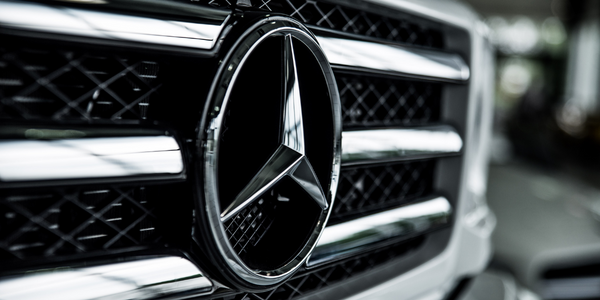
Case Study
Integral Plant Maintenance
Mercedes-Benz and his partner GAZ chose Siemens to be its maintenance partner at a new engine plant in Yaroslavl, Russia. The new plant offers a capacity to manufacture diesel engines for the Russian market, for locally produced Sprinter Classic. In addition to engines for the local market, the Yaroslavl plant will also produce spare parts. Mercedes-Benz Russia and his partner needed a service partner in order to ensure the operation of these lines in a maintenance partnership arrangement. The challenges included coordinating the entire maintenance management operation, in particular inspections, corrective and predictive maintenance activities, and the optimizing spare parts management. Siemens developed a customized maintenance solution that includes all electronic and mechanical maintenance activities (Integral Plant Maintenance).