Technology Category
- Analytics & Modeling - Process Analytics
- Functional Applications - Enterprise Resource Planning Systems (ERP)
Applicable Industries
- Mining
- Oil & Gas
Applicable Functions
- Procurement
- Product Research & Development
Use Cases
- Process Control & Optimization
Services
- System Integration
About The Customer
BP is a global enterprise operating in the oil and gas industry. With hundreds of diverse processes spanning countless business units and domains, the company was seeking to standardize its operations and discover procurement inefficiencies. As part of a broader digital transformation plan, BP built out its Center of Excellence (CoE) and leveraged Celonis, a process mining tool, to visualize and streamline its processes. The company also partnered with Celonis for co-innovation projects, implementing features like Action Engine and Task Mining to automate tasks and improve efficiency.
The Challenge
BP, a global enterprise in the oil and gas industry, was faced with the challenge of standardizing hundreds of diverse processes across numerous business units and domains. The company had a clear vision of what it wanted its processes to look like, a state it referred to as its 'happy path', but identifying where existing processes were deviating from this path was proving difficult. The company was also looking to discover procurement inefficiencies as part of a broader digital transformation plan. The challenge was to visualize all the differences between processes that had been lifted and shifted into GBS, understand how to streamline them, and bring them in line with the happy path.
The Solution
BP built out its Center of Excellence (CoE) and leveraged Celonis, a process mining tool, to visualize and streamline its processes. The CoE team used Celonis to visualize the potential impact of proposed process changes early in the transformation process. This helped to secure the right senior sponsorship and ensure that the right resources were made available for every project. BP also partnered with Celonis for co-innovation projects, implementing features like Action Engine and Task Mining. Action Engine was used for smart receipting, transforming a manual chase into an automated process. Task Mining was used to break down specific time-consuming tasks like invoice processing, filling in all the manual gaps and pushing a big funnel of innovation and automation into the team.
Operational Impact
Quantitative Benefit
Case Study missing?
Start adding your own!
Register with your work email and create a new case study profile for your business.
Related Case Studies.
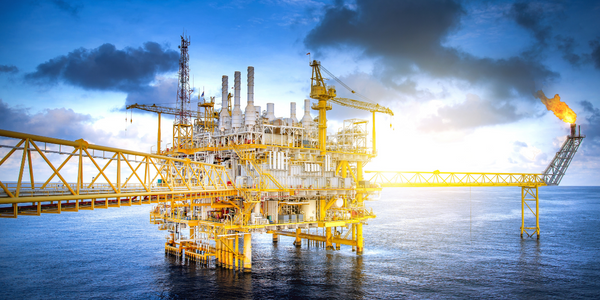
Case Study
Taking Oil and Gas Exploration to the Next Level
DownUnder GeoSolutions (DUG) wanted to increase computing performance by 5 to 10 times to improve seismic processing. The solution must build on current architecture software investments without sacrificing existing software and scale computing without scaling IT infrastructure costs.
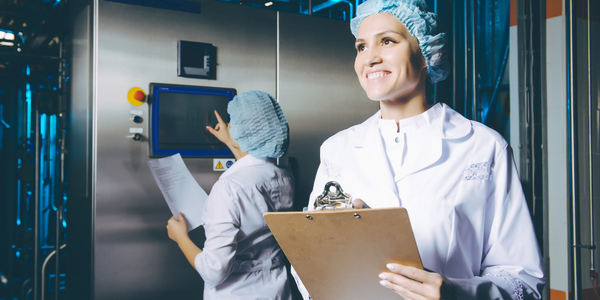
Case Study
Remote Wellhead Monitoring
Each wellhead was equipped with various sensors and meters that needed to be monitored and controlled from a central HMI, often miles away from the assets in the field. Redundant solar and wind generators were installed at each wellhead to support the electrical needs of the pumpstations, temperature meters, cameras, and cellular modules. In addition to asset management and remote control capabilities, data logging for remote surveillance and alarm notifications was a key demand from the customer. Terra Ferma’s solution needed to be power efficient, reliable, and capable of supporting high-bandwidth data-feeds. They needed a multi-link cellular connection to a central server that sustained reliable and redundant monitoring and control of flow meters, temperature sensors, power supply, and event-logging; including video and image files. This open-standard network needed to interface with the existing SCADA and proprietary network management software.
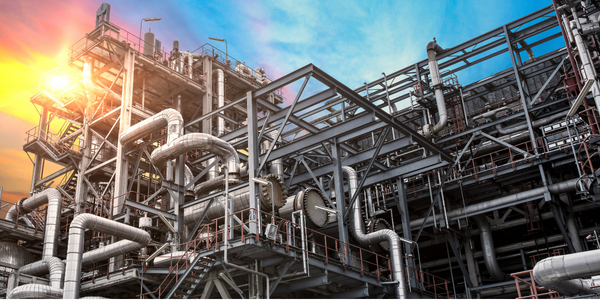
Case Study
Refinery Saves Over $700,000 with Smart Wireless
One of the largest petroleum refineries in the world is equipped to refine various types of crude oil and manufacture various grades of fuel from motor gasoline to Aviation Turbine Fuel. Due to wear and tear, eight hydrogen valves in each refinery were leaking, and each cost $1800 per ton of hydrogen vented. The plant also had leakage on nearly 30 flare control hydrocarbon valves. The refinery wanted a continuous, online monitoring system that could catch leaks early, minimize hydrogen and hydrocarbon production losses, and improve safety for maintenance.