Technology Category
- Analytics & Modeling - Digital Twin / Simulation
- Robots - Autonomous Guided Vehicles (AGV)
Applicable Industries
- Automotive
- Education
Applicable Functions
- Product Research & Development
Use Cases
- Digital Twin
- Virtual Reality
About The Customer
Eco-Runner Team Delft is a student engineering team from TU Delft, a renowned technical university in the Netherlands. Since 2005, the team has been dedicated to designing and building the most efficient hydrogen-powered vehicle possible. They participate in the Shell Eco-marathon competition annually, a competition that challenges student teams around the world to design, build, and drive the most energy-efficient car. The team's mission is not only to win the competition but also to contribute to the development of sustainable mobility solutions. They are committed to pushing the boundaries of what's possible in vehicle efficiency, using innovative design and cutting-edge technology.
The Challenge
Eco-Runner Team Delft, a student engineering team at TU Delft, has been designing and building the most efficient hydrogen-powered vehicles since 2005. They participate in the Shell Eco-marathon competition annually, where the goal is to complete a 16-kilometer course using the least amount of fuel. The challenge lies in designing a vehicle with a fuel-efficient propulsion system and a body with minimal resistance or weight. The weight of the vehicle is particularly crucial to fuel efficiency, especially in the 2017 Eco-marathon course that featured a hill. The team's design efforts were focused on making every component of the car as light as possible to reduce the energy requirement to climb the hill. However, they faced the challenge of exploring and simulating many weight-saving design options while maintaining structural integrity, all within a constrained project schedule and a student budget.
The Solution
The team used Rescale’s ScaleX platform to explore and simulate many weight-saving design options while maintaining structural integrity. Rescale’s cloud-enabled simulation allowed them to quickly design a lightweight, but strong vehicle. They used ANSYS Mechanical for their FEA to reduce the weight of the car’s carbon fiber body. Using previous models of the Ecorunner as reference points, they ran FEA on various parts of the car to determine the lay-up plan of the carbon fiber and to determine whether each component would withstand the loads applied. Rescale’s cloud big compute platform provided turnkey access to compute resources, enabling them to get simulation results almost immediately. They ran the majority of their simulations on 192 cores of the Gold hardware configuration, which was the most cost-effective configuration for their simulations. The ability to scale out on unlimited cores on demand via the Rescale platform reduced their typical simulation turnaround time from a couple of days to a matter of hours.
Operational Impact
Quantitative Benefit
Case Study missing?
Start adding your own!
Register with your work email and create a new case study profile for your business.
Related Case Studies.
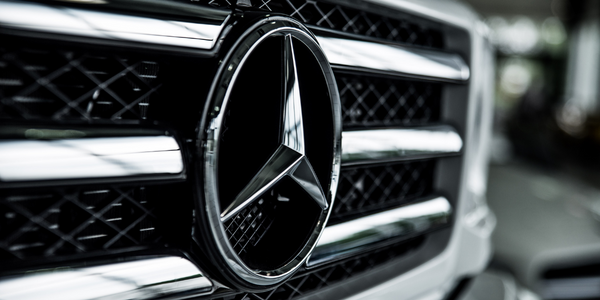
Case Study
Integral Plant Maintenance
Mercedes-Benz and his partner GAZ chose Siemens to be its maintenance partner at a new engine plant in Yaroslavl, Russia. The new plant offers a capacity to manufacture diesel engines for the Russian market, for locally produced Sprinter Classic. In addition to engines for the local market, the Yaroslavl plant will also produce spare parts. Mercedes-Benz Russia and his partner needed a service partner in order to ensure the operation of these lines in a maintenance partnership arrangement. The challenges included coordinating the entire maintenance management operation, in particular inspections, corrective and predictive maintenance activities, and the optimizing spare parts management. Siemens developed a customized maintenance solution that includes all electronic and mechanical maintenance activities (Integral Plant Maintenance).
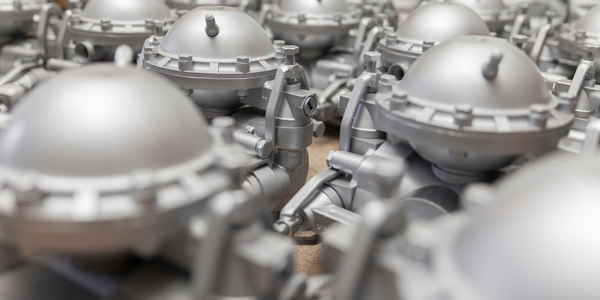
Case Study
Monitoring of Pressure Pumps in Automotive Industry
A large German/American producer of auto parts uses high-pressure pumps to deburr machined parts as a part of its production and quality check process. They decided to monitor these pumps to make sure they work properly and that they can see any indications leading to a potential failure before it affects their process.