Customer Company Size
Mid-size Company
Region
- America
Country
- Canada
Product
- FlowForma Process Automation
Tech Stack
- Microsoft Excel
- SharePoint
- Power BI
Implementation Scale
- Enterprise-wide Deployment
Impact Metrics
- Productivity Improvements
- Cost Savings
Technology Category
- Application Infrastructure & Middleware - Data Exchange & Integration
Applicable Industries
- Oil & Gas
Applicable Functions
- Human Resources
Use Cases
- Personnel Tracking & Monitoring
Services
- System Integration
- Software Design & Engineering Services
About The Customer
Morgan Construction and Environmental Ltd. is an oilfield construction company based out of Edmonton, Alberta, with branches across the province. The company prides itself on delivering excellence and upholding the utmost workplace safety. The core of their business lies in their employees and contractors. Due to the nature of their business, the company has a high volume of these individuals being onboarded to work on contracts across the various oilfield sites they serve. The company has over 200 employees.
The Challenge
Morgan Construction, an oilfield construction company, was facing challenges with their employee onboarding process. The company relied on a shared Microsoft Excel spreadsheet to manage and track the onboarding progress of employees. This method was time-consuming, susceptible to human error, and was no longer an efficient tool considering the volume of individuals that were being onboarded at a time. The spreadsheet could not show the team up-to-date reporting nor could it efficiently organize the 200+ employees tracked in the spreadsheet. The team needed a solution for providing timely and accurate reports to executives and client sites to ensure they were kept up-to-date on the status of when employees and contractors would be available for the next job.
The Solution
Morgan Construction used FlowForma Process Automation as a workflow solution that organized the onboarding process, reduced the likelihood of human errors, and allowed for automated, accurate progress reporting. Pontem Innovations worked closely with the Field Recruitment Supervisor and members of the team to develop a customized solution with the use of FlowForma Process Automation. By using FlowForma Process Automation as the basis for the digital workflow, Pontem Innovations could tailor the tool to meet the specific needs of the business requirements – particularly the automation of the process that allowed the HR team to no longer manually update documents, track progress status through one shared Excel, nor email documents back and forth.
Operational Impact
Quantitative Benefit
Case Study missing?
Start adding your own!
Register with your work email and create a new case study profile for your business.
Related Case Studies.
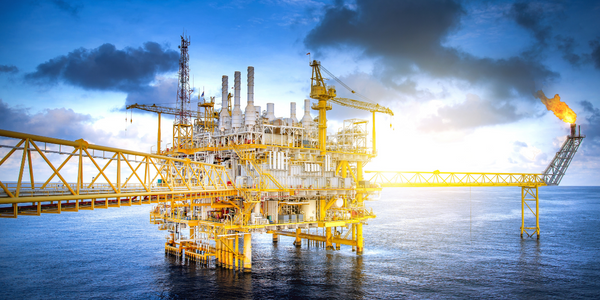
Case Study
Taking Oil and Gas Exploration to the Next Level
DownUnder GeoSolutions (DUG) wanted to increase computing performance by 5 to 10 times to improve seismic processing. The solution must build on current architecture software investments without sacrificing existing software and scale computing without scaling IT infrastructure costs.
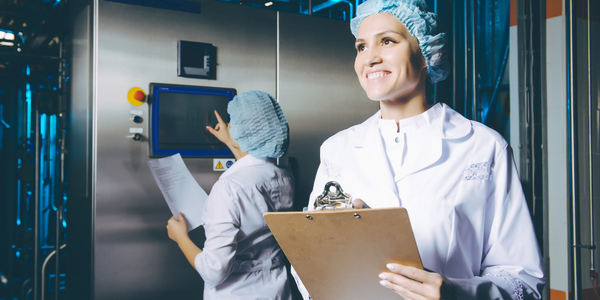
Case Study
Remote Wellhead Monitoring
Each wellhead was equipped with various sensors and meters that needed to be monitored and controlled from a central HMI, often miles away from the assets in the field. Redundant solar and wind generators were installed at each wellhead to support the electrical needs of the pumpstations, temperature meters, cameras, and cellular modules. In addition to asset management and remote control capabilities, data logging for remote surveillance and alarm notifications was a key demand from the customer. Terra Ferma’s solution needed to be power efficient, reliable, and capable of supporting high-bandwidth data-feeds. They needed a multi-link cellular connection to a central server that sustained reliable and redundant monitoring and control of flow meters, temperature sensors, power supply, and event-logging; including video and image files. This open-standard network needed to interface with the existing SCADA and proprietary network management software.
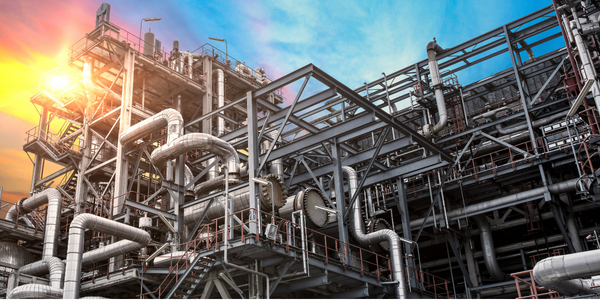
Case Study
Refinery Saves Over $700,000 with Smart Wireless
One of the largest petroleum refineries in the world is equipped to refine various types of crude oil and manufacture various grades of fuel from motor gasoline to Aviation Turbine Fuel. Due to wear and tear, eight hydrogen valves in each refinery were leaking, and each cost $1800 per ton of hydrogen vented. The plant also had leakage on nearly 30 flare control hydrocarbon valves. The refinery wanted a continuous, online monitoring system that could catch leaks early, minimize hydrogen and hydrocarbon production losses, and improve safety for maintenance.