Customer Company Size
SME
Region
- Europe
Country
- United Kingdom
Product
- ICONICS GENESIS™32 Software
- AlarmWorX™32
- TrendWorX™32
- GraphWorX™32
Tech Stack
- SCADA
- OPC
- Windows operating system
Implementation Scale
- Enterprise-wide Deployment
Impact Metrics
- Productivity Improvements
- Innovation Output
Technology Category
- Application Infrastructure & Middleware - API Integration & Management
Applicable Industries
- Oil & Gas
- Marine & Shipping
Applicable Functions
- Discrete Manufacturing
- Maintenance
Use Cases
- Remote Asset Management
- Machine Condition Monitoring
Services
- System Integration
- Software Design & Engineering Services
About The Customer
Hydrovision Ltd. is a world leader in the manufacturing of Remotely Operated Vehicles (ROVs). The company is based in the UK and specializes in the design and manufacturing of sub-sea robotic systems. These systems are used in various industries including Underwater Salvage, Cable Laying, and Offshore Oil drilling. The systems need to meet extremely demanding standards of performance, control, and endurance. Hydrovision is a private limited company.
The Challenge
Hydrovision Ltd., a leading manufacturer of Remotely Operated Vehicles (ROVs), required a new scalable control system for their ROVs, sub-sea tooling, and other custom tooling applications. The specifications demanded a PC-based system running under a Windows operating system and meeting open standards like OPC. The system needed to be scalable, maintainable, easy to modify after implementation, and economical. The company also wanted a system that would allow their customers to make their own modifications to the machines for different tooling or use applications.
The Solution
Hydrovision Ltd. selected ICONICS GENESIS™32 Software suite of SCADA and OPC products to meet their requirements. The GENESIS32 software suite of applications operate seamlessly together, communicating solely via an OPC server which allows easy interface to any industry standard hardware and software systems. The software also has an intuitive development environment, which allows for speedy development and re-engineering by both experienced and new SCADA Engineers. ICONICS GENESIS32’s GraphWorX32 software was used to create the Operator Interface HMI screen using multiple touch screen control panels for control of the ROV machine with a single main display to continuously present the system data.
Operational Impact
Case Study missing?
Start adding your own!
Register with your work email and create a new case study profile for your business.
Related Case Studies.
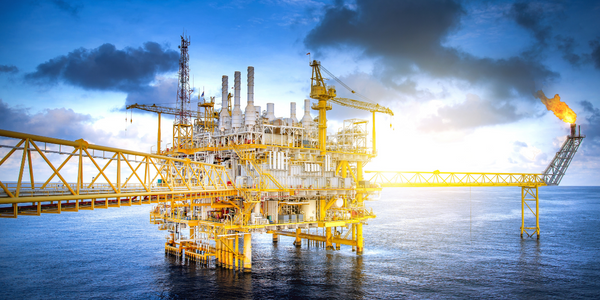
Case Study
Taking Oil and Gas Exploration to the Next Level
DownUnder GeoSolutions (DUG) wanted to increase computing performance by 5 to 10 times to improve seismic processing. The solution must build on current architecture software investments without sacrificing existing software and scale computing without scaling IT infrastructure costs.
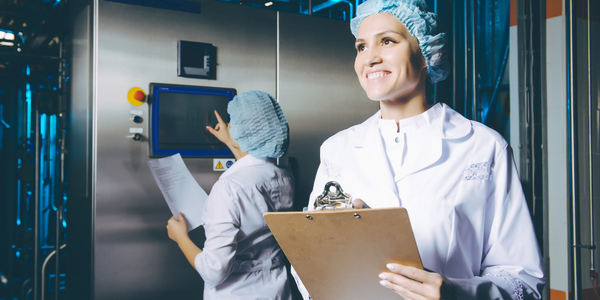
Case Study
Remote Wellhead Monitoring
Each wellhead was equipped with various sensors and meters that needed to be monitored and controlled from a central HMI, often miles away from the assets in the field. Redundant solar and wind generators were installed at each wellhead to support the electrical needs of the pumpstations, temperature meters, cameras, and cellular modules. In addition to asset management and remote control capabilities, data logging for remote surveillance and alarm notifications was a key demand from the customer. Terra Ferma’s solution needed to be power efficient, reliable, and capable of supporting high-bandwidth data-feeds. They needed a multi-link cellular connection to a central server that sustained reliable and redundant monitoring and control of flow meters, temperature sensors, power supply, and event-logging; including video and image files. This open-standard network needed to interface with the existing SCADA and proprietary network management software.
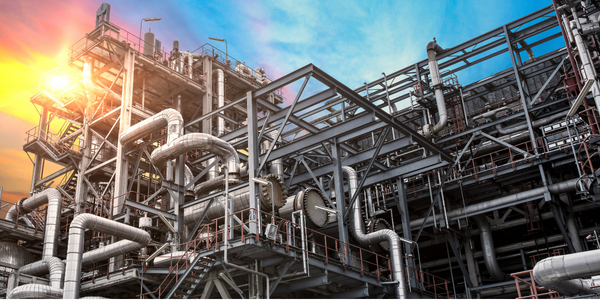
Case Study
Refinery Saves Over $700,000 with Smart Wireless
One of the largest petroleum refineries in the world is equipped to refine various types of crude oil and manufacture various grades of fuel from motor gasoline to Aviation Turbine Fuel. Due to wear and tear, eight hydrogen valves in each refinery were leaking, and each cost $1800 per ton of hydrogen vented. The plant also had leakage on nearly 30 flare control hydrocarbon valves. The refinery wanted a continuous, online monitoring system that could catch leaks early, minimize hydrogen and hydrocarbon production losses, and improve safety for maintenance.