Customer Company Size
Large Corporate
Region
- Europe
Country
- Germany
Product
- ICONICS’ HMI/SCADA suite
- ICONICS data historian
Tech Stack
- Database for Online Process Analysis and Control (DOPAC)
- Statistical Process Control (SPC)
Implementation Scale
- Enterprise-wide Deployment
Impact Metrics
- Productivity Improvements
- Innovation Output
Technology Category
- Application Infrastructure & Middleware - Data Exchange & Integration
Applicable Industries
- Automotive
Applicable Functions
- Discrete Manufacturing
- Quality Assurance
Use Cases
- Manufacturing System Automation
- Real-Time Location System (RTLS)
Services
- System Integration
About The Customer
Continental AG, headquartered in Hanover, Germany, is the world’s fourth largest tire manufacturer. Founded in 1871 as a rubber manufacturer, the company now contains additional divisions handling brake systems, interior electronics, automotive safety, powertrain/chassis components, tachographs and additional parts for the automotive and transportation industries. Almost every third car in Europe is delivered with tires from Continental. Its Division Tires features tire brands like Continental, Uniroyal, General Tire, Semperit, Barum and many more. Today the company has over 227,000 employees in 56 countries.
The Challenge
Continental AG, a leading tire manufacturer, sought to update their process analysis and control systems across 18 separate locations worldwide. The company aimed to develop a system capable of near real-time data collection from production equipment for process and product analysis and optimization. This led to the initiation of the 'DOPAC' project, standing for 'Database for Online Process Analysis and Control'. A pilot project began in 2016 in the company’s Puchov, Slovakia plant, with a year spent on prototype development. The company decided to move on from installed legacy systems and, after considering multiple vendor solutions, decided upon ICONICS HMI/SCADA and data historian to comprise the heart of DOPAC.
The Solution
Continental AG selected ICONICS’ HMI/SCADA suite, in addition to the high-speed, reliable, robust plant historian. The new system was intended to steer and continuously improve the company’s production processes based on statistical process control (SPC) measurement of product performance-relevant data. A taskforce was put together to clearly define the company’s IT requirements, as the right pertinent performance data was deemed necessary for continuous improvement. On top actual product and process data were for intended advanced analytics. High on the list was real-time data collection. Another necessity was a redundant architecture, including data buffering at sources. The company also highly valued integrating specification systems, high-rate data compression and data mapping.
Operational Impact
Case Study missing?
Start adding your own!
Register with your work email and create a new case study profile for your business.
Related Case Studies.
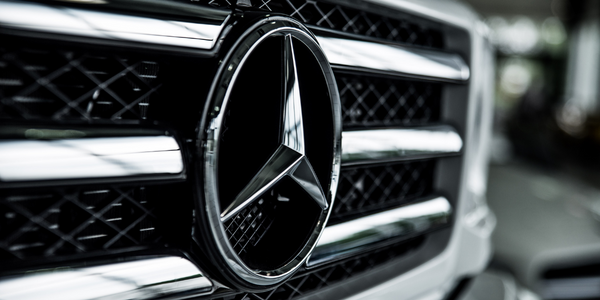
Case Study
Integral Plant Maintenance
Mercedes-Benz and his partner GAZ chose Siemens to be its maintenance partner at a new engine plant in Yaroslavl, Russia. The new plant offers a capacity to manufacture diesel engines for the Russian market, for locally produced Sprinter Classic. In addition to engines for the local market, the Yaroslavl plant will also produce spare parts. Mercedes-Benz Russia and his partner needed a service partner in order to ensure the operation of these lines in a maintenance partnership arrangement. The challenges included coordinating the entire maintenance management operation, in particular inspections, corrective and predictive maintenance activities, and the optimizing spare parts management. Siemens developed a customized maintenance solution that includes all electronic and mechanical maintenance activities (Integral Plant Maintenance).
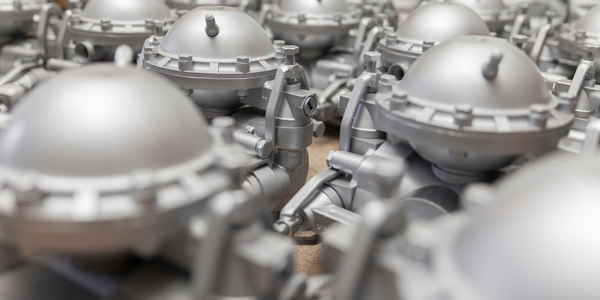
Case Study
Monitoring of Pressure Pumps in Automotive Industry
A large German/American producer of auto parts uses high-pressure pumps to deburr machined parts as a part of its production and quality check process. They decided to monitor these pumps to make sure they work properly and that they can see any indications leading to a potential failure before it affects their process.