Technology Category
- Networks & Connectivity - Gateways
- Sensors - Environmental Sensors
Applicable Industries
- Chemicals
- Electronics
Applicable Functions
- Product Research & Development
Use Cases
- Indoor Air Quality Monitoring
- Outdoor Environmental Monitoring
About The Customer
Bosch is a Fortune 100 company and one of the world’s largest suppliers of technology and services. It is an organization well aware of its social and environmental responsibility. For more than thirty years, Bosch has been developing corporate policies that protect people and the environment and reinforce the importance of sustainability. Bosch is a long-time user of Altium’s earlier design software, Protel99. As part of its continued efforts, Bosch decided to design its latest Rexroth Frequency Converter Fe series to be more economical and environmentally friendly.
The Challenge
Large corporations are increasingly under pressure to address environmental concerns while maintaining their business operations. The challenge lies in the perceived trade-off between corporate strategies and environmental responsibility. Many organizations struggle to see the opportunities in green engineering, while others are simply confused by the numerous principles and guidelines that can differ for each industry and organizational department. For instance, electronics engineers can influence the impact of their products by adhering to various design principles such as green engineering, sustainable design, green design, or design-for-environment. These principles share the same basic rules: make it smaller, more reliable, and consume less power. However, engineers must also consider product life cycle, reusability, and how to eliminate toxic chemicals before they can start touting themselves as ‘green engineers’.
The Solution
Bosch, a Fortune 100 company and one of the world’s largest suppliers of technology and services, decided to design its latest Rexroth Frequency Converter Fe series to be more economical and environmentally friendly. To realize the environmental objectives, the engineers needed to reduce parts, size, and power consumption, while improving reliability and stability. Bosch upgraded to Altium Designer, a tool that provides a user-friendly interface and improved features for board design. The engineers could exploit Altium’s intelligent pin and part swapping capabilities, which simplifies board layout, reduces the numbers of layers used, and overall board size. Bosch also took advantage of Altium’s high-speed capabilities to carefully control track clearances, track lengths, and trace widths to safeguard against integrity issues. Using Altium Designer’s integrated database libraries, Bosch could link into its various ERP systems to Altium Designer, allowing it to easily oversee suppliers, factory, reseller, and even customer information, monitor resources, and manage waste with greater efficiency.
Operational Impact
Case Study missing?
Start adding your own!
Register with your work email and create a new case study profile for your business.
Related Case Studies.
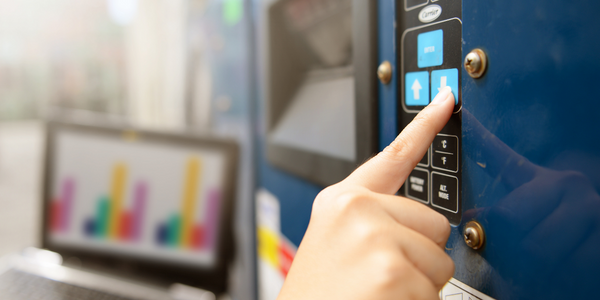
Case Study
Remote Temperature Monitoring of Perishable Goods Saves Money
RMONI was facing temperature monitoring challenges in a cold chain business. A cold chain must be established and maintained to ensure goods have been properly refrigerated during every step of the process, making temperature monitoring a critical business function. Manual registration practice can be very costly, labor intensive and prone to mistakes.
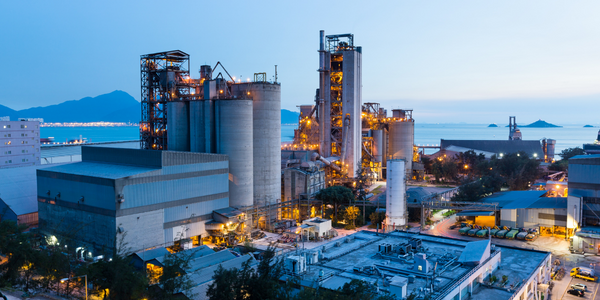
Case Study
Honeywell - Tata Chemicals Improves Data Accessibility with OneWireless
Tata was facing data accessibility challenges in the cement plant control room tapping signals from remote process control areas and other distant locations, including the gas scrubber. Tata needed a wireless solution to extend its control network securely to remote locations that would also provide seamless communication with existing control applications.

Case Study
Advanced Elastomer Systems Upgrades Production
In order to maintain its share of the international market for thermoplastic elastomers AES recently expanded its Florida plant by adding a new production line. While the existing lines were operating satisfactorily using a PROVOX distributed control system with traditional analog I/O, AES wanted advanced technology on the new line for greater economy, efficiency, and reliability. AES officials were anxious to get this line into production to meet incoming orders, but two hurricanes slowed construction.