Technology Category
- Functional Applications - Fleet Management Systems (FMS)
- Robots - Autonomous Guided Vehicles (AGV)
Applicable Industries
- Automotive
- Transportation
Use Cases
- Public Transportation Management
- Vehicle Performance Monitoring
About The Customer
The customers of the Pickup service are residents of the Austin metro region, including rural, suburban, and urban areas. These individuals previously had limited access to the city’s fixed route transit system, making commuting a challenge, especially for those with limited mobility. The Pickup service was designed to cater to these individuals, offering a convenient, accessible, and cost-effective solution for their commuting needs. The service is particularly beneficial for those who rely on public transit for their daily commute, as well as those who require wheelchair-accessible vehicles.
The Challenge
The Austin metro region, encompassing rural, suburban, and urban areas, was grappling with limited access to the city’s fixed route transit system. This posed a significant challenge for residents, particularly those with limited mobility. The existing transit options were inadequate and inconvenient, making daily commuting a struggle for many. A previous dial-a-ride service had been implemented but it was not cost-effective and failed to meet the growing demand. In 2017, a pilot project between Via and CapMetro quadrupled ridership and halved the cost per passenger, prompting CapMetro to consider a more extensive solution. The goal was to re-launch the 'Pickup' service in five zones covering a combined 18 square miles within the Austin region, with plans to expand to additional zones.
The Solution
In June 2019, Via and CapMetro re-launched the Pickup service, covering five large service zones. The service was designed to be fully accessible for riders with all types of needs. Rides could be booked through the Pickup app or by phone, offering flexibility and convenience to users. The service was priced the same as MetroBus and MetroRapid, and accepted a variety of payment methods, including credit cards, cash, and CapMetro transit passes. The vehicle fleet was fully wheelchair accessible, ensuring inclusivity for all riders. Despite a decline in ridership during the COVID-19 pandemic, Via and CapMetro continued to invest in Pickup’s long-term success, launching new service areas in Leander, Lago Vista, Pflugerville, and Dessau.
Operational Impact
Quantitative Benefit
Case Study missing?
Start adding your own!
Register with your work email and create a new case study profile for your business.
Related Case Studies.
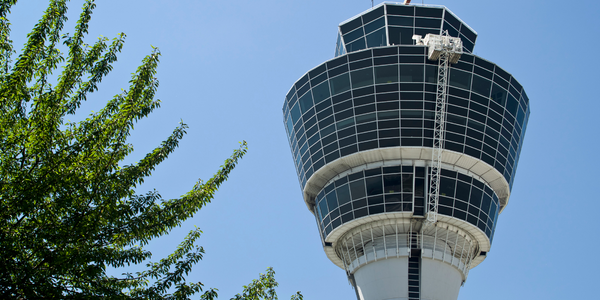
Case Study
Airport SCADA Systems Improve Service Levels
Modern airports are one of the busiest environments on Earth and rely on process automation equipment to ensure service operators achieve their KPIs. Increasingly airport SCADA systems are being used to control all aspects of the operation and associated facilities. This is because unplanned system downtime can cost dearly, both in terms of reduced revenues and the associated loss of customer satisfaction due to inevitable travel inconvenience and disruption.
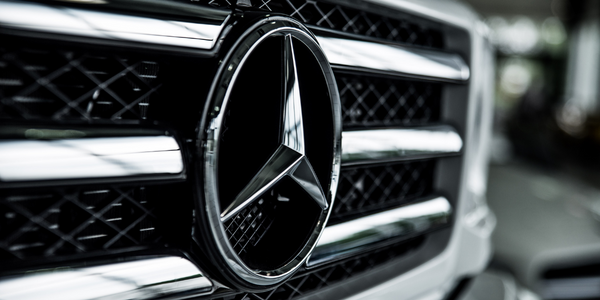
Case Study
Integral Plant Maintenance
Mercedes-Benz and his partner GAZ chose Siemens to be its maintenance partner at a new engine plant in Yaroslavl, Russia. The new plant offers a capacity to manufacture diesel engines for the Russian market, for locally produced Sprinter Classic. In addition to engines for the local market, the Yaroslavl plant will also produce spare parts. Mercedes-Benz Russia and his partner needed a service partner in order to ensure the operation of these lines in a maintenance partnership arrangement. The challenges included coordinating the entire maintenance management operation, in particular inspections, corrective and predictive maintenance activities, and the optimizing spare parts management. Siemens developed a customized maintenance solution that includes all electronic and mechanical maintenance activities (Integral Plant Maintenance).
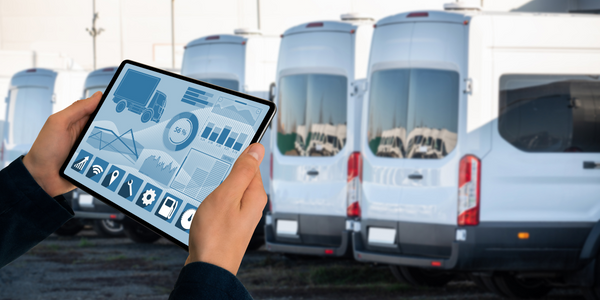
Case Study
IoT-based Fleet Intelligence Innovation
Speed to market is precious for DRVR, a rapidly growing start-up company. With a business model dependent on reliable mobile data, managers were spending their lives trying to negotiate data roaming deals with mobile network operators in different countries. And, even then, service quality was a constant concern.
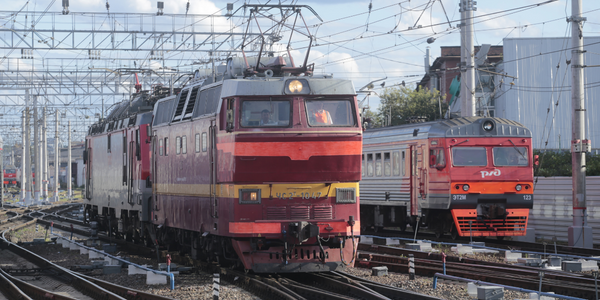
Case Study
Digitize Railway with Deutsche Bahn
To reduce maintenance costs and delay-causing failures for Deutsche Bahn. They need manual measurements by a position measurement system based on custom-made MEMS sensor clusters, which allow autonomous and continuous monitoring with wireless data transmission and long battery. They were looking for data pre-processing solution in the sensor and machine learning algorithms in the cloud so as to detect critical wear.
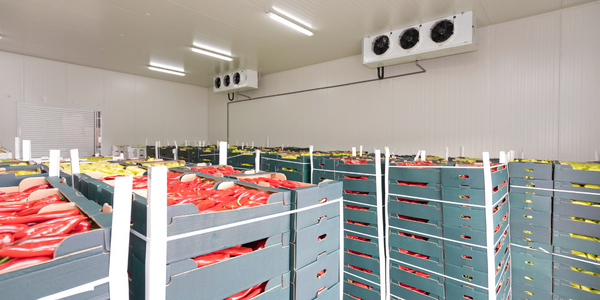
Case Study
Cold Chain Transportation and Refrigerated Fleet Management System
1) Create a digital connected transportation solution to retrofit cold chain trailers with real-time tracking and controls. 2) Prevent multi-million dollar losses due to theft or spoilage. 3) Deliver a digital chain-of-custody solution for door to door load monitoring and security. 4) Provide a trusted multi-fleet solution in a single application with granular data and access controls.