Customer Company Size
Large Corporate
Region
- America
- Asia
- Europe
Country
- United States
- China
- India
Product
- EthicsPoint® Incident Management
- Whistleblower Hotline Intake
- Awareness Solutions
Tech Stack
- Reporting System
- Case Management System
Implementation Scale
- Enterprise-wide Deployment
Impact Metrics
- Employee Satisfaction
- Productivity Improvements
Technology Category
- Application Infrastructure & Middleware - Data Exchange & Integration
- Analytics & Modeling - Process Analytics
Applicable Industries
- Automotive
Applicable Functions
- Human Resources
- Business Operation
Use Cases
- Process Control & Optimization
- Regulatory Compliance Monitoring
Services
- System Integration
- Cloud Planning, Design & Implementation Services
About The Customer
Cummins, Inc. is a global power leader that designs, manufactures, distributes, and services engines and related technologies, including fuel systems, controls, air handling, filtration, emission solutions, and electrical power generation systems. The corporation is made up of complementary business units. Headquartered in Columbus, Indiana, Cummins employs approximately 46,000 people worldwide and serves customers in approximately 190 countries and territories through a network of more than 600 company-owned and independent distributor locations and approximately 6,500 dealer locations. The company is committed to acting responsibly to improve the lives of its stakeholders and communities. It believes in the power of its employees and works to ensure that they know that Cummins is deeply committed to providing an ethical work environment for them.
The Challenge
Cummins, a global power leader with approximately 46,000 employees worldwide, was facing the challenge of maintaining a consistent communication structure across its global operations. The company was outgrowing its old vendor and needed a system that could support its Code of Conduct policies on a global scale. The company launched a Six Sigma project to determine the necessary requirements for an ideal system. As an international company, Cummins needed a comprehensive reporting system to maintain a consistent workplace culture around the world.
The Solution
Cummins selected EthicsPoint case management to help them overcome their challenges. The company worked with NAVEX’s Implementation Services team to configure the system according to the global business needs of Cummins. Now, Cummins has a consistent communication process in every business unit and region. If a concern is reported, the case automatically goes to a Master Investigator who assigns it, monitors the process, and closes the case. Each Master Investigator can analyze regional data and report statistics using the system. The internal audit, legal, security, and human resources teams at Cummins are notified of any relevant cases, and often work together to decide which group leads the investigation. All departments collaborate and store their data in the system, so those who have been given access to the information have it available at their fingertips.
Operational Impact
Quantitative Benefit
Case Study missing?
Start adding your own!
Register with your work email and create a new case study profile for your business.
Related Case Studies.
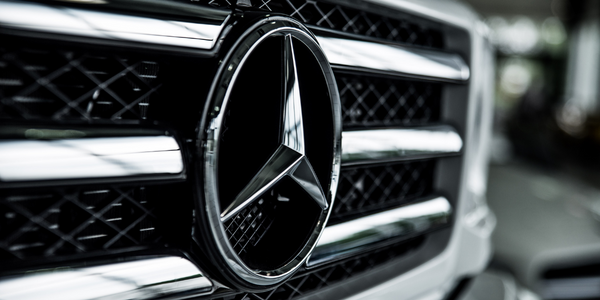
Case Study
Integral Plant Maintenance
Mercedes-Benz and his partner GAZ chose Siemens to be its maintenance partner at a new engine plant in Yaroslavl, Russia. The new plant offers a capacity to manufacture diesel engines for the Russian market, for locally produced Sprinter Classic. In addition to engines for the local market, the Yaroslavl plant will also produce spare parts. Mercedes-Benz Russia and his partner needed a service partner in order to ensure the operation of these lines in a maintenance partnership arrangement. The challenges included coordinating the entire maintenance management operation, in particular inspections, corrective and predictive maintenance activities, and the optimizing spare parts management. Siemens developed a customized maintenance solution that includes all electronic and mechanical maintenance activities (Integral Plant Maintenance).
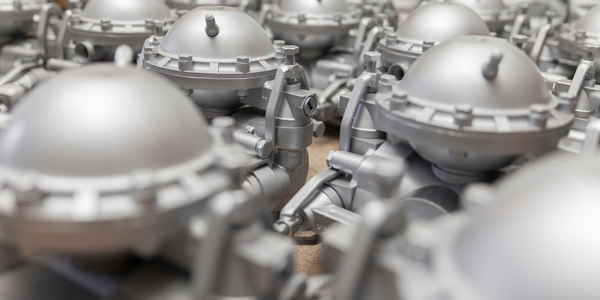
Case Study
Monitoring of Pressure Pumps in Automotive Industry
A large German/American producer of auto parts uses high-pressure pumps to deburr machined parts as a part of its production and quality check process. They decided to monitor these pumps to make sure they work properly and that they can see any indications leading to a potential failure before it affects their process.