Technology Category
- Application Infrastructure & Middleware - Middleware, SDKs & Libraries
- Robots - Autonomous Guided Vehicles (AGV)
Applicable Industries
- Automotive
- Finance & Insurance
Applicable Functions
- Maintenance
- Procurement
Use Cases
- Usage-Based Insurance
- Vehicle Performance Monitoring
Services
- System Integration
About The Customer
ChevyPlan is the leading brand of payment schemes for new Chevrolet vehicles, serving Ecuador for 11 years and the Andean Region for over twenty years. The company encourages and develops a culture of planification in the automotive industry for the supply of new Chevrolet vehicles, offering high-quality products and services with highly dedicated, motivated, and skilled staff. ChevyPlan has managed the purchase of over sixteen thousand vehicles to date, benefiting its customers by generating savings through careful planning.
The Challenge
ChevyPlan, a leading brand of payment schemes for new Chevrolet vehicles in Ecuador and the Andean Region, faced significant operational challenges due to its growth. The company was dealing with a high volume of operational work across various departments to monitor and manage the provision of vehicles for each customer. The manual generation and review of documentation were labor-intensive and time-consuming, involving approvals and the collection of signatures. The process was also prone to errors, leading to reprocessing of work. ChevyPlan needed a software solution that would give them control of all the elements involved in the vehicle provision process, including document generation tools, a notification system, and connectivity with internal systems.
The Solution
ChevyPlan chose AuraQuantic iBPMS to manage their internal processes and integrate the information from their systems, thereby controlling and improving the participation from suppliers and other external companies. The process implementation with AuraQuantic began with a basic process which made it possible to send billing orders and generate documents. Thanks to AuraPortal’s ability to manage continuous improvement, it continued to optimize and today, it has transformed into a process which generates all documentation online and involves several company areas and external companies including insurance firms, notaries, and dealers. The success of the first project led ChevyPlan towards business excellence through a high level of process management maturity. They have used AuraQuantic to automate other processes including sales, maintenance, cession of rights, etc., making their processes more agile and eliminating manual activities.
Operational Impact
Quantitative Benefit
Case Study missing?
Start adding your own!
Register with your work email and create a new case study profile for your business.
Related Case Studies.
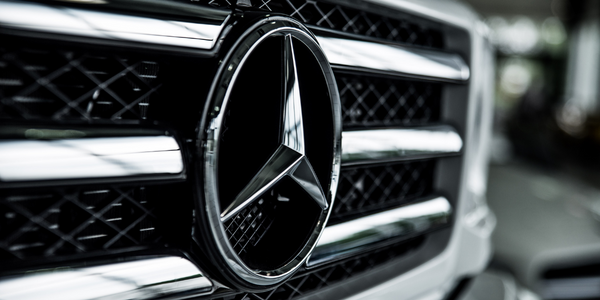
Case Study
Integral Plant Maintenance
Mercedes-Benz and his partner GAZ chose Siemens to be its maintenance partner at a new engine plant in Yaroslavl, Russia. The new plant offers a capacity to manufacture diesel engines for the Russian market, for locally produced Sprinter Classic. In addition to engines for the local market, the Yaroslavl plant will also produce spare parts. Mercedes-Benz Russia and his partner needed a service partner in order to ensure the operation of these lines in a maintenance partnership arrangement. The challenges included coordinating the entire maintenance management operation, in particular inspections, corrective and predictive maintenance activities, and the optimizing spare parts management. Siemens developed a customized maintenance solution that includes all electronic and mechanical maintenance activities (Integral Plant Maintenance).
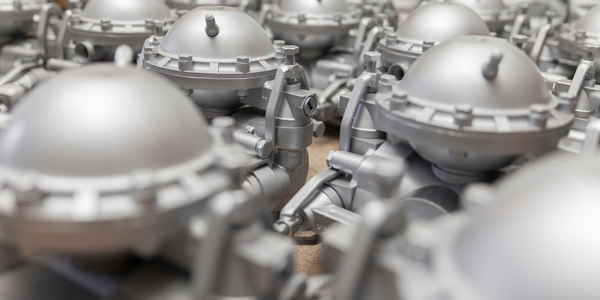
Case Study
Monitoring of Pressure Pumps in Automotive Industry
A large German/American producer of auto parts uses high-pressure pumps to deburr machined parts as a part of its production and quality check process. They decided to monitor these pumps to make sure they work properly and that they can see any indications leading to a potential failure before it affects their process.