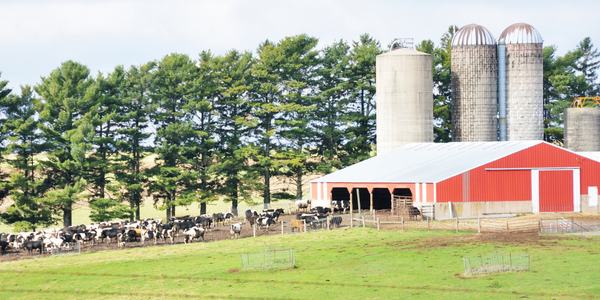
- Analytics & Modeling - Digital Twin / Simulation
- Food & Beverage
- Process Manufacturing
- Digital Twin
Leading global dairy producer
Manufacturers must cultivate the cheese like artisans but do so in enormous batches—thus the need for production know-how. Mass producing cheese requires machinery and elaborate processing plants that are difficult to manage. To better understand their operations, dairy companies are increasingly turning to data analytics.
Chemists and engineers at the dairy plant were running into bottlenecks, especially in terms of:
-The blend of protein and fat in the raw materials
-The temperature of the batches coming out of the upstream cookers
-The pH of output from the upstream fermentation process
Sight Machine’s experts designed a digital model of the dairy plant’s entire production process. They placed sensors on the machines and collected data on every aspect of the processing lines. The experts trained the model to analyze cooker and fermentation data, from which they could make recommendations for improving the lines. For instance, they determined optimal temperatures and release times for the fermenters; optimum speed and run times for the centrifuges used in the separation process; and accounted for daily production schedules and variations in the arrival of raw materials (milk and additives) to the plant.
Sight Machine was delighted to find that integrating process and batch data allowed the company to optimize production settings for its manufacturing process, both upstream and downstream. We maximized the quality and throughput of its production process—the mixing, blending, and packaging of cheese. Combining chemistry and statistics, we also calculated the optimal amount of water to add to the vats; the best time to clean the vats to avoid waste (of curds and water); and ways to decrease the dairy company’s energy use, thereby enhancing sustainability. Our models, moreover, interpreted data from raw materials, also derived from sensors, to forecast completion times for the vats of cheese.
Working with chemists at the plant, the data science team also designed a physics-based digital twin of the machinery that produces the cheese. The digital twin modelled essential information such as how milk acts inside the separator, how long it needs to ferment, and when to drain the tanks.
Case Study missing?
Start adding your own!
Register with your work email and create a new case study profile for your business.
Related Case Studies.

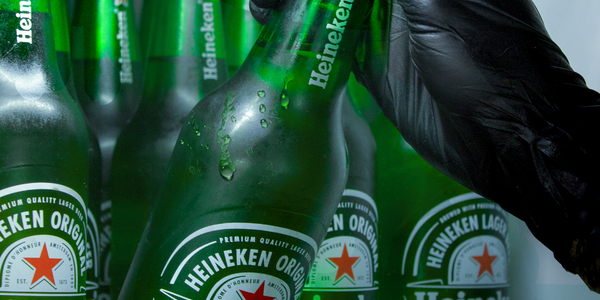
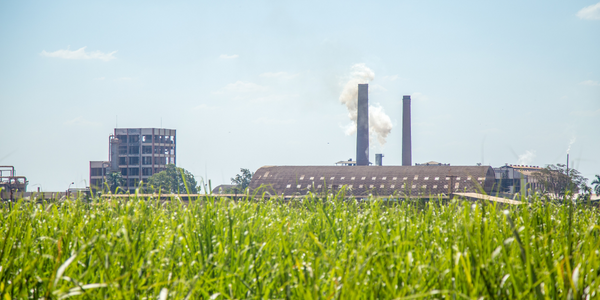
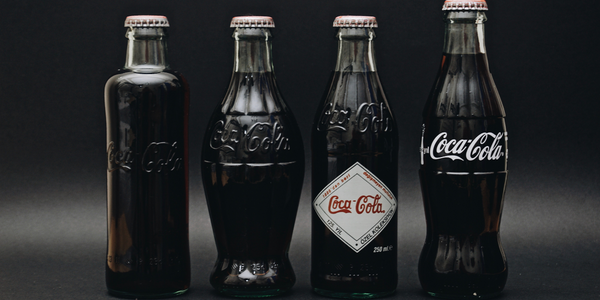
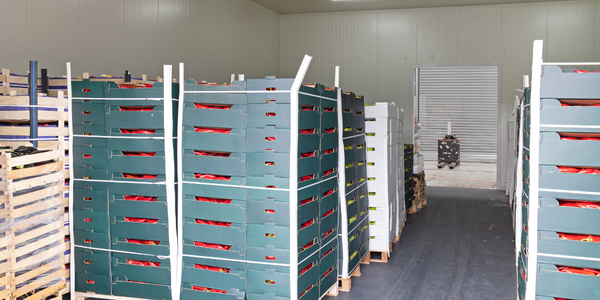
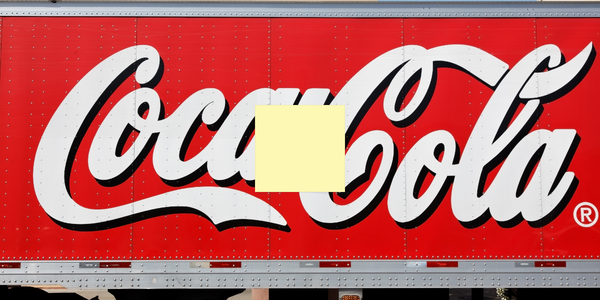