Customer Company Size
Large Corporate
Region
- Europe
Country
- United Kingdom
Product
- JDA® Dispatcher WMS
- JDA® Third Party Billing
- Socius24 Users Service Portal (USP)
Tech Stack
- Amazon Web Services
Implementation Scale
- Enterprise-wide Deployment
Impact Metrics
- Productivity Improvements
- Customer Satisfaction
Technology Category
- Functional Applications - Warehouse Management Systems (WMS)
Applicable Industries
- Automotive
- Food & Beverage
- Packaging
Applicable Functions
- Logistics & Transportation
- Warehouse & Inventory Management
Use Cases
- Warehouse Automation
- Inventory Management
Services
- Cloud Planning, Design & Implementation Services
- System Integration
About The Customer
ATL is a fast-growing family-owned business headquartered in Foston, South Derbyshire, UK. The company offers mission-critical warehousing and logistics solutions to a wide range of customers, including automotive, food and beverage, and packaging companies, among others. With over a million feet of warehouse space, approximately 100 commercial vehicles and 150 trailers, ATL stores and delivers products for a wide range of customers. The company has plans to double its business size over the next five years.
The Challenge
ATL, a fast-growing family-owned business offering mission-critical warehousing and logistics solutions to automotive, food and beverage, and packaging companies, among others, was facing challenges with its existing warehousing management system (WMS). The system lacked the flexibility and systematic traceability required to enable growth in the warehousing arm of the business and diversify in new products that required multi-level tracking. With plans to double business size over the next five years, accurate management and control of day-to-day warehouse operations was critical. The company needed a solution that could improve the speed and accuracy of its warehousing and logistics activities.
The Solution
In 2017, ATL decided to implement JDA® Dispatcher Warehouse Management™ and JDA® Third Party Billing to increase the speed and accuracy of its warehousing and logistics activities. The implementation was led by Socius24, JDA’s UK-based reseller partner. The company launched JDA Dispatcher WMS on the Amazon Web Services platform, along with JDA Third Party Billing and the Socius24 developed User Service Portal (USP). As a result of its cloud-based implementation, ATL was able to quickly migrate about 30 percent of its customers to the JDA solution. The JDA solution enabled ATL to track products by location, weight and other detailed characteristics. They could define specific rules and make sure they are honored, ensuring the integrity of all the stock they manage for their customers.
Operational Impact
Quantitative Benefit
Case Study missing?
Start adding your own!
Register with your work email and create a new case study profile for your business.
Related Case Studies.

Case Study
The Kellogg Company
Kellogg keeps a close eye on its trade spend, analyzing large volumes of data and running complex simulations to predict which promotional activities will be the most effective. Kellogg needed to decrease the trade spend but its traditional relational database on premises could not keep up with the pace of demand.
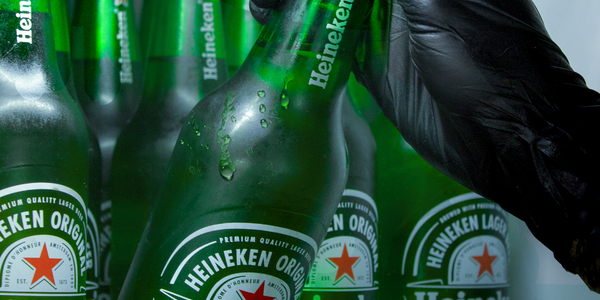
Case Study
HEINEKEN Uses the Cloud to Reach 10.5 Million Consumers
For 2012 campaign, the Bond promotion, it planned to launch the campaign at the same time everywhere on the planet. That created unprecedented challenges for HEINEKEN—nowhere more so than in its technology operation. The primary digital content for the campaign was a 100-megabyte movie that had to play flawlessly for millions of viewers worldwide. After all, Bond never fails. No one was going to tolerate a technology failure that might bruise his brand.Previously, HEINEKEN had supported digital media at its outsourced datacenter. But that datacenter lacked the computing resources HEINEKEN needed, and building them—especially to support peak traffic that would total millions of simultaneous hits—would have been both time-consuming and expensive. Nor would it have provided the geographic reach that HEINEKEN needed to minimize latency worldwide.
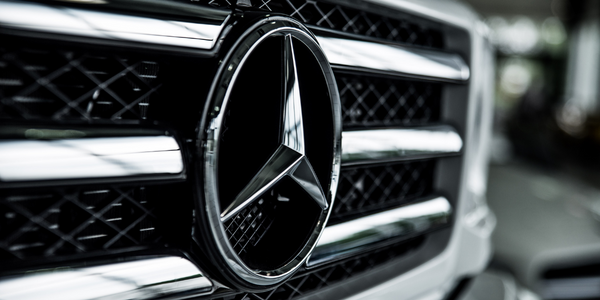
Case Study
Integral Plant Maintenance
Mercedes-Benz and his partner GAZ chose Siemens to be its maintenance partner at a new engine plant in Yaroslavl, Russia. The new plant offers a capacity to manufacture diesel engines for the Russian market, for locally produced Sprinter Classic. In addition to engines for the local market, the Yaroslavl plant will also produce spare parts. Mercedes-Benz Russia and his partner needed a service partner in order to ensure the operation of these lines in a maintenance partnership arrangement. The challenges included coordinating the entire maintenance management operation, in particular inspections, corrective and predictive maintenance activities, and the optimizing spare parts management. Siemens developed a customized maintenance solution that includes all electronic and mechanical maintenance activities (Integral Plant Maintenance).