Customer Company Size
Large Corporate
Region
- America
Country
- United States
Product
- Luminate™ Planning
Tech Stack
- Cloud
Implementation Scale
- Enterprise-wide Deployment
Impact Metrics
- Customer Satisfaction
- Cost Savings
Technology Category
- Platform as a Service (PaaS) - Data Management Platforms
Applicable Industries
- Automotive
Applicable Functions
- Logistics & Transportation
- Procurement
Use Cases
- Supply Chain Visibility
- Demand Planning & Forecasting
Services
- Cloud Planning, Design & Implementation Services
- Training
About The Customer
Mitsubishi Motors North America, Inc. (MMNA) is a part of the Mitsubishi Motors Corporation. It is responsible for the manufacturing, marketing, distribution, and financing of Mitsubishi motor vehicles in the United States. The company places a high emphasis on customer service and aims to ensure that the right part is delivered at the right time to meet its customers’ high service expectations. Supply chain plays a critical role in MMNA's operations, making sure that the necessary accessories and service parts are on hand to meet its customers’ needs.
The Challenge
Mitsubishi Motors North America, Inc. (MMNA) was facing challenges in achieving a high level of supply chain excellence. The company was focusing on three key performance indicators (KPIs) - customer service levels, on-hand inventory objectives, and forecast accuracy targets. However, MMNA’s old forecast module had only one algorithm that was applied to all parts, regardless of whether they were fast-moving or slow-moving parts. This approach was not effective in achieving their KPIs. The company found it difficult to perform analytics on their inventory business. They needed a forecasting tool that was flexible and could support the rigors and stock-keeping unit volumes of an automotive original equipment manufacturer.
The Solution
MMNA implemented Luminate™ Planning to improve its forecasting process. The new technology provided MMNA’s users with greater analytical capabilities, enabling them to analyze and identify trouble spots in the supply chain. It allowed them to dive deep into problem areas, tweak forecasts where needed, and resolve potential negative impacts to the company. The implementation also had a positive impact on MMNA’s New Part Introduction (NPI) process. When launching a new vehicle model into the marketplace, the company could ensure that they had enough material to support the new model launch and satisfy customer demand. The new capabilities were deployed via the Cloud in just three months, providing financial benefits as the company didn’t have to invest in hardware. In addition to the standard software training, MMNA worked with Blue Yonder’s education services to provide more in-depth forecast training for its users.
Operational Impact
Quantitative Benefit
Case Study missing?
Start adding your own!
Register with your work email and create a new case study profile for your business.
Related Case Studies.
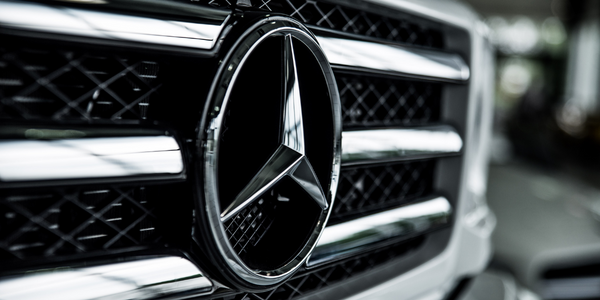
Case Study
Integral Plant Maintenance
Mercedes-Benz and his partner GAZ chose Siemens to be its maintenance partner at a new engine plant in Yaroslavl, Russia. The new plant offers a capacity to manufacture diesel engines for the Russian market, for locally produced Sprinter Classic. In addition to engines for the local market, the Yaroslavl plant will also produce spare parts. Mercedes-Benz Russia and his partner needed a service partner in order to ensure the operation of these lines in a maintenance partnership arrangement. The challenges included coordinating the entire maintenance management operation, in particular inspections, corrective and predictive maintenance activities, and the optimizing spare parts management. Siemens developed a customized maintenance solution that includes all electronic and mechanical maintenance activities (Integral Plant Maintenance).
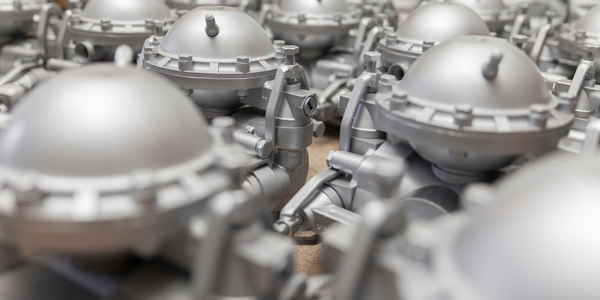
Case Study
Monitoring of Pressure Pumps in Automotive Industry
A large German/American producer of auto parts uses high-pressure pumps to deburr machined parts as a part of its production and quality check process. They decided to monitor these pumps to make sure they work properly and that they can see any indications leading to a potential failure before it affects their process.