Technology Category
- Networks & Connectivity - 5G
- Platform as a Service (PaaS) - Application Development Platforms
Applicable Industries
- Automotive
- Cement
Applicable Functions
- Maintenance
- Sales & Marketing
Use Cases
- Vehicle Performance Monitoring
- Vehicle-to-Infrastructure
Services
- System Integration
About The Customer
Dealer-FX is a fast-growing software solution provider that streamlines vehicle maintenance. Founded in 2007, the company aims to improve vehicle maintenance efficiency, transparency, and convenience. Their tools assist dealerships in serving their customers better by facilitating booking appointments, estimating quotes, and ensuring clear internal communication. After being acquired by Snap-On Incorporated in early 2021, Dealer-FX recognized the need to build a more sophisticated contactless communications solution. The company's core requirement was to adopt a backend chat infrastructure that could scale with them as they grew.
The Challenge
Dealer-FX, an automotive software company, was facing a challenge with its existing SMS text messaging platform. The platform was used by service dealerships to communicate with vehicle owners. However, as the company scaled, it needed a more sophisticated communication platform with features such as 1:1 chat and automated group messaging to enhance the car maintenance experience. The existing disjointed communication tools were not sufficient to keep all dealership departments connected and updated about a customer's vehicle status. After several months of attempting to build a messaging platform in-house, Dealer-FX engineers decided to explore using a third-party chat API solution instead.
The Solution
Dealer-FX turned to Stream's flexible backend chat API infrastructure to customize a communication platform that could store, filter, and search certain data types, including users, channels, and messages. This enabled Dealer-FX to have a high-performing automated platform. The company worked closely with Stream's customer success team to integrate the Stream Chat API into their product. Instead of using Stream's front-end UI kits, Dealer-FX engineers customized the entire front-end user experience for an on-brand appearance. The tool extracts meta-data from each repair order and can automatically generate a group conversation that includes key stakeholders from around the dealership. This functionality allows Dealer-FX the unique capability to enable their customers to connect to their app in myriad ways.
Operational Impact
Quantitative Benefit
Case Study missing?
Start adding your own!
Register with your work email and create a new case study profile for your business.
Related Case Studies.
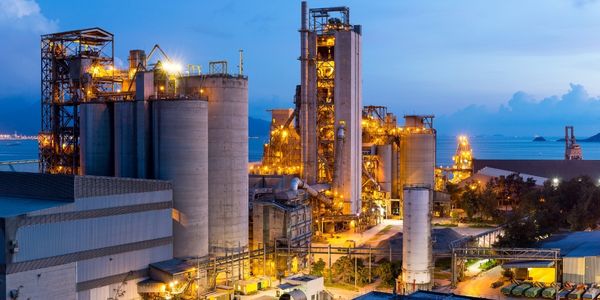
Case Study
System 800xA at Indian Cement Plants
Chettinad Cement recognized that further efficiencies could be achieved in its cement manufacturing process. It looked to investing in comprehensive operational and control technologies to manage and derive productivity and energy efficiency gains from the assets on Line 2, their second plant in India.
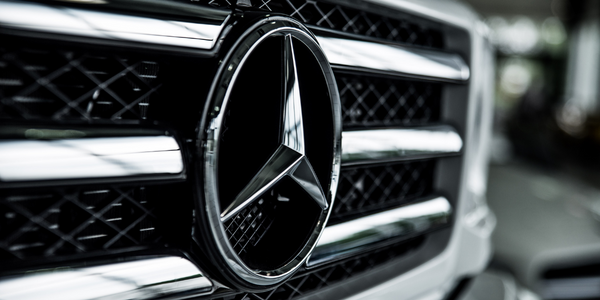
Case Study
Integral Plant Maintenance
Mercedes-Benz and his partner GAZ chose Siemens to be its maintenance partner at a new engine plant in Yaroslavl, Russia. The new plant offers a capacity to manufacture diesel engines for the Russian market, for locally produced Sprinter Classic. In addition to engines for the local market, the Yaroslavl plant will also produce spare parts. Mercedes-Benz Russia and his partner needed a service partner in order to ensure the operation of these lines in a maintenance partnership arrangement. The challenges included coordinating the entire maintenance management operation, in particular inspections, corrective and predictive maintenance activities, and the optimizing spare parts management. Siemens developed a customized maintenance solution that includes all electronic and mechanical maintenance activities (Integral Plant Maintenance).
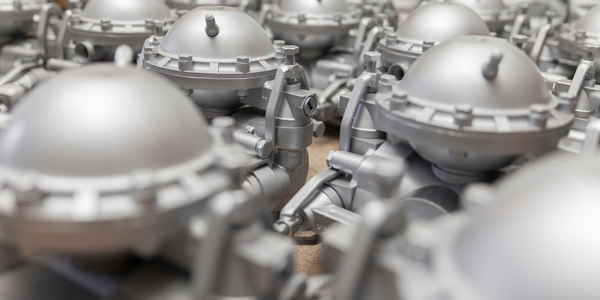
Case Study
Monitoring of Pressure Pumps in Automotive Industry
A large German/American producer of auto parts uses high-pressure pumps to deburr machined parts as a part of its production and quality check process. They decided to monitor these pumps to make sure they work properly and that they can see any indications leading to a potential failure before it affects their process.