Customer Case Study: Dunlop Systems & Components
Customer Company Size
SME
Region
- Europe
Country
- United Kingdom
Product
- Priority ERP
- ECAS (Electronically Controlled Air Suspension)
- Air Springs
Tech Stack
- ERP
- Business Intelligence
- Data Cleansing
Implementation Scale
- Enterprise-wide Deployment
Impact Metrics
- Productivity Improvements
- Customer Satisfaction
- Cost Savings
Technology Category
- Functional Applications - Enterprise Resource Planning Systems (ERP)
- Application Infrastructure & Middleware - Data Exchange & Integration
Applicable Industries
- Automotive
Applicable Functions
- Logistics & Transportation
Use Cases
- Inventory Management
Services
- System Integration
- Data Science Services
- Software Design & Engineering Services
About The Customer
Dunlop Systems & Components, headquartered in Coventry, UK, specializes in the design and manufacture of advanced electronic control systems and air suspension components for the automotive and ancillary industries. Established in 2007 after a management buyout of the Dunlop Coventry suspension division from Trelleborg AB, the company operates from a state-of-the-art facility. Dunlop's product range includes air springs, electronically controlled air suspension (ECAS), air suspension conversions, mobility systems, testing services, and electronic design. The company employs close to 100 people and has an annual turnover of approximately £10 million. They have sold over a quarter of a million ECAS systems worldwide and over 10 million air springs since production began in the 1950s.
The Challenge
The senior management team at Dunlop Systems & Components identified the need for a more robust and efficient ERP system to replace their outdated and costly legacy system. The legacy system had several issues, including data accuracy problems related to BOM's routings and core part data, and a poor MRP mechanism that resulted in operational inefficiency. Dunlop aimed to implement a comprehensive ERP package focusing on production, logistics, and project management. Their future plans included extensive use of shop floor data collection, PDA’s, barcoding, and live reporting of production.
The Solution
Dunlop Systems & Components partnered with Medatech UK to implement the Priority ERP system. Priority provided a standard system with modifications tailored to Dunlop's business processes. The implementation included extensive data cleansing before migrating to the new system, ensuring accurate results across various data analyzers. The new ERP system facilitated smooth and efficient workflows in the challenging environment of a manufacturing platform within a multi-company setup. The project management module was integrated into the system, enhancing transparency and collaboration across departments. The business intelligence module allowed for executive dashboards and drill-down capabilities, providing management with a comprehensive view of business processes and performance.
Operational Impact
Quantitative Benefit
Case Study missing?
Start adding your own!
Register with your work email and create a new case study profile for your business.
Related Case Studies.
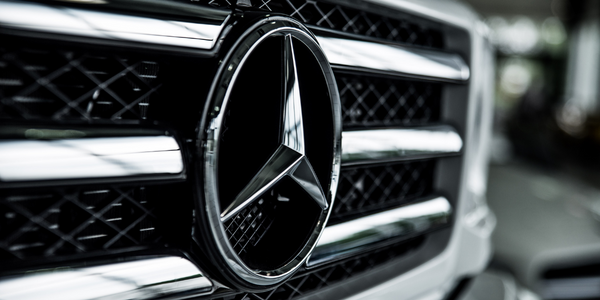
Case Study
Integral Plant Maintenance
Mercedes-Benz and his partner GAZ chose Siemens to be its maintenance partner at a new engine plant in Yaroslavl, Russia. The new plant offers a capacity to manufacture diesel engines for the Russian market, for locally produced Sprinter Classic. In addition to engines for the local market, the Yaroslavl plant will also produce spare parts. Mercedes-Benz Russia and his partner needed a service partner in order to ensure the operation of these lines in a maintenance partnership arrangement. The challenges included coordinating the entire maintenance management operation, in particular inspections, corrective and predictive maintenance activities, and the optimizing spare parts management. Siemens developed a customized maintenance solution that includes all electronic and mechanical maintenance activities (Integral Plant Maintenance).
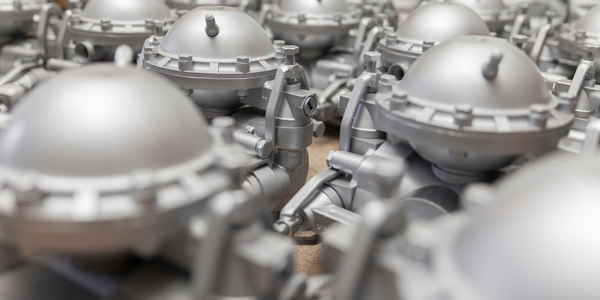
Case Study
Monitoring of Pressure Pumps in Automotive Industry
A large German/American producer of auto parts uses high-pressure pumps to deburr machined parts as a part of its production and quality check process. They decided to monitor these pumps to make sure they work properly and that they can see any indications leading to a potential failure before it affects their process.