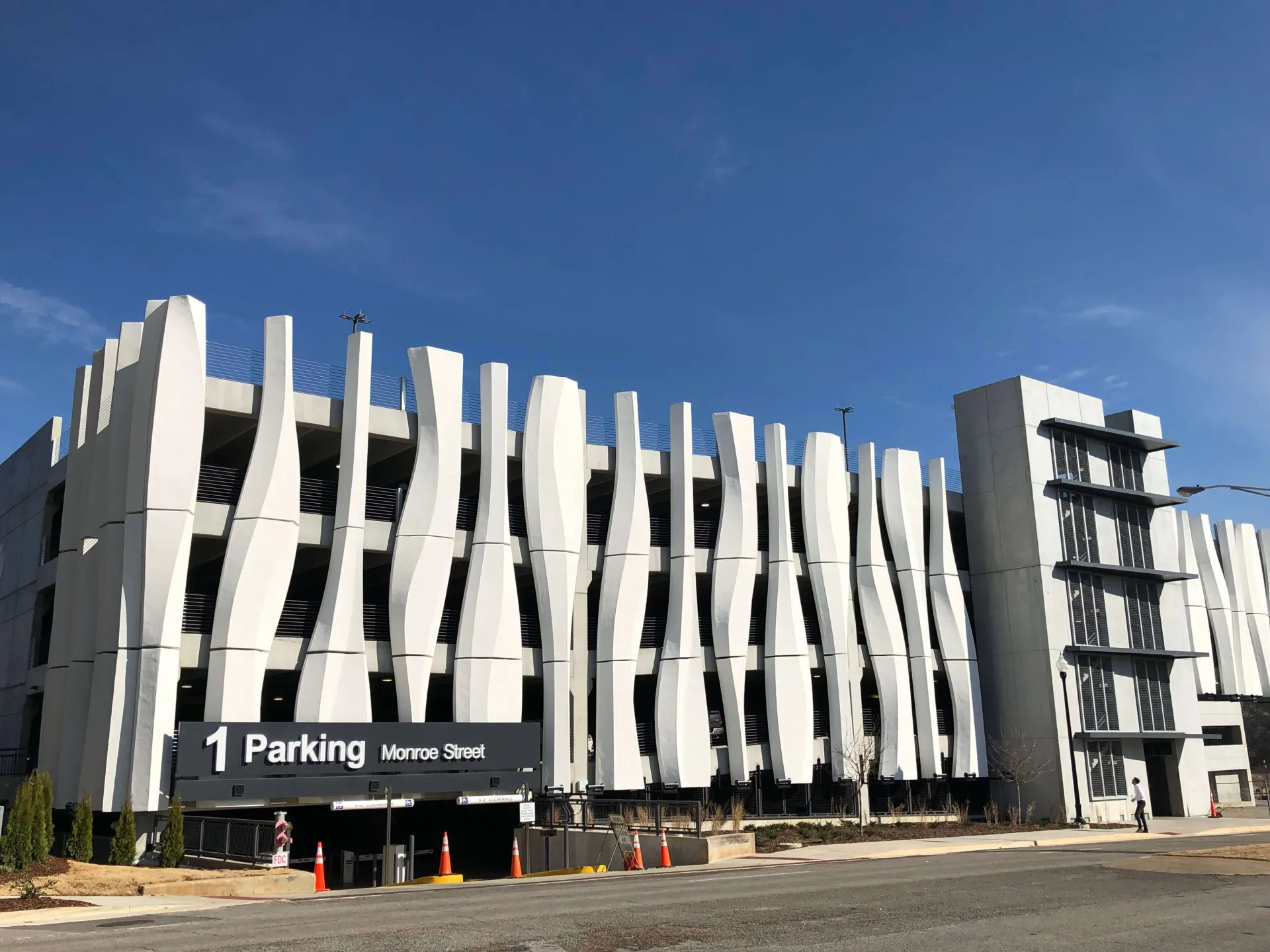
Technology Category
- Networks & Connectivity - Cellular
- Platform as a Service (PaaS) - Application Development Platforms
Applicable Industries
- Chemicals
- Telecommunications
Use Cases
- Additive Manufacturing
- Rapid Prototyping
Services
- Cloud Planning, Design & Implementation Services
- Training
The Customer
Branch Technology
About The Customer
Branch Technology is a Tennessee-based company that designs and manufactures commercial facade systems, including rainscreens and mega panel systems that offer articulated surfaces. The company is inspired by nature’s efficient cellular structures and has developed a unique construction-scale, freeform 3D-printing technique and direct digital manufacturing approach called cellular fabrication (C-Fab®). This approach enables architects, designers, and innovators to imagine, compose, and construct complex design structures. Branch Technology is committed to pushing the boundaries of design and manufacturing, and is always in search of innovative solutions that can enhance their processes and outcomes.
