Customer Company Size
Large Corporate
Region
- America
Country
- United States
Product
- GENESIS32™
- GraphWorX™
- TrendWorX™
- AlarmWorX™
- WebHMI™
Tech Stack
- Automation Software
- Data Collection Software
- Monitoring Software
Implementation Scale
- Enterprise-wide Deployment
Impact Metrics
- Environmental Impact Reduction
- Energy Saving
Technology Category
- Application Infrastructure & Middleware - Data Exchange & Integration
Applicable Industries
- Renewable Energy
- Agriculture
Applicable Functions
- Maintenance
- Quality Assurance
Use Cases
- Energy Management System
- Remote Asset Management
Services
- System Integration
- Software Design & Engineering Services
About The Customer
Microgy is a subsidiary of Environmental Power Corporation, a company that has been contributing to environmentally responsible energy operations since 1982. Microgy develops facilities to efficiently and reliably produce clean, renewable gas from agriculture and food industry wastes. The company uses anaerobic digestion, where methane-rich biogas is extracted from waste to produce electric power. This process not only generates fuel used in various applications but also reduces manure odor and creates significant quantities of marketable carbon credits. The biogas is utilized in internal combustion engines to generate electric power and heat, used as-is to offset fossil fuels, or is captured and further refined to pipeline quality Renewable Natural Gas (RNG).
The Challenge
Microgy, a subsidiary of Environmental Power Corporation, develops facilities to efficiently and reliably produce clean, renewable gas from agriculture and food industry wastes. The company uses anaerobic digestion, where methane-rich biogas is extracted from waste to produce electric power, helping farms and businesses responsibly manage the wastes they generate. The company operates in four renewable energy facilities across the United States' Western and Midwestern regions. The challenge was to monitor and control systems at these facilities, provide real-time monitoring and control, and convey data from remote locations to a corporate location in Tarrytown, New York.
The Solution
ICONICS automation solutions were applied in four of Microgy’s renewable energy facilities. The software solutions deployed include GENESIS32™, GraphWorX™, TrendWorX™, and AlarmWorX™, which are used to monitor and control systems at Microgy’s facilities. AlarmWorX MMX provides paging for alarms. At Microgy’s corporate level, ICONICS’ WebHMI™ provides internal access and visibility to all sites. Over the course of three months per facility, Wunderlich-Malec Engineering integrated ICONICS’ monitoring and control systems. The control system is designed to provide automatic operation of all systems components with built-in fail to safe modes in the event of an upset. Data is conveyed from remote locations to a corporate location in Tarrytown, New York via WebHMI, providing data collection, batch-transfer, and trending from all sites.
Operational Impact
Quantitative Benefit
Case Study missing?
Start adding your own!
Register with your work email and create a new case study profile for your business.
Related Case Studies.

Case Study
Remote Monitoring & Predictive Maintenance App for a Solar Energy System
The maintenance & tracking of various modules was an overhead for the customer due to the huge labor costs involved. Being an advanced solar solutions provider, they wanted to ensure early detection of issues and provide the best-in-class customer experience. Hence they wanted to automate the whole process.
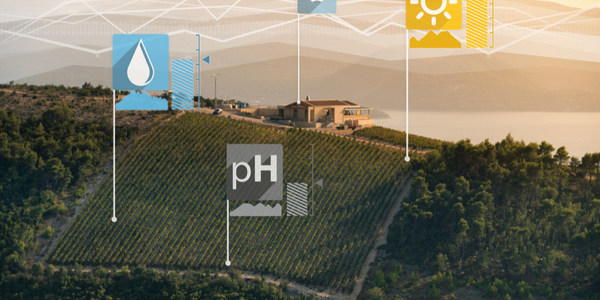
Case Study
Intelligent Farming with ThingWorx Analytics
Z Farms was facing three challenges: costly irrigation systems with water as a limited resource, narrow optimal ranges of soil moisture for growth with difficult maintenance and farm operators could not simply turn on irrigation systems like a faucet.
