Customer Company Size
Mid-size Company
Region
- America
Country
- United States
Product
- FORCAM FORCE
- FORCAM FORCE Bridge
- Smart Factory Starter Kit
Tech Stack
- Industrial IoT
- Data Analytics
- OpenAPI
- MTConnect
Implementation Scale
- Enterprise-wide Deployment
Impact Metrics
- Productivity Improvements
- Cost Savings
Technology Category
- Platform as a Service (PaaS) - Connectivity Platforms
- Analytics & Modeling - Real Time Analytics
Applicable Industries
- Aerospace
Applicable Functions
- Discrete Manufacturing
- Quality Assurance
Use Cases
- Predictive Maintenance
- Manufacturing System Automation
- Real-Time Location System (RTLS)
Services
- System Integration
- Cloud Planning, Design & Implementation Services
About The Customer
Dynomax is an engineering and manufacturing leader in the aerospace and defense industries with an unwavering commitment to get the job done right and deliver on time. Dynomax’ turnkey solutions provide customers with simplified logistics, reduced costs and superior quality components and sub-assemblies - from engineering support and prototypes, to custom-kitted, dock-to-stock solutions. Dynomax a certified or preferred supplier to major A&D companies, certifications include: ISO 9001:2015, AS9100 Rev D, and an ITAR registration. Products, Aerospace and Defense Applications include: Airframe Components and Assemblies, Automated Production Cells, Space Systems, Weaponry Components, Missile Structural Components. At Dynomax in Wheeling, Illionois Continuous Improvement efforts are a crucial factor in daily operations. As a Low-Volume/High-Mix product environment Dynomax’ production is co-located with engineering for the purpose to maintain quality and increase performance.
The Challenge
The global aerospace industry is experiencing rapid growth, with a focus on production efficiency for both commercial and military projects. Aerospace suppliers like Dynomax and other manufacturers in the supply chain understand that staying ahead of the competition and meeting the growing need for finished products requires leaner production through technological investment. Dynomax, an aggressively growing aerospace supplier, rises to the challenge of smarter production and proactively drives greater capacity, speed to market, and overall competitiveness. The team determined that the performance of machines needed to be measured in real time to quickly recognize and correct errors, reduce waste and continuously optimize productivity. Key challenges included the collection of OEE / KPIs, full production transparency, identification of bottlenecks, Epicor ERP integration, machine utilization, and reduction in machine downtime.
The Solution
Dynomax implemented the FORCAM Industrial IOT platform to measure machine utilization, performance, and output as a means to complement their Epicor ERP system. FORCAM delivers Industrial IoT for manufacturing by providing a unified approach for sustained manufacturing excellence across all operations on a single platform. The ready-configured IIoT solution, FORCAM FORCE, delivers the performance of a traditional MES combined with the added value of hi-tech IIoT. The heart of the engine, FORCAM FORCE Bridge, is so flexible that it collects data from machines of different manufacturers and year of manufacture - and makes it available to third-party systems via OpenAPI. Any ERP, PLM, CAQ, Tool Management, Predictive Maintenance or Artificial Intelligence (AI) now become an integral part of the holistic Industrial IoT solution. The Smart Factory Starter Kit guarantees productivity gains of at least 5 percent in 3 months. In the long run, shop floor management supported by FORCAM technology can increase productivity by more than 30 percent. CFOs confirm swift Return-On-Investment (ROI) with FORCAM in less than twelve months.
Operational Impact
Quantitative Benefit
Case Study missing?
Start adding your own!
Register with your work email and create a new case study profile for your business.
Related Case Studies.
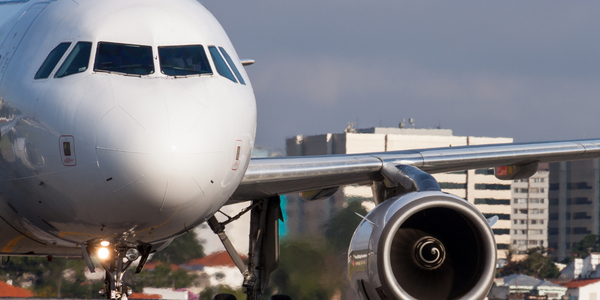
Case Study
Airbus Soars with Wearable Technology
Building an Airbus aircraft involves complex manufacturing processes consisting of thousands of moving parts. Speed and accuracy are critical to business and competitive advantage. Improvements in both would have high impact on Airbus’ bottom line. Airbus wanted to help operators reduce the complexity of assembling cabin seats and decrease the time required to complete this task.
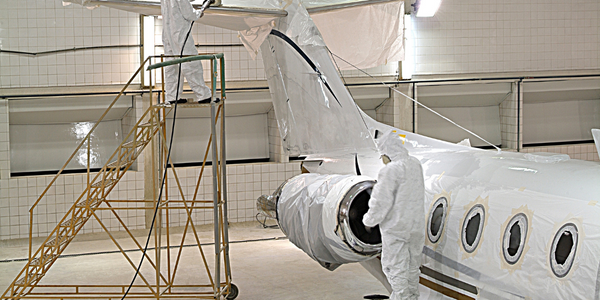
Case Study
Aircraft Predictive Maintenance and Workflow Optimization
First, aircraft manufacturer have trouble monitoring the health of aircraft systems with health prognostics and deliver predictive maintenance insights. Second, aircraft manufacturer wants a solution that can provide an in-context advisory and align job assignments to match technician experience and expertise.
