Technology Category
- Application Infrastructure & Middleware - Database Management & Storage
- Infrastructure as a Service (IaaS) - Cloud Databases
Applicable Industries
- Aerospace
- Cement
Applicable Functions
- Logistics & Transportation
- Procurement
Use Cases
- Supply Chain Visibility
- Time Sensitive Networking
Services
- System Integration
- Training
About The Customer
Celestica is a Toronto-based company that specializes in design, manufacturing, engineering, and supply chain solutions. The company partners with brands in aerospace and defense, communications, enterprise, health tech, industrial, capital equipment, and smart energy to deliver solutions for their most complex technology challenges. With over 24,000 employees, Celestica is a global leader in its field. Despite being the brand behind many big-name brands, Celestica is not a household name, which has posed challenges in attracting talent for very niche engineering roles in a competitive market.
The Challenge
Celestica, a leader in design, manufacturing, engineering, and supply chain solutions, faