Customer Company Size
Large Corporate
Region
- Europe
Country
- Denmark
Product
- JDA Advanced Store Replenishment
- JDA Advanced Warehouse Replenishment
Tech Stack
- ERP system
Implementation Scale
- Enterprise-wide Deployment
Impact Metrics
- Customer Satisfaction
- Cost Savings
- Productivity Improvements
Technology Category
- Functional Applications - Inventory Management Systems
- Functional Applications - Warehouse Management Systems (WMS)
Applicable Industries
- Pharmaceuticals
Applicable Functions
- Warehouse & Inventory Management
- Logistics & Transportation
Use Cases
- Inventory Management
- Supply Chain Visibility
Services
- System Integration
About The Customer
Nomeco A/S is Denmark’s largest pharmaceutical wholesaler with a 70 percent market share. Specializing in health logistics, Nomeco is an international center of excellence for the Danish pharmaceutical industry and part of the wholly owned subsidiary of the Finnish company Tamro – the largest distributor of pharmaceuticals in Northern Europe, Poland and the Baltic countries. Nomeco has five distribution facilities that service more than 200 pharmacies throughout Denmark. Before selecting JDA, Nomeco was creating vendor orders weekly using its ERP system. These orders were based on historical data and the team’s best estimates of what its pharmacy clients’ needs would be.
The Challenge
Pharmaceutical suppliers and retailers in Denmark operate in a tremendously complex environment. Every two weeks suppliers must submit product pricing to the government without having any knowledge of how their competitors will price similar pharmaceutical products. The government then selects among bids for the lowest-priced prescription drug, which serves as the only one that it will fully reimburse for a given two-week period. After those two weeks, the process starts all over again. One company excelling in this highly competitive market is Nomeco A/S, Denmark’s largest pharmaceutical wholesaler with a 70 percent market share. Specializing in health logistics, Nomeco is an international center of excellence for the Danish pharmaceutical industry and part of the wholly owned subsidiary of the Finnish company Tamro – the largest distributor of pharmaceuticals in Northern Europe, Poland and the Baltic countries.
The Solution
To gain better insight and control over this challenging business environment, the company turned to JDA Advanced Warehouse Replenishment and JDA Advanced Store Replenishment software. These solutions enabled the wholesaler to implement an innovative VMI program that easily integrated into its existing ERP system, as well as all of its pharmacy customers’ systems. With JDA’s solutions in place, Nomeco is able to take the pricing-code information that the government provides one week before the pricing system changes, and enter that data into its ERP system. The wholesaler uses JDA Advanced Warehouse Replenishment to create purchase orders (POs) for products from its drug manufacturer vendors. JDA Advanced Store Replenishment provides real-time insight for both Nomeco and the company’s pharmacy customers involved in the wholesaler’s VMI initiative. Nomeco is also obtaining pharmacy inventory data that can then be synched with its ERP system, allowing the company to create more accurate POs.
Operational Impact
Quantitative Benefit
Case Study missing?
Start adding your own!
Register with your work email and create a new case study profile for your business.
Related Case Studies.
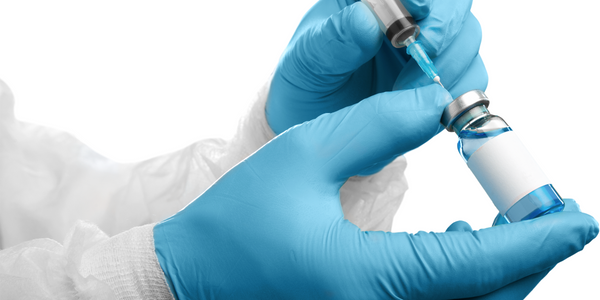
Case Study
Case Study: Pfizer
Pfizer’s high-performance computing software and systems for worldwide research and development support large-scale data analysis, research projects, clinical analytics, and modeling. Pfizer’s computing services are used across the spectrum of research and development efforts, from the deep biological understanding of disease to the design of safe, efficacious therapeutic agents.