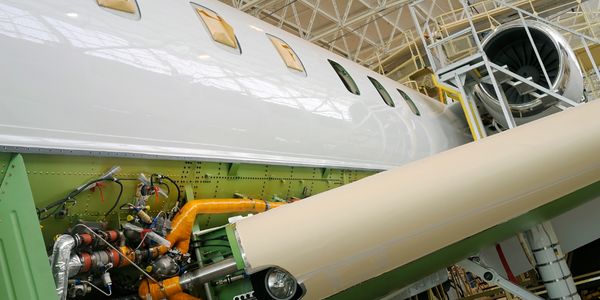
Case Study
Aerospace & Defense Case Study Airbus
For the development of its new wide-body aircraft, Airbus needed to ensure quality and consistency across all internal and external stakeholders. Airbus had many challenges including a very aggressive development schedule and the need to ramp up production quickly to satisfy their delivery commitments. The lack of communication extended design time and introduced errors that drove up costs.
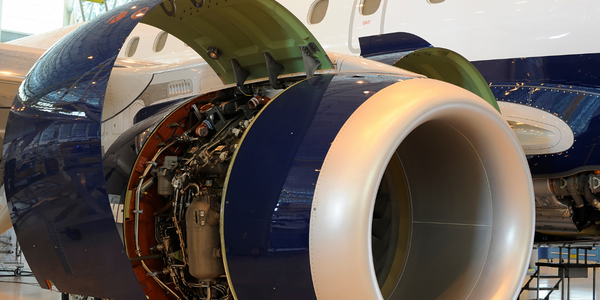
Case Study
Accelerate Production for Spirit AeroSystems
The manufacture and assembly of massive fuselage assemblies and other large structures generates a river of data. In fact, the bill of materials for a single fuselage alone can be millions of rows of data. In-house production processes and testing, as well as other manufacturers and customers created data flows that overwhelmed previous processes and information systems. Spirit’s customer base had grown substantially since their 2005 divestiture from Boeing, resulting in a $41 billion backlog of orders to fill. To address this backlog, meet increased customer demands and minimize additional capital investment, the company needed a way to improve throughput in the existing operational footprint. Spirit had a requirement from customers to increase fuselage production by 30%. To accomplish this goal, Spirit needed real-time information on its value chain and workflow. However, the two terabytes of data being pulled from their SAP ECC was unmanageable and overloaded their business warehouse. It had become time-consuming and difficult to pull aggregate data, disaggregate it for the needed information and then reassemble to create a report. During the 6-8 hours it took to build a report, another work shift (they run three per day) would have already taken place, thus the report content was out-of-date before it was ever delivered. As a result, supervisors often had to rely on manual efforts to provide charts, reports and analysis.
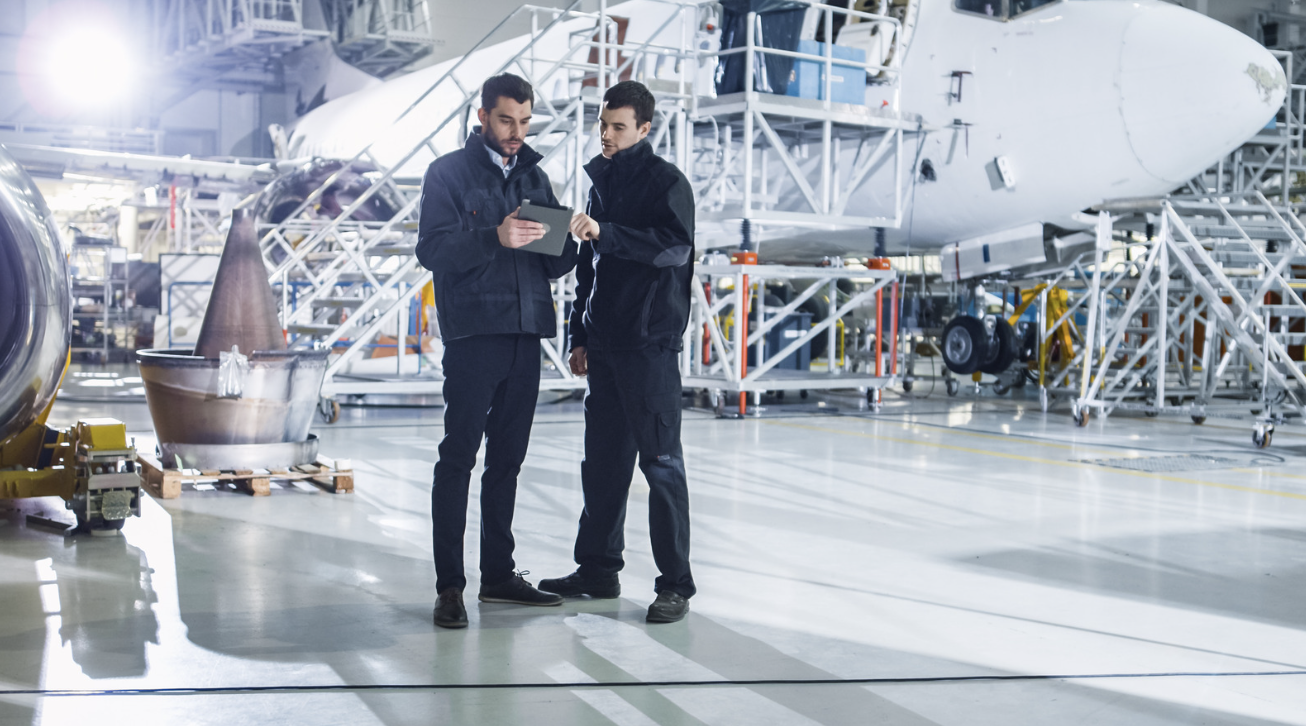
Case Study
Developing Smart Tools for the Airbus Factory
Manufacturing and assembly of aircraft, which involves tens of thousands of steps that must be followed by the operators, and a single mistake in the process could cost hundreds of thousands of dollars to fix, makes the room for error very small.