Customer Company Size
Large Corporate
Region
- Europe
Country
- Italy
Product
- ICONICS GENESIS32
- GraphWorX™32
- AlarmWorX™32
- TrendWorX™32
- ScriptWorX™32
Tech Stack
- OPC Server
- ODBC driver
- Sybase database
Implementation Scale
- Enterprise-wide Deployment
Impact Metrics
- Productivity Improvements
- Digital Expertise
Technology Category
- Application Infrastructure & Middleware - API Integration & Management
- Application Infrastructure & Middleware - Data Exchange & Integration
Applicable Industries
- Automotive
- Electronics
Applicable Functions
- Discrete Manufacturing
- Quality Assurance
Use Cases
- Machine Condition Monitoring
- Predictive Maintenance
Services
- Software Design & Engineering Services
- System Integration
About The Customer
IDRA Presse is a leading producer of Pressure Die Casting Machines. IDRA manufacturers large (20 to 5000 Ton clamping force) metal die casting machines are shipped to clients worldwide. The market focus for IDRA is in automotive, where their machines are used to cast engine blocks, car body frames and other automotive parts for clients such as Mercedes-Benz, Ford, GM, Chrysler, VW, BMW, Fiat and many others. They also have casting customers such as Black & Decker, Electrolux, Siemens and Singer. Over 80% of their sales are in Europe.
The Challenge
IDRA Presse, a leading producer of Pressure Die Casting Machines, had the requirement of sampling process parameters on their Pressure Die Casting Machines at 10,000 cycles/sec and needed a software system to have the ability to collect real time data at those rates. They used an external sampling system with real time operating software. This system was connected through an Ethernet link with ICONICS software using an OPC Server on a PC, where TrendWorX32 trends the data collected. This data was then sent via a LAN to a centralized database for final evaluation and storage. IDRA selected ICONICS to provide them with state-of-the-art injection press machine monitoring and control after evaluating nine other suppliers including Intellution, Wonderware, WinCC and RSView. IDRA replaced their existing Orsi Cube system with the GENESIS32™ HMI Software suite.
The Solution
ICONICS GENESIS32 software has been deployed to provide supervision and operator visualization to the metal injection press machine operations. The operator has the ability to set the machine parameters to display critical real time information about the process. All the real time injection data from the press machine is collected and stored in a relational database. All collected data is available in a graphical display that also includes third party ActiveX’s data. IDRA also uses ICONICS TrendWorX32 to display and store process data. Each press machine is equipped with dual network interface cards, one for communicating collected real time data over their LAN to be stored into their database. The second network interface is used by the end customer to provide them with access to all the stored data on that press machine through an ODBC driver. A modem is also installed on the press machine for remote diagnostics and/or update modifications from IDRA. The press machine system interfaces with up to 4 Siemens PLCs, 1 Allen-Bradley PLC and has over 500 I/O points with 300 Tags.
Operational Impact
Quantitative Benefit
Case Study missing?
Start adding your own!
Register with your work email and create a new case study profile for your business.
Related Case Studies.
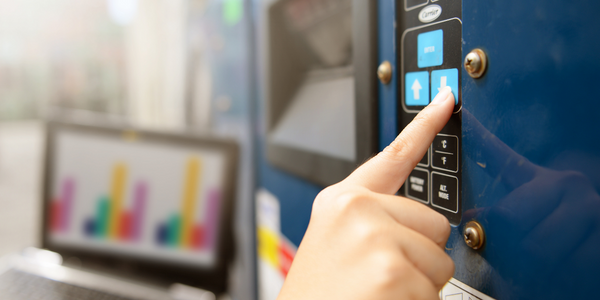
Case Study
Remote Temperature Monitoring of Perishable Goods Saves Money
RMONI was facing temperature monitoring challenges in a cold chain business. A cold chain must be established and maintained to ensure goods have been properly refrigerated during every step of the process, making temperature monitoring a critical business function. Manual registration practice can be very costly, labor intensive and prone to mistakes.
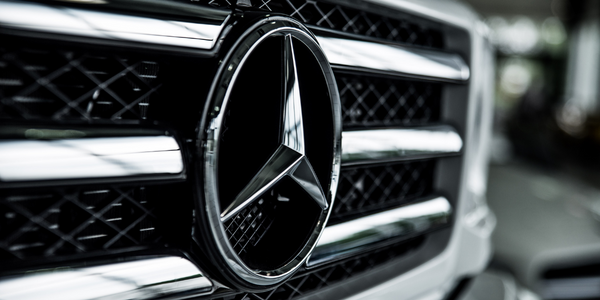
Case Study
Integral Plant Maintenance
Mercedes-Benz and his partner GAZ chose Siemens to be its maintenance partner at a new engine plant in Yaroslavl, Russia. The new plant offers a capacity to manufacture diesel engines for the Russian market, for locally produced Sprinter Classic. In addition to engines for the local market, the Yaroslavl plant will also produce spare parts. Mercedes-Benz Russia and his partner needed a service partner in order to ensure the operation of these lines in a maintenance partnership arrangement. The challenges included coordinating the entire maintenance management operation, in particular inspections, corrective and predictive maintenance activities, and the optimizing spare parts management. Siemens developed a customized maintenance solution that includes all electronic and mechanical maintenance activities (Integral Plant Maintenance).