Technology Category
- Infrastructure as a Service (IaaS) - Cloud Middleware & Microservices
- Platform as a Service (PaaS) - Application Development Platforms
Applicable Industries
- Specialty Vehicles
- Transportation
Use Cases
- Leasing Finance Automation
- Personnel Tracking & Monitoring
Services
- System Integration
About The Customer
Bowman Trailer Leasing is a rental company that provides road trailers and containers for land, sea, and onsite storage. Founded in 1972, the company has grown to become the leading trailer rental company on the East Coast of the United States, with over 175 employees and 32 locations across 14 states. The company caters to Fortune 500 companies such as Wal-Mart, Pepsi, and Coca-Cola. The majority of its employees work remotely, with the company's headquarters located in Maryland.
The Challenge
Bowman Trailer Leasing, a leading trailer rental company on the East Coast of the United States, was facing significant challenges with its outdated Avaya PBX phone system. The company, with its headquarters in Maryland and 32 locations across the East Coast, had a majority of its employees working remotely. The old system was proving to be inefficient and problematic, with over 30 employees attempting to share 16 voicemail boxes and none of the employees having direct lines. Additionally, scheduling technicians to service the PBX system was not only difficult but also expensive. The company was in dire need of a new phone system that would not only be cost-effective but also efficient and easy to manage, especially considering the company's IT Manager was the only IT staff member.
The Solution
Bowman Trailer Leasing turned to RingCentral, a cloud-based phone system, to address its communication challenges. The company was able to eliminate individual PBX systems for each of its 32 locations, leading to significant cost savings. The company now uses RingCentral’s auto-receptionist feature for its central 800 number to transfer customers to the appropriate extensions, thereby reducing customer wait times. Prior to RingCentral, an expensive third-party dispatcher was used to answer these calls after normal business hours. The company was also able to eliminate all traditional fax lines, with staff in the accounting department particularly pleased about faxing via RingCentral as it allows them to keep copies for their records. The RingCentral mobile app has also simplified communication between employees and customers.
Operational Impact
Quantitative Benefit
Case Study missing?
Start adding your own!
Register with your work email and create a new case study profile for your business.
Related Case Studies.
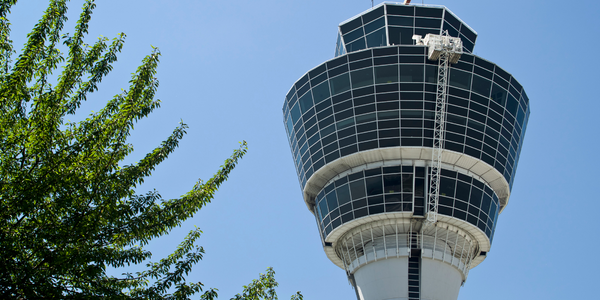
Case Study
Airport SCADA Systems Improve Service Levels
Modern airports are one of the busiest environments on Earth and rely on process automation equipment to ensure service operators achieve their KPIs. Increasingly airport SCADA systems are being used to control all aspects of the operation and associated facilities. This is because unplanned system downtime can cost dearly, both in terms of reduced revenues and the associated loss of customer satisfaction due to inevitable travel inconvenience and disruption.
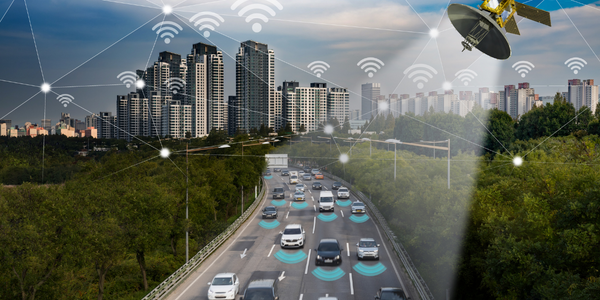
Case Study
Transformation for IoT Business Model in Connected Industrial Vehicles
CNH Industrial wanted to put IoT-enabled viechles onto the market. Whether monitoring a single machine or integrating an entire fleet, operators are able to track the status, speed, and movement of machines and their performance and also receive alerts on issues that may require service by a qualified technician to improve uptime and overall effectiveness of the vehicle.
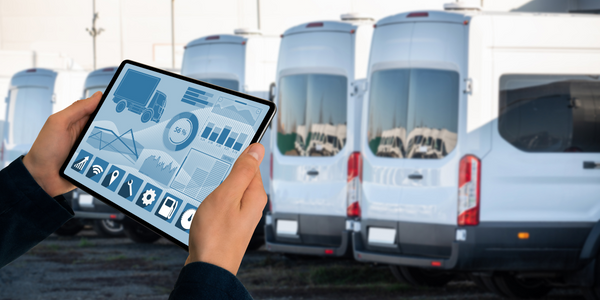
Case Study
IoT-based Fleet Intelligence Innovation
Speed to market is precious for DRVR, a rapidly growing start-up company. With a business model dependent on reliable mobile data, managers were spending their lives trying to negotiate data roaming deals with mobile network operators in different countries. And, even then, service quality was a constant concern.
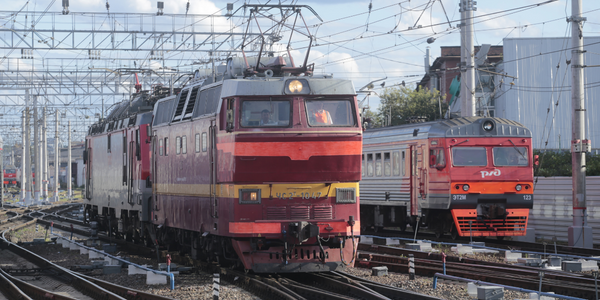
Case Study
Digitize Railway with Deutsche Bahn
To reduce maintenance costs and delay-causing failures for Deutsche Bahn. They need manual measurements by a position measurement system based on custom-made MEMS sensor clusters, which allow autonomous and continuous monitoring with wireless data transmission and long battery. They were looking for data pre-processing solution in the sensor and machine learning algorithms in the cloud so as to detect critical wear.
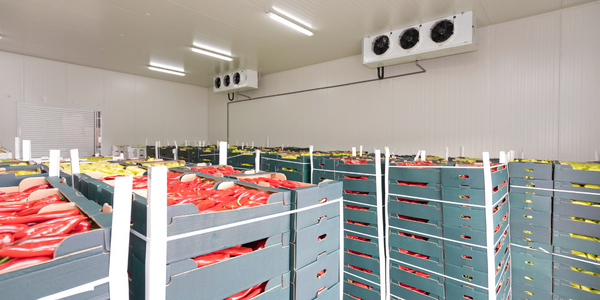
Case Study
Cold Chain Transportation and Refrigerated Fleet Management System
1) Create a digital connected transportation solution to retrofit cold chain trailers with real-time tracking and controls. 2) Prevent multi-million dollar losses due to theft or spoilage. 3) Deliver a digital chain-of-custody solution for door to door load monitoring and security. 4) Provide a trusted multi-fleet solution in a single application with granular data and access controls.