Technology Category
- Platform as a Service (PaaS) - Application Development Platforms
- Sensors - Flow Meters
Applicable Industries
- Agriculture
- Transportation
Applicable Functions
- Logistics & Transportation
- Quality Assurance
Use Cases
- Farm Monitoring & Precision Farming
- Visual Quality Detection
Services
- System Integration
- Testing & Certification
About The Customer
Alquería is a leading dairy company in Colombia, specializing in the processing and commercialization of long-life dairy products. For 60 years, the company has been a key player in the Colombian Dairy industry, ranking among the top three companies in the sector. Alquería operates 11 collection centers, 3 plants, and over 2,500 production associations involving over 13,000 farms. The company is committed to constant evolution for business processes in its value chain, especially in critical processes such as supply and the optimization of fresh milk collection. To stay ahead of the market, Alquería has embraced digital transformation, using a Digital Business Platform to achieve real-time control of their operations.
The Challenge
Alquería, a leading dairy company in Colombia, faced significant challenges in managing its supply chain, particularly in the collection and processing of fresh milk. The company processes 1.2 million liters of fresh milk daily, involving numerous processes such as purchasing, milk collection, farm visits, and supply to production. The process of collecting raw milk involved many people who had to manually control the amount of milk collected on paper, which was subsequently consolidated into Excel sheets. This often generated delays that impacted decision making in the supply chain, milk quality analysis, freight payment, and application of discounts to farmers and transporters. The company needed a solution that could streamline these processes, improve efficiency, and provide real-time control of their operations.
The Solution
Alquería embarked on a digital transformation journey, implementing the AuraQuantic digital platform to achieve real-time control of their daily processing of fresh milk. The platform operates 24 hours a day, every day of the year, and impacts 100% of the industrial process. It controls the entry of more than one million liters of milk per day at a national level. All operators in each collection center use very efficient capture screens and integration with industrial devices, which give the company total control of the process. The platform drives hyper automation providing integration and interaction with other applications, including mobile applications for milk collection drivers, mechanical measurement systems for supply control, and corporate ERP functionalities to keep online inventory control. The system provides traceability back to the farm and even the exact silo of milk that is collected, as well as a detailed report of the milk losses and charges to each person.
Operational Impact
Quantitative Benefit
Case Study missing?
Start adding your own!
Register with your work email and create a new case study profile for your business.
Related Case Studies.
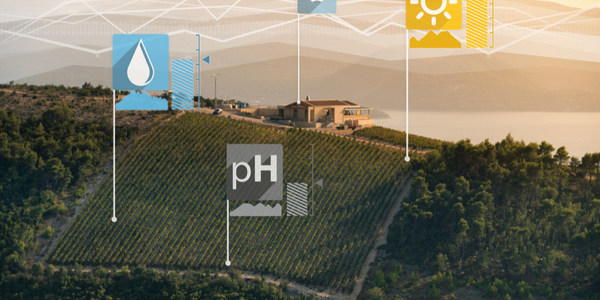
Case Study
Intelligent Farming with ThingWorx Analytics
Z Farms was facing three challenges: costly irrigation systems with water as a limited resource, narrow optimal ranges of soil moisture for growth with difficult maintenance and farm operators could not simply turn on irrigation systems like a faucet.
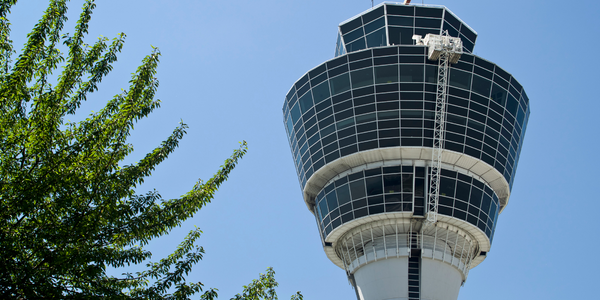
Case Study
Airport SCADA Systems Improve Service Levels
Modern airports are one of the busiest environments on Earth and rely on process automation equipment to ensure service operators achieve their KPIs. Increasingly airport SCADA systems are being used to control all aspects of the operation and associated facilities. This is because unplanned system downtime can cost dearly, both in terms of reduced revenues and the associated loss of customer satisfaction due to inevitable travel inconvenience and disruption.
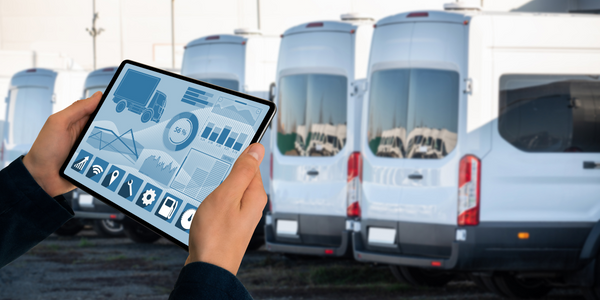
Case Study
IoT-based Fleet Intelligence Innovation
Speed to market is precious for DRVR, a rapidly growing start-up company. With a business model dependent on reliable mobile data, managers were spending their lives trying to negotiate data roaming deals with mobile network operators in different countries. And, even then, service quality was a constant concern.
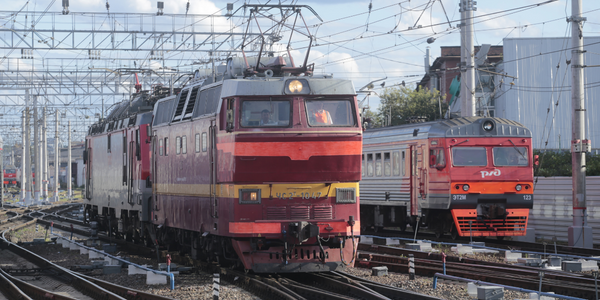
Case Study
Digitize Railway with Deutsche Bahn
To reduce maintenance costs and delay-causing failures for Deutsche Bahn. They need manual measurements by a position measurement system based on custom-made MEMS sensor clusters, which allow autonomous and continuous monitoring with wireless data transmission and long battery. They were looking for data pre-processing solution in the sensor and machine learning algorithms in the cloud so as to detect critical wear.