Technology Category
- Application Infrastructure & Middleware - Middleware, SDKs & Libraries
- Sensors - GPS
Applicable Industries
- Automotive
- Electrical Grids
Applicable Functions
- Product Research & Development
- Sales & Marketing
Use Cases
- Leasing Finance Automation
- Material Handling Automation
Services
- Hardware Design & Engineering Services
- System Integration
About The Customer
Digital Design Corporation (DDC) is an engineering consulting company that offers high-end design services and products. The company specializes in video interfacing, enhancement, and recording, image processing, communications, DSP, and audio in a wide variety of military, automotive, medical, and other industrial markets. DDC architects, designs, and implements ICs (FPGAs, ASICs, etc.), associated circuits and software, and the systems that encompass them. The company has over 400 years of cumulative digital design experience, working the entire process from concept to foundry, including everything from initial architecture through complete design and verification, including the ability to provide prototype and/or production builds and support.
The Challenge
Digital Design Corporation (DDC) faced a complex challenge in designing a system capable of recording, processing, and analyzing video image data. The design requirements were demanding, including the need to withstand extreme temperatures and environments typical of military and rugged industrial applications. The system also had to cope with noisy power supplies, high G-forces, and vibration, all within a compact size. The design process required close collaboration among various disciplines, including system, schematic, board, mechanical, chip, firmware, and software design. The high frequencies involved in modern digital designs necessitated a broad experience base and high-powered tools. DDC's Video and Advanced Data Recorder (VAADR) was designed for military avionics applications, with most of its functionality residing on one controller board that interfaces with removable storage modules. The large sizes of the FPGAs used in the design presented a significant board design and layout challenge.
The Solution
DDC used Altium Designer to provide an integrated design environment for its hardware designers. This tool, with its comprehensive libraries, smart automation, and cross-discipline integration, allowed DDC to quickly balance all the design trade-offs within its most demanding products. Altium Designer's built-in component libraries made it easier to create schematics, even with the large Altera and Xilinx FPGAs that DDC depends on. Automation of data-intensive steps accelerated the design process and helped eliminate errors. The integration of schematics and board design also facilitated an efficient, error-free design cycle. Upon design completion, Altium Designer automatically generated the manufacturing output files. As the VAADR was tested, revised, and put through environmental testing, DDC made numerous revisions and improvements in the board using Altium Designer.
Operational Impact
Case Study missing?
Start adding your own!
Register with your work email and create a new case study profile for your business.
Related Case Studies.
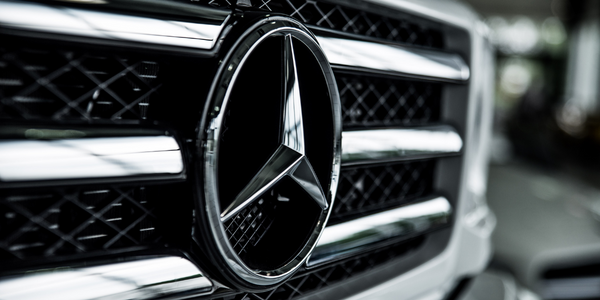
Case Study
Integral Plant Maintenance
Mercedes-Benz and his partner GAZ chose Siemens to be its maintenance partner at a new engine plant in Yaroslavl, Russia. The new plant offers a capacity to manufacture diesel engines for the Russian market, for locally produced Sprinter Classic. In addition to engines for the local market, the Yaroslavl plant will also produce spare parts. Mercedes-Benz Russia and his partner needed a service partner in order to ensure the operation of these lines in a maintenance partnership arrangement. The challenges included coordinating the entire maintenance management operation, in particular inspections, corrective and predictive maintenance activities, and the optimizing spare parts management. Siemens developed a customized maintenance solution that includes all electronic and mechanical maintenance activities (Integral Plant Maintenance).
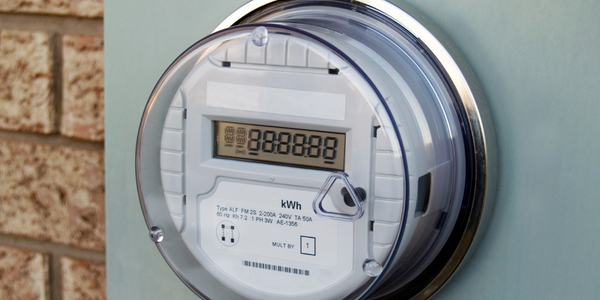
Case Study
Hydro One Leads the Way In Smart Meter Development
In 2010, Ontario’s energy board mandated that time-of-use (TOU) pricing for consumers be available for all consumers on a regulated price plan. To meet this requirement, Hydro One needed to quickly deploy a smart meter and intelligent communications network solution to meet the provincial government’s requirement at a low cost. The network needed to cover Hydro One’s expansive service territory, which has a land mass twice the size of Texas, and its customers live in a mix of urban, rural, and remote areas, some places only accessible by air, rail, boat or snowmobile. Most importantly, the network needed to enable future enterprise-wide business efficiencies, modernization of distribution infrastructure and enhanced customer service. To meet these needs, Hydro One conceptualized an end-to-end solution leveraging open standards and Internet Protocols (IP) at all communication levels. The utility drew upon industry leaders like Trilliant to realize this vision.
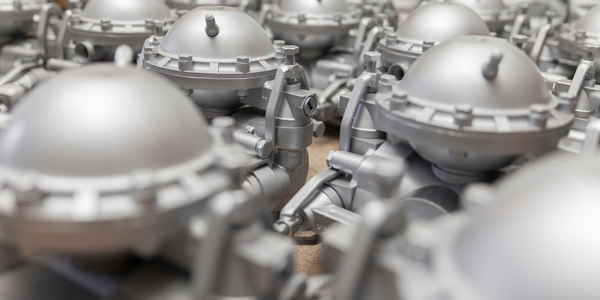
Case Study
Monitoring of Pressure Pumps in Automotive Industry
A large German/American producer of auto parts uses high-pressure pumps to deburr machined parts as a part of its production and quality check process. They decided to monitor these pumps to make sure they work properly and that they can see any indications leading to a potential failure before it affects their process.