Circulor achieves first-ever-mine-to-manufacturer traceability of a conflict mineral with Hyperledger Fabric
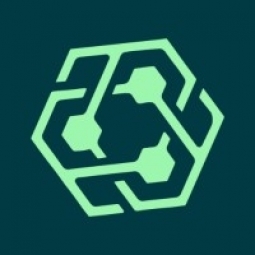
Customer Company Size
Large Corporate
Region
- Africa
- Europe
Country
- Macedonia
- United Kingdom
Product
- Hyperledger Fabric
- Circulor Blockchain System
- URU Facial Recognition System
Tech Stack
- Blockchain
- Facial Recognition
- QR Codes
- Smart Contracts
- Cloud Computing (Oracle Cloud, Amazon Web Services)
Implementation Scale
- Enterprise-wide Deployment
Impact Metrics
- Cost Savings
- Brand Awareness
- Customer Satisfaction
Technology Category
- Application Infrastructure & Middleware - Blockchain
- Application Infrastructure & Middleware - Data Exchange & Integration
Applicable Industries
- Mining
- Electronics
Applicable Functions
- Logistics & Transportation
- Procurement
Use Cases
- Track & Trace of Assets
- Supply Chain Visibility
- Regulatory Compliance Monitoring
Services
- System Integration
- Cloud Planning, Design & Implementation Services
About The Customer
The customer in this case study is the African country of Rwanda, the world's biggest supplier of tantalum. Tantalum is a rare mineral used to make capacitors found in devices like smartphones and laptops. A small region of Africa produces 60% of the world's supply, with Rwanda as the main exporter. However, tantalum was sometimes smuggled in from conflict-ridden Congo, where it was mined by children or workers enslaved by warlords. This led to the OECD, U.S., and EU naming tantalum a 'conflict mineral' and passing regulations to improve its traceability. Despite these rules, no one had a foolproof way to prove where tantalum actually came from.
The Challenge
Rwanda, the world's largest supplier of tantalum, a rare mineral used in devices like smartphones and laptops, faced a challenge in proving that every bag of tantalum ore was mined, transported, and processed under OECD-approved conditions, without any child or slave labor. The existing tracing methods involved tagging materials and filling in paper forms, which met the OECD rules but didn't provide actual traceability. It also generated a costly mountain of paper with room for errors or fraud. The challenge was to create a system that ensures tantalum is mined, transported, and processed under approved conditions with an unbroken chain of custody.
The Solution
UK-based Circulor created a system that ensures tantalum is mined, transported, and processed under approved conditions with an unbroken chain of custody. Powered by a permissioned blockchain built on Hyperledger Fabric, the system uses facial recognition and QR codes to deliver a world first: mine-to-manufacturer traceability of this vital resource. After mapping every step of the supply chain for tantalum from mine to manufacturer, Circulor introduced new online procedures that generate reliable data at each step of the global supply chain. The system databases are hosted in the cloud through a combination of Oracle Cloud and Amazon Web Services.
Operational Impact
Quantitative Benefit
Case Study missing?
Start adding your own!
Register with your work email and create a new case study profile for your business.
Related Case Studies.
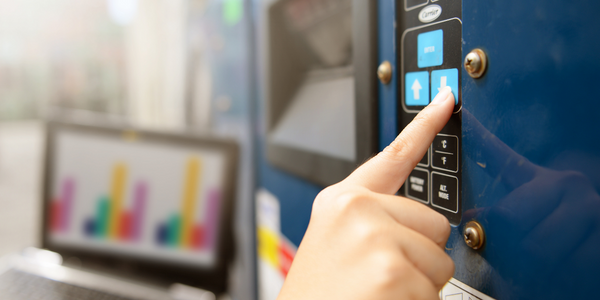
Case Study
Remote Temperature Monitoring of Perishable Goods Saves Money
RMONI was facing temperature monitoring challenges in a cold chain business. A cold chain must be established and maintained to ensure goods have been properly refrigerated during every step of the process, making temperature monitoring a critical business function. Manual registration practice can be very costly, labor intensive and prone to mistakes.
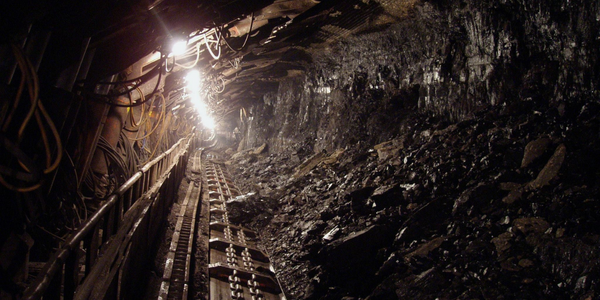
Case Study
Underground Mining Safety
The goal was to produce a safety system to monitor and support underground mining operations; existing systems were either too simple (i.e. phone line) or overly complex and expensive, inhibiting deployment, and providing little-to-no support in event of an accident. Given the dangerous nature of the mining work environment and the strict regulations placed on the industry, the solution would have to comply with Mine Safety and Health Administration (MSHA) regulations. Yet the product needed to allow for simple deployment to truly be a groundbreaking solution - increasing miner safety and changing daily operations for the better.
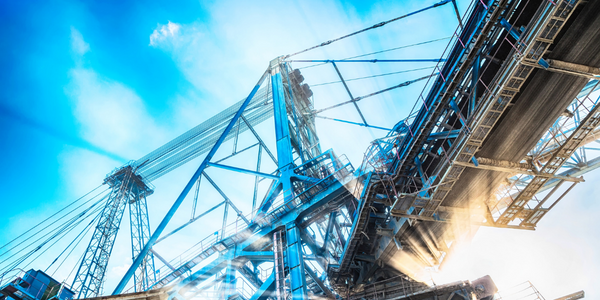
Case Study
Mining Firm Quadruples Production, with Internet of Everything
Dundee Precious Metal’s flagship mine, in Chelopech, Bulgaria, produces a gold, copper, and silver concentrate set a goal to increase production by 30%. Dundee wanted to increase production quality and output without increasing headcount and resources, improve miner safety, and minimize cost.
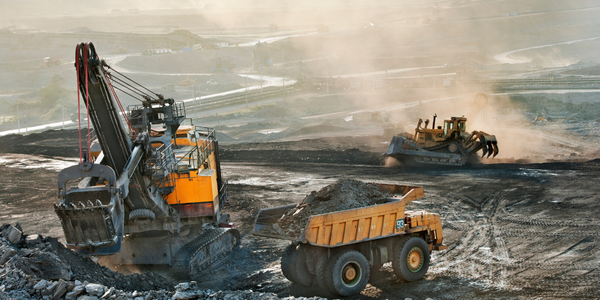
Case Study
Fastenal Builds the Future of Manufacturing with MachineMetrics
Fastenal's objective was to better understand their machine downtime, utilization, quality issues, and to embrace cutting-edge manufacturing technology/process improvement capabilities to bring their team to the next level. However, there was a lack of real-time data, visualization, and actionable insights made this transition impossible.