Technology Category
- Platform as a Service (PaaS) - Application Development Platforms
Applicable Industries
- Cement
- Mining
Applicable Functions
- Product Research & Development
About The Customer
The Deutsches Bergbau-Museum, also known as the Leibniz Research Museum for Georesources, is the world's largest mining museum. Founded in 1930 and based in Bochum, the museum is dedicated to collecting, preserving, investigating, exhibiting, and teaching the material heritage of the mining industry. The museum not only hosts permanent exhibits but also conducts its own research, data and artefact collection, and teaching by investing in the latest scientific innovations. A landmark project for the museum began in the 1980s when the oldest underground mine in Europe, dating back to 20,000 BC, was discovered on the Island of Thasos.
The Challenge
The Deutsches Bergbau-Museum, the world's largest mining museum, has been dedicated to the collection, preservation, investigation, exhibition, and teaching of the material heritage of the mining industry since 1930. A significant project for the museum began in the 1980s on the Island of Thasos, where the oldest underground mine in Europe, dating back to 20,000 BC, was discovered. However, the museum faced challenges in documenting its research due to the fragile nature of ancient mine sites and the need for unobtrusive technologies to create the models and drawings required for restoration. The process involved collecting two-dimensional and three-dimensional spatial data specifically designed for underground projects, using 2D-line-scanners and a photo camera to take thousands of images. The multiple data outputs gathered required an open technology platform to build digital replicas that could be trusted and used as the foundation of actual research activities.
The Solution
To overcome these challenges, the museum started using BricsCAD, a global design software provider, in 2021. This software supports the museum's continuous efforts to build better virtual models at Thasos and other mines worldwide. Gero Steffens at the Deutsches Bergbau-Museum stated that CAD software had been a crucial part of their documentation work for over 20 years, but finding the right partner had become increasingly difficult due to restrictive fee arrangements and proprietary platforms offered by industry incumbents. The museum chose BricsCAD for its ease of use, good reputation as a DWG-based alternative, and the fact that it allowed the museum to continue using all existing documentation created with the legacy system without any restrictions.
Operational Impact
Case Study missing?
Start adding your own!
Register with your work email and create a new case study profile for your business.
Related Case Studies.
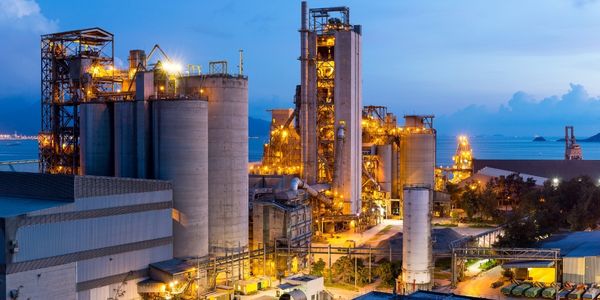
Case Study
System 800xA at Indian Cement Plants
Chettinad Cement recognized that further efficiencies could be achieved in its cement manufacturing process. It looked to investing in comprehensive operational and control technologies to manage and derive productivity and energy efficiency gains from the assets on Line 2, their second plant in India.
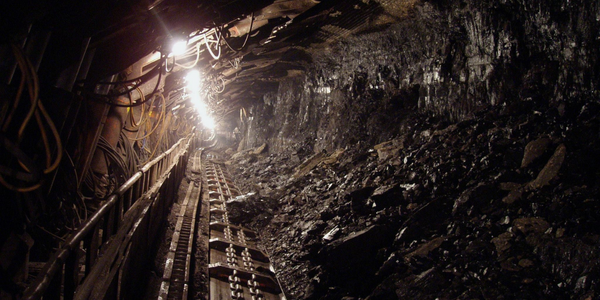
Case Study
Underground Mining Safety
The goal was to produce a safety system to monitor and support underground mining operations; existing systems were either too simple (i.e. phone line) or overly complex and expensive, inhibiting deployment, and providing little-to-no support in event of an accident. Given the dangerous nature of the mining work environment and the strict regulations placed on the industry, the solution would have to comply with Mine Safety and Health Administration (MSHA) regulations. Yet the product needed to allow for simple deployment to truly be a groundbreaking solution - increasing miner safety and changing daily operations for the better.
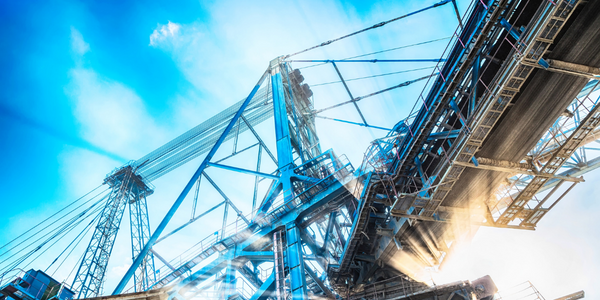
Case Study
Mining Firm Quadruples Production, with Internet of Everything
Dundee Precious Metal’s flagship mine, in Chelopech, Bulgaria, produces a gold, copper, and silver concentrate set a goal to increase production by 30%. Dundee wanted to increase production quality and output without increasing headcount and resources, improve miner safety, and minimize cost.
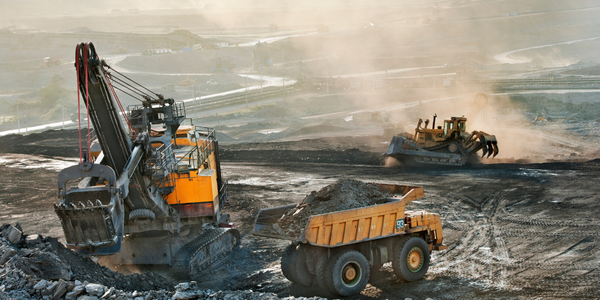
Case Study
Fastenal Builds the Future of Manufacturing with MachineMetrics
Fastenal's objective was to better understand their machine downtime, utilization, quality issues, and to embrace cutting-edge manufacturing technology/process improvement capabilities to bring their team to the next level. However, there was a lack of real-time data, visualization, and actionable insights made this transition impossible.
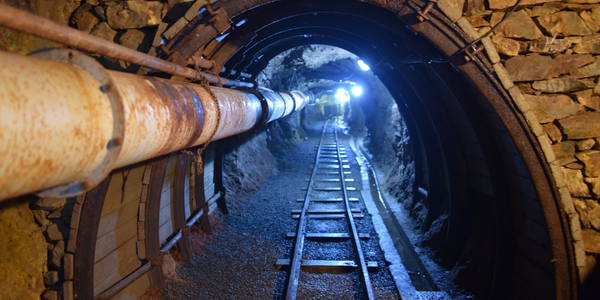
Case Study
Joy Mining Systems
Joy equipment faces many challenges. The first is machine integration and control. The business end of the machine has a rapidly-spinning cylinder with 6-inch diamond-studded cutting teeth. It chews through rock at rates measured in tens of tons per minute. The system grinds through the rock in front, creating a rectangular mine tunnel. Hydraulic lifters support the ceiling as the machine moves forward. Automated drills and screws drive 3-ft long screws into the ceiling to stabilize it. The rock and coal fall into a set of gathering "fingers" below the cutting cylinder. These fingers scoop up the rock and coal and deposit it onto a conveyor belt. The conveyor passes under the machine and out the back. A train of conveyor belt cars, up to a mile long, follows the cutter into the mine. The rock shoots along this train at over 400 feet per minute until it empties into rail cars at the end. Current systems place an operator cage next to the cutter. Choking dust (potentially explosive), the risk of collapse and the proximity of metal and rock mayhem make the operator cage a hazardous location.