Customer Company Size
Large Corporate
Region
- Europe
Country
- Germany
Product
- SAP NetWeaver
- GENESIS64
Tech Stack
- Web-enabled technology
- OPC-integrated technology
- 64-bit computing
Implementation Scale
- Enterprise-wide Deployment
Impact Metrics
- Productivity Improvements
- Innovation Output
Technology Category
- Platform as a Service (PaaS) - Connectivity Platforms
Applicable Functions
- Discrete Manufacturing
- Product Research & Development
Use Cases
- Manufacturing System Automation
- Process Control & Optimization
Services
- Software Design & Engineering Services
About The Customer
SAP is the world’s leading provider of business software. Today, more than 46,100 customers in more than 120 countries run SAP® software – from distinct solutions addressing the needs of small businesses and midsize companies to suite offerings for global organizations. Powered by the SAP NetWeaver® technology platform to drive innovation and enable business change, SAP software helps enterprises of all sizes worldwide improve customer relationships, enhance partner collaboration and create efficiencies across their supply chains and business operations. SAP solution portfolios support the unique business processes of more than 25 industries, including high tech, retail, financial services, healthcare and the public sector. With subsidiaries in more than 50 countries, the company is listed on several exchanges, including the Frankfurt stock exchange and NYSE under the symbol “SAP”.
The Challenge
The Future Factory Initiative (FFI) is a joint effort of SAP Research and external partner organizations, including ICONICS. It is active in key areas including a Living Lab, a Real-World Manufacturing Testbed and a Center of Excellence. The initiative is a set of innovative demonstrators showing the potential of real-world-integrated business processes in the manufacturing domain. The challenge was to create a testbed that shows leading edge software and the latest hardware developments with different scenarios, products, and prototypes in a distributed manufacturing environment. The testbed needed to span multiple manufacturers and demonstrate the viability of prototypes.
The Solution
ICONICS’ GENESIS64™ 64-bit, OPC-integrated, Web-enabled HMI/SCADA suite is currently utilized by SAP Research at the Future Factory Initiative. GENESIS64 provides customers with a 360° view of their entire organization, providing users with the power to quickly and efficiently add 3D symbols and animation to graphic visualizations of business processes and bring them to life. Researchers at SAP Research’s CEC Dresden location have had a chance to put ICONICS “next generation of automation software” to the test in as “real-world” circumstances as they have been able to produce and have remarked on the outstanding quality of this latest ICONICS software solution.
Operational Impact
Case Study missing?
Start adding your own!
Register with your work email and create a new case study profile for your business.
Related Case Studies.
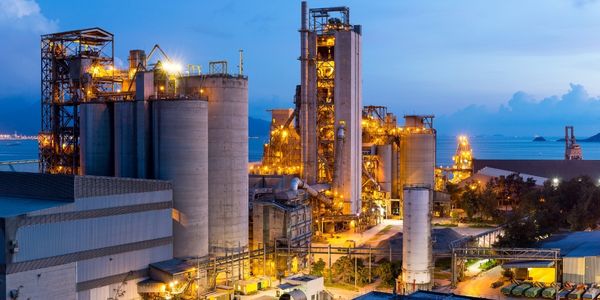
Case Study
System 800xA at Indian Cement Plants
Chettinad Cement recognized that further efficiencies could be achieved in its cement manufacturing process. It looked to investing in comprehensive operational and control technologies to manage and derive productivity and energy efficiency gains from the assets on Line 2, their second plant in India.
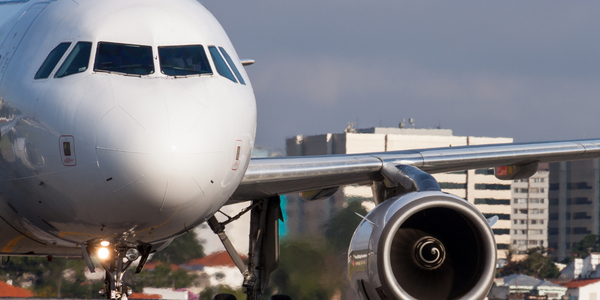
Case Study
Airbus Soars with Wearable Technology
Building an Airbus aircraft involves complex manufacturing processes consisting of thousands of moving parts. Speed and accuracy are critical to business and competitive advantage. Improvements in both would have high impact on Airbus’ bottom line. Airbus wanted to help operators reduce the complexity of assembling cabin seats and decrease the time required to complete this task.
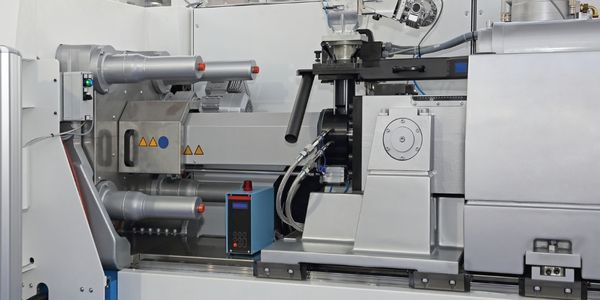
Case Study
Plastic Spoons Case study: Injection Moulding
In order to meet customer expectations by supplying a wide variety of packaging units, from 36 to 1000 spoons per package, a new production and packaging line needed to be built. DeSter wanted to achieve higher production capacity, lower cycle time and a high degree of operator friendliness with this new production line.
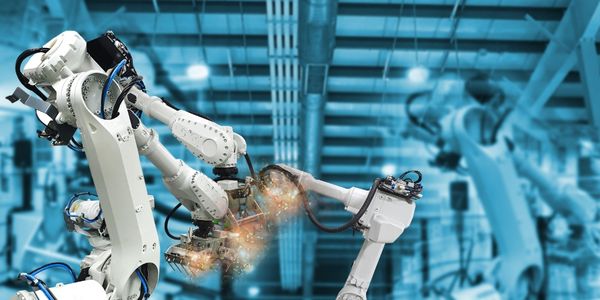
Case Study
Robot Saves Money and Time for US Custom Molding Company
Injection Technology (Itech) is a custom molder for a variety of clients that require precision plastic parts for such products as electric meter covers, dental appliance cases and spools. With 95 employees operating 23 molding machines in a 30,000 square foot plant, Itech wanted to reduce man hours and increase efficiency.