Customer Company Size
Large Corporate
Region
- America
Country
- United States
Product
- Parsable
Tech Stack
- Data Analysis
- Digital Workflow
Implementation Scale
- Enterprise-wide Deployment
Impact Metrics
- Cost Savings
- Productivity Improvements
Technology Category
- Platform as a Service (PaaS) - Data Management Platforms
Applicable Industries
- Oil & Gas
Applicable Functions
- Discrete Manufacturing
- Quality Assurance
Use Cases
- Predictive Maintenance
Services
- Data Science Services
About The Customer
Scientific Drilling International (Scientific Drilling) is a leading directional drilling services provider. The company is headquartered in Houston, TX and has nearly 40 locations across 26 countries. Over the past five years, Scientific Drilling has doubled-down on their commitment to tool performance, strategic cost reduction, and process optimization to provide best-in-class technology and customer service. Their long-term goal is to be the 'ultimate partner in wellbore placement'. To achieve this vision, they have been focusing on optimizing specific areas of their operations by evaluating the key drivers of customer value, such as process controls, change management, and quality.
The Challenge
Scientific Drilling, a leading provider of directional drilling equipment and services, aimed to become the 'ultimate partner in wellbore placement'. To achieve this, they focused on tool performance, strategic cost reduction, and process optimization. Rob McKee, SVP of Manufacturing and Product Support, was tasked with driving the reliability component of these performance improvements. The team recognized the need to integrate in-depth data analysis into their repair processes at Scientific Drilling’s motor shops. They aimed for digital workflows for standard assembly, disassembly, and repair procedures, actionable insights and quick visibility into quality workflows, near real-time data collection during repair operations, 100% conformance to process standards, and measurable improvements in cost and reliability.
The Solution
Scientific Drilling adopted Parsable's platform to integrate standard work instructions and procedures for all processes related to drill motor assembly, disassembly, and repair into digital workflows. The intuitive user interface of Parsable enabled the team to complete this integration in just 8 weeks. Users could access digital workflows with inline procedural content and execute work on the go, allowing for seamless execution of each process step from start to finish. Supervisors at Scientific Drilling used Parsable to digitally oversee motor repair workflows, ensure quality, and iterate their operations quickly. With access to execution data, Scientific Drilling was able to make knowledgeable decisions from the data and has become a continuous source of actionable process and technology improvement.
Operational Impact
Quantitative Benefit
Case Study missing?
Start adding your own!
Register with your work email and create a new case study profile for your business.
Related Case Studies.
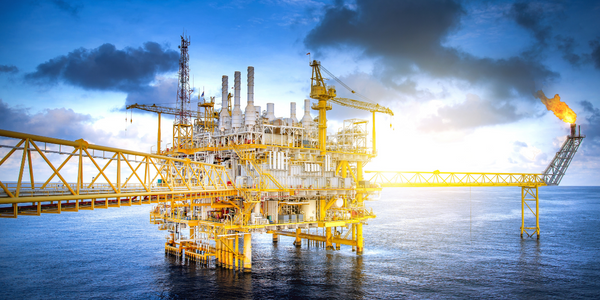
Case Study
Taking Oil and Gas Exploration to the Next Level
DownUnder GeoSolutions (DUG) wanted to increase computing performance by 5 to 10 times to improve seismic processing. The solution must build on current architecture software investments without sacrificing existing software and scale computing without scaling IT infrastructure costs.
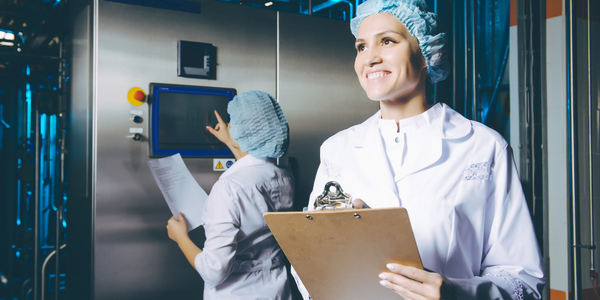
Case Study
Remote Wellhead Monitoring
Each wellhead was equipped with various sensors and meters that needed to be monitored and controlled from a central HMI, often miles away from the assets in the field. Redundant solar and wind generators were installed at each wellhead to support the electrical needs of the pumpstations, temperature meters, cameras, and cellular modules. In addition to asset management and remote control capabilities, data logging for remote surveillance and alarm notifications was a key demand from the customer. Terra Ferma’s solution needed to be power efficient, reliable, and capable of supporting high-bandwidth data-feeds. They needed a multi-link cellular connection to a central server that sustained reliable and redundant monitoring and control of flow meters, temperature sensors, power supply, and event-logging; including video and image files. This open-standard network needed to interface with the existing SCADA and proprietary network management software.
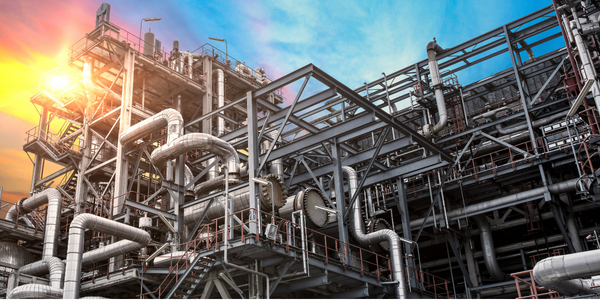
Case Study
Refinery Saves Over $700,000 with Smart Wireless
One of the largest petroleum refineries in the world is equipped to refine various types of crude oil and manufacture various grades of fuel from motor gasoline to Aviation Turbine Fuel. Due to wear and tear, eight hydrogen valves in each refinery were leaking, and each cost $1800 per ton of hydrogen vented. The plant also had leakage on nearly 30 flare control hydrocarbon valves. The refinery wanted a continuous, online monitoring system that could catch leaks early, minimize hydrogen and hydrocarbon production losses, and improve safety for maintenance.