The Challenge
Branch Technology, a Tennessee-based company that designs and manufactures commercial facade systems, was in need of a software solution that could process complex geometries to produce a multitude of components for various digital fabrication methods. The company was inspired by nature's efficient cellular structures and had developed a construction-scale, freeform 3D-printing technique and direct digital manufacturing approach called cellular fabrication (C-Fab®). However, they were facing challenges in implementing a digital process that could eliminate digital fabrication bottlenecks, be easily updated, and yield high fidelity parts. The company was in search of a solution that could help them imagine, compose, and construct complex design structures with ease and precision.
The Solution
Branch Technology turned to Dassault Systèmes’ 3DEXPERIENCE® Cloud platform to address their challenges. They created a digital model of an intelligent template that included fabrication instructions, quality control metrics, cut files, and digital production elements. This template was used in a project in Alabama, where a model consisting of 102 panels, each with around 70 custom elements, was generated within the platform during the digital production phase. The template, created in CATIA, housed geometric configurations and components as logic. This solution provided a comprehensive and efficient approach to managing complex geometries and digital fabrication processes.
Operational Impact
Quantitative Benefit
Case Study missing?
Start adding your own!
Register with your work email and create a new case study profile for your business.
Related Case Studies.
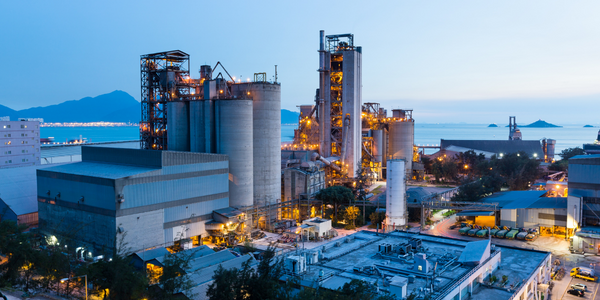
Case Study
Honeywell - Tata Chemicals Improves Data Accessibility with OneWireless
Tata was facing data accessibility challenges in the cement plant control room tapping signals from remote process control areas and other distant locations, including the gas scrubber. Tata needed a wireless solution to extend its control network securely to remote locations that would also provide seamless communication with existing control applications.

Case Study
Advanced Elastomer Systems Upgrades Production
In order to maintain its share of the international market for thermoplastic elastomers AES recently expanded its Florida plant by adding a new production line. While the existing lines were operating satisfactorily using a PROVOX distributed control system with traditional analog I/O, AES wanted advanced technology on the new line for greater economy, efficiency, and reliability. AES officials were anxious to get this line into production to meet incoming orders, but two hurricanes slowed construction.
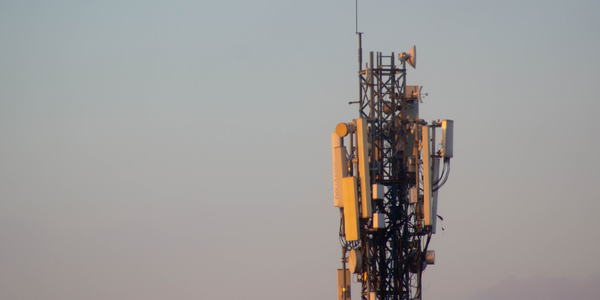
Case Study
Vodafone Hosted On AWS
Vodafone found that traffic for the applications peak during the four-month period when the international cricket season is at its height in Australia. During the 2011/2012 cricket season, 700,000 consumers downloaded the Cricket Live Australia application. Vodafone needed to be able to meet customer demand, but didn’t want to invest in additional resources that would be underutilized during cricket’s off-season.
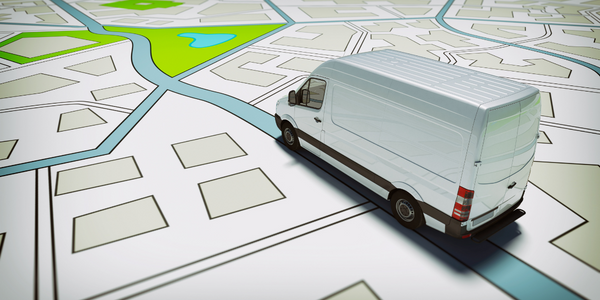
Case Study
Wireless GPS Tracking & Security Monitoring
Enhancing the security of hazardous freight and ensuring compliance with Homeland Security’s Transportation Security Administration mandate that all trains carrying chemicals capable of creating a toxic inhalation condition are equipped with on-board safety monitoring systems.