Customer Company Size
Large Corporate
Region
- Africa
- Europe
- Middle East
Product
- JDA® Sales & Operations Planning
Implementation Scale
- Enterprise-wide Deployment
Impact Metrics
- Customer Satisfaction
- Productivity Improvements
Technology Category
- Functional Applications - Enterprise Resource Planning Systems (ERP)
Applicable Industries
- Automotive
Applicable Functions
- Business Operation
- Sales & Marketing
Use Cases
- Demand Planning & Forecasting
- Supply Chain Visibility
Services
- Cloud Planning, Design & Implementation Services
- Training
About The Customer
TE Connectivity (TE) is a global technology leader that designs and manufactures connectivity and sensor products for harsh environments in a variety of industries, such as automotive, industrial equipment, data communication systems, aerospace, defense, medical, oil and gas, consumer electronics and energy. TE has a large size with multiple business units and operates in a dynamic industry. It needed to define and support a new high-impact, demand-driven S&OP process across its production sites to guide the manufacture of components for passenger car wire harnesses, advanced automotive safety systems, highly integrated engine controls and advanced power management systems.
The Challenge
TE Connectivity (TE) needed to improve the sales and operations planning (S&OP) processes in each of its business units. The challenge was that every division was approaching this from a different perspective, and many, if not all, were simultaneously managing organizational, process or IT issues. While TE’s global IT organization supported all of the company’s business units, the company did not have a common S&OP platform or tool set, and business units were replicating information across multiple tools. TE needed an S&OP solution with the scalability to handle multiple business units and the ability to support flexible corporate hierarchies and various product coding, customer and other structures. Integration with current enterprise resource planning and other systems, as well as robust exception management capabilities, were also key requirements.
The Solution
TE decided to begin its corporate rollout of JDA Sales & Operations Planning, which is part of JDA’s Manufacturing Planning suite, with two business units: its Automotive business in the Europe, Middle East and Africa (EMEA) region and its Circuit Protection business from a global perspective. The TE Automotive EMEA pilot represented an end-to-end opportunity to develop a baseline framework from which to leverage subsequent TE business unit rollouts of JDA Sales & Operations Planning. TE Automotive competes in a dynamic industry, and it needed to define and support a new high-impact, demand-driven S&OP process across its production sites to guide the manufacture of components for passenger car wire harnesses, advanced automotive safety systems, highly integrated engine controls and advanced power management systems.
Operational Impact
Quantitative Benefit
Case Study missing?
Start adding your own!
Register with your work email and create a new case study profile for your business.
Related Case Studies.
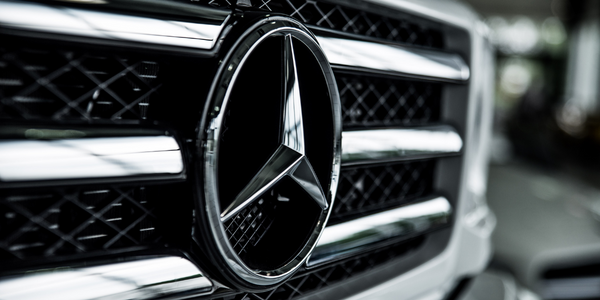
Case Study
Integral Plant Maintenance
Mercedes-Benz and his partner GAZ chose Siemens to be its maintenance partner at a new engine plant in Yaroslavl, Russia. The new plant offers a capacity to manufacture diesel engines for the Russian market, for locally produced Sprinter Classic. In addition to engines for the local market, the Yaroslavl plant will also produce spare parts. Mercedes-Benz Russia and his partner needed a service partner in order to ensure the operation of these lines in a maintenance partnership arrangement. The challenges included coordinating the entire maintenance management operation, in particular inspections, corrective and predictive maintenance activities, and the optimizing spare parts management. Siemens developed a customized maintenance solution that includes all electronic and mechanical maintenance activities (Integral Plant Maintenance).
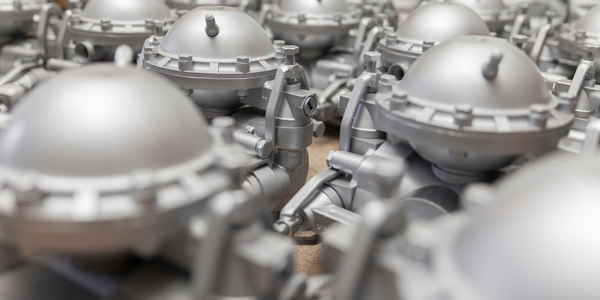
Case Study
Monitoring of Pressure Pumps in Automotive Industry
A large German/American producer of auto parts uses high-pressure pumps to deburr machined parts as a part of its production and quality check process. They decided to monitor these pumps to make sure they work properly and that they can see any indications leading to a potential failure before it affects their process.