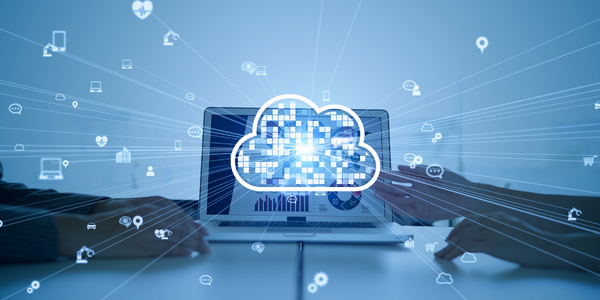
Case Study
Fusion Middleware Integration on Cloud for Pharma Major
Customer wanted a real-time, seamless, cloud based integration between the existing on premise and cloud based application using SOA technology on Oracle Fusion Middleware Platform, a Contingent Worker Solution to collect, track, manage and report information for on-boarding, maintenance and off-boarding of contingent workers using a streamlined and Integrated business process, and streamlining of integration to the back-end systems and multiple SaaS applications.
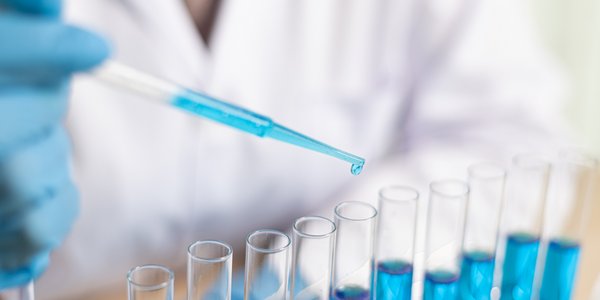
Case Study
Process Control System Support
In many automated production facilities, changes are made to SIMATIC PCS 7 projects on a daily basis, with individual processes often optimised by multiple workers due to shift changes. Documentation is key here, as this keeps workers informed about why a change was made. Furthermore, SIMATIC PCS 7 installations are generally used in locations where documentation is required for audits and certification. The ability to track changes between two software projects is not only an invaluable aid during shift changes, but also when searching for errors or optimising a PCS 7 installation. Every change made to the system is labour-intensive and time-consuming. Moreover, there is also the risk that errors may occur. If a change is saved in the project, then the old version is lost unless a backup copy was created in advance. If no backup was created, it will no longer be possible to return to the previous state if and when programming errors occur. Each backup denotes a version used by the SIMATIC PCS 7 system to operate an installation. To correctly interpret a version, information is required on WHO changed WHAT, WHERE, WHEN and WHY: - Who created the version/who is responsible for the version? - Who released the version? - What was changed in the version i.e. in which block or module of the SIMATIC PCS 7 installation were the changes made? - When was the version created? Is this the latest version or is there a more recent version? - Why were the changes made to the version? If they are part of a regular maintenance cycle, then is the aim to fix an error or to improve production processes? - Is this particular version also the version currently being used in production? The fact that SIMATIC PCS 7 projects use extremely large quantities of data complicates the situation even further, and it can take a long time to load and save information as a result. Without a sustainable strategy for operating a SIMATIC PCS 7 installation, searching for the right software version can become extremely time-consuming and the installation may run inefficiently as a result.
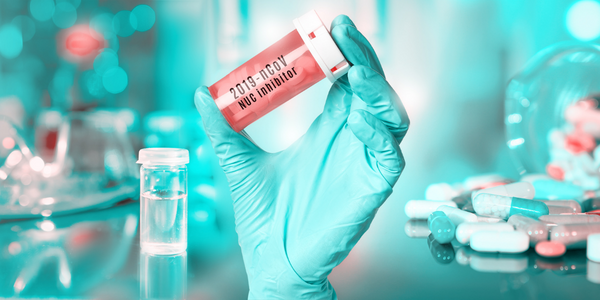
Case Study
ELI LILLY ADOPTS MICROMEDIA’S ALERT NOTIFICATION SYSTEM
Pharmaceutical production is subject to a strict set of enforced rules that must be adhered to and compliance to these standards is critically necessary. Due to the efforts of WIN 911’s strategic partner Micromedia, Lilly was able to adopt an alarm notification infrastructure that integrated smoothly with their existing workflows and emergency hardware and protocols. These raw energy sources enable the industrial process to function: electricity, WIN-911 Software | 4020 South Industrial Drive, Suite 120 | Austin, TX 78744 USA industrial steam, iced water, air mixtures of varying quality. Refrigeration towers, boilers and wastewater are monitored by ALERT. Eli Lilly identified 15000 potential variables, but limitations compelled them to chisel the variable list down to 300. This allowed all major alarms to be covered including pressure, discharge, quantity of waste water discharged,temperature, carbon dioxide content, oxygen & sulphur content, and the water’s pH.