Customer Company Size
Large Corporate
Region
- America
Country
- United States
- Canada
- Mexico
Product
- ICONICS GENESIS32™
- GraphWorX™32
- TrendWorX™32
- AlarmWorX™32
- ScriptWorX™32
Tech Stack
- Oracle®-based database
- POSMON®
- Local Area Network (LAN)
Implementation Scale
- Enterprise-wide Deployment
Impact Metrics
- Productivity Improvements
- Digital Expertise
Technology Category
- Platform as a Service (PaaS) - Connectivity Platforms
- Application Infrastructure & Middleware - Data Exchange & Integration
Applicable Industries
- Automotive
Applicable Functions
- Discrete Manufacturing
- Quality Assurance
Use Cases
- Machine Condition Monitoring
- Real-Time Location System (RTLS)
- Predictive Maintenance
Services
- System Integration
- Software Design & Engineering Services
About The Customer
Comau Pico is an innovative leader in industrial automation. As a member of the Comau Group, they are part of the largest full-service automotive supplier in the world. With over 50 years of experience in automated assembly tooling, Comau Pico offers an unparalleled scope of engineering and services to the North American market. Using the latest technology, they deliver complete turnkey systems and continually meet and exceed the design and manufacturing needs of their customers. Comau Pico is an Authorized OEM of ICONICS and uses GENESIS32™ software extensively on their systems.
The Challenge
Ford Motor Company contracted with Comau Pico to design and install multiple cold and hot test stands at the Dearborn Engine plant. The requirement was to perform 100 percent testing of every engine produced at this plant (4 & 6 cylinder engines) along with the logging and trending of results for both cold and hot testing. Cold testing does not use gasoline and the engine is basically driven by an external motor. All fluids are installed and the engine is run through its cycles. Hot testing involves adding gasoline and actually starting and running the engine through various test cycles. The test stands perform measurements on the heating and cooling of fluids as well as exhaust gases, spark timing and advancement through the RPM range. Testing is also done on the air combustion mixture of exhaust gases and fuel mixtures of the injection systems.
The Solution
Comau Pico has installed ICONICS GENESIS32™ HMI/SCADA software suite (including GraphWorX™32, TrendWorX™32, AlarmWorX™32 and ScriptWorX™32) at Ford Motor Company on the engine test stands, designed by Comau Pico at their Dearborn, MI engine plant. Comau Pico has also installed this same software at other Ford plants including those in Mexico and Canada. GENESIS32 was used primarily for its ease of use, speed and its 100 percent OPC compliant capabilities. All testing parameters are recorded and trending data stored via LAN to a historical database. Comau Pico has installed over 50 of these engine test stands into six Ford engine plants. Ford is also using ICONICS GENESIS32 software on “In Process” test stands at other facilities.
Operational Impact
Quantitative Benefit
Case Study missing?
Start adding your own!
Register with your work email and create a new case study profile for your business.
Related Case Studies.
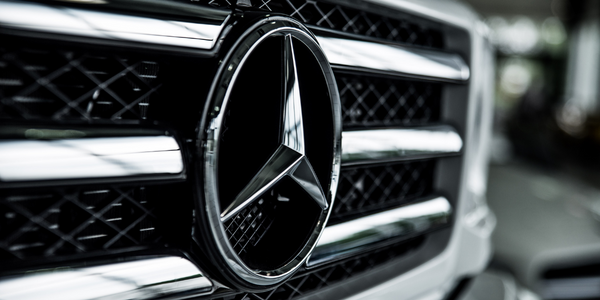
Case Study
Integral Plant Maintenance
Mercedes-Benz and his partner GAZ chose Siemens to be its maintenance partner at a new engine plant in Yaroslavl, Russia. The new plant offers a capacity to manufacture diesel engines for the Russian market, for locally produced Sprinter Classic. In addition to engines for the local market, the Yaroslavl plant will also produce spare parts. Mercedes-Benz Russia and his partner needed a service partner in order to ensure the operation of these lines in a maintenance partnership arrangement. The challenges included coordinating the entire maintenance management operation, in particular inspections, corrective and predictive maintenance activities, and the optimizing spare parts management. Siemens developed a customized maintenance solution that includes all electronic and mechanical maintenance activities (Integral Plant Maintenance).
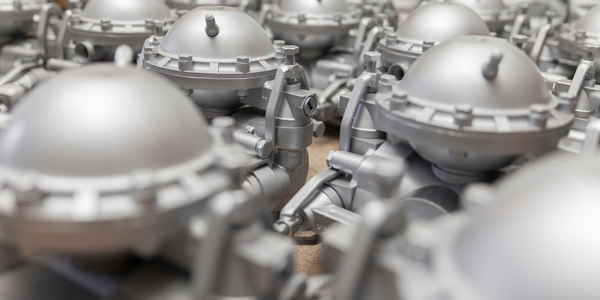
Case Study
Monitoring of Pressure Pumps in Automotive Industry
A large German/American producer of auto parts uses high-pressure pumps to deburr machined parts as a part of its production and quality check process. They decided to monitor these pumps to make sure they work properly and that they can see any indications leading to a potential failure before it affects their process.