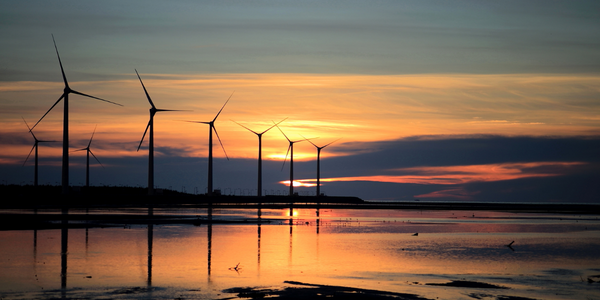
Case Study
Vestas: Turning Climate into Capital with Big Data
Making wind a reliable source of energy depends greatly on the placement of the wind turbines used to produce electricity. Turbulence is a significant factor as it strains turbine components, making them more likely to fail. Vestas wanted to pinpoint the optimal location for wind turbines to maximize power generation and reduce energy costs.
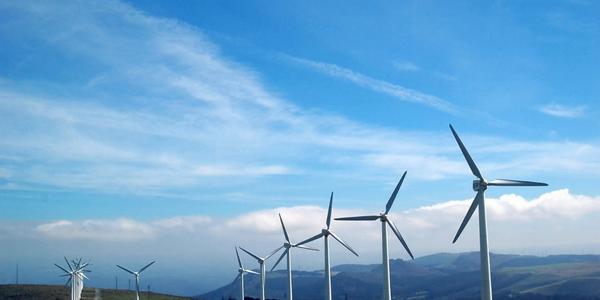
Case Study
Siemens Wind Power
Wind provides clean, renewable energy. The core concept is simple: wind turbines spin blades to generate power. However, today's systems are anything but simple. Modern wind turbines have blades that sweep a 120 meter circle, cost more than 1 million dollars and generate multiple megawatts of power. Each turbine may include up to 1,000 sensors and actuators – integrating strain gages, bearing monitors and power conditioning technology. The turbine can control blade speed and power generation by altering the blade pitch and power extraction. Controlling the turbine is a sophisticated job requiring many cooperating processors closing high-speed loops and implementing intelligent monitoring and optimization algorithms. But the real challenge is integrating these turbines so that they work together. A wind farm may include hundreds of turbines. They are often installed in difficult-to-access locations at sea. The farm must implement a fundamentally and truly distributed control system. Like all power systems, the goal of the farm is to match generation to load. A farm with hundreds of turbines must optimize that load by balancing the loading and generation across a wide geography. Wind, of course, is dynamic. Almost every picture of a wind farm shows a calm sea and a setting sun. But things get challenging when a storm goes through the wind farm. In a storm, the control system must decide how to take energy out of gusts to generate constant power. It must intelligently balance load across many turbines. And a critical consideration is the loading and potential damage to a half-billion-dollar installed asset. This is no environment for a slow or undependable control system. Reliability and performance are crucial.
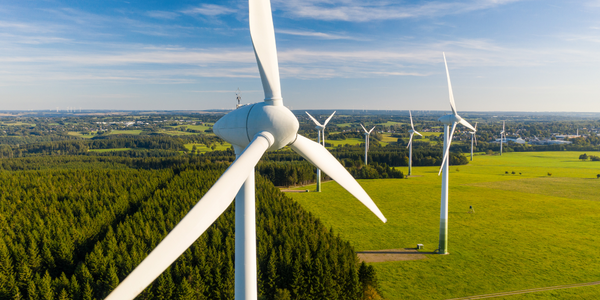
Case Study
Remote Monitoring and Control for a Windmill Generator
As concerns over global warming continue to grow, green technologies are becoming increasingly popular. Wind turbine companies provide an excellent alternative to burning fossil fuels by harnessing kinetic energy from the wind and converting it into electricity. A typical wind farm may include over 80 wind turbines so efficient and reliable networks to manage and control these installations are imperative. Each wind turbine includes a generator and a variety of serial components such as a water cooler, high voltage transformer, ultrasonic wind sensors, yaw gear, blade bearing, pitch cylinder, and hub controller. All of these components are controlled by a PLC and communicate with the ground host. Due to the total integration of these devices into an Ethernet network, one of our customers in the wind turbine industry needed a serial-to-Ethernet solution that can operate reliably for years without interruption.