Customer Company Size
Large Corporate
Region
- America
Country
- United States
Product
- Documoto software platform
Tech Stack
- Cloud-based relational database
Implementation Scale
- Enterprise-wide Deployment
Impact Metrics
- Productivity Improvements
- Customer Satisfaction
Technology Category
- Platform as a Service (PaaS) - Data Management Platforms
Applicable Industries
- Consumer Goods
Applicable Functions
- Product Research & Development
- Quality Assurance
Use Cases
- Supply Chain Visibility
- Inventory Management
Services
- Cloud Planning, Design & Implementation Services
About The Customer
Viking Range, LLC has been making high-end residential ranges and appliances in Greenwood, Mississippi since the late 1980s. A pioneer in bringing commercial-quality technology and design to the residential market, Viking has become one of America’s iconic luxury brands. In 2012, Viking Range was acquired by The Middleby Corporation. Middleby is an industry leader in commercial and residential kitchen products with a portfolio of over 70 quality brands. Viking has continued to develop and introduce new products and innovations since the acquisition, maintaining its reputation as an extremely customer-focused organization.
The Challenge
Viking Range, LLC, a pioneer in bringing commercial-quality technology and design to the residential market, needed an online solution to provide comprehensive product information in one location for both service people and consumers. The documentation includes use and care instructions, installation guides, service manuals and bulletins, and parts books. Viking was also motivated to increase efficiencies in their publishing department. Their previous system relied on an outside vendor to update the content via static PDFs and spreadsheet files. The process of updating a parts book took up to two weeks before it was available online because Viking had to send the change to the external service provider and wait for them to get the content updated on Viking’s online system.
The Solution
After conducting market research and evaluating a number of competing products, Viking selected the Documoto software platform as the best option for fulfilling its desired criteria. Documoto’s cloud-based relational database system would allow the greatest flexibility in associating media, parts, and appliance models. And it would enable technical publishers to make changes to parts lists and upload new documents instantly, saving time for both the publishing department and service technicians. With a fairly extensive library of legacy documents and data, Viking enlisted Documoto’s Professional Services team to help with conversion and migration of existing content. Documoto was successfully deployed on schedule, approximately 90 days after starting implementation. Technical writers and illustrators immediately began using the application to speed up critical processes.
Operational Impact
Quantitative Benefit
Case Study missing?
Start adding your own!
Register with your work email and create a new case study profile for your business.
Related Case Studies.
.png)
Case Study
Improving Vending Machine Profitability with the Internet of Things (IoT)
The vending industry is undergoing a sea change, taking advantage of new technologies to go beyond just delivering snacks to creating a new retail location. Intelligent vending machines can be found in many public locations as well as company facilities, selling different types of goods and services, including even computer accessories, gold bars, tickets, and office supplies. With increasing sophistication, they may also provide time- and location-based data pertaining to sales, inventory, and customer preferences. But at the end of the day, vending machine operators know greater profitability is driven by higher sales and lower operating costs.
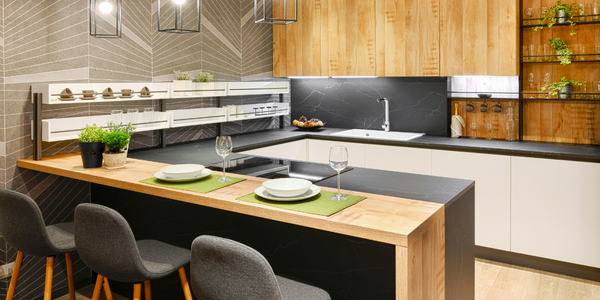
Case Study
Series Production with Lot-size-1 Flexibility
Nobilia manufactures customized fitted kitchens with a lot size of 1. They require maximum transparency of tracking design data and individual processing steps so that they can locate a particular piece of kitchen furniture in the sequence of processes.
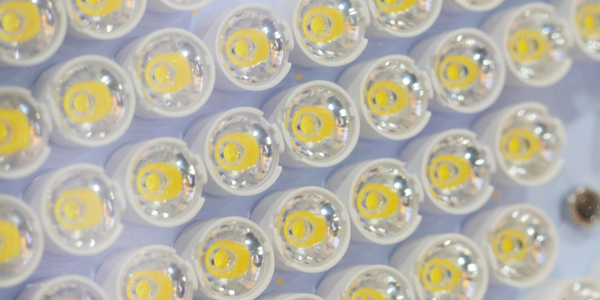
Case Study
American Eagle Achieves LEED with GE LED Lighting Fixtures
American Eagle Outfitters (AEO) was in the process of building a new distribution center. The AEO facility management team decided to look at alternate options for lighting layout that could provide energy and maintenance savings. AEO would need a full-time maintenance employee just to replace burned-out fluorescent tubes.
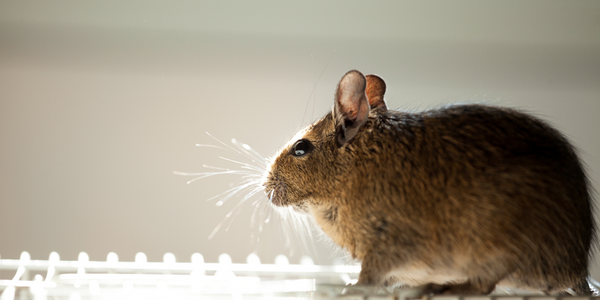
Case Study
Revolutionizing Rodent Control
From pet- and child-safe traps, to touch-free and live-catch rodent control solutions, Victor continues to stay committed to producing superior products that meet the varying needs of today’s pest control professionals. And, with a long standing history supporting customers in the food processing, service, and retail settings, Victor knew that strict regulations were costing organizations thousands of dollars in excess overhead trying to manage their rodent-control solutions. Trap inspections in these environments are often difficult and time consuming, requiring personnel to manually check a trap’s status multiple times per day, amounting to over six hours of manual labor. Victor is looking for an innovative way to increase operational efficiencies with the use of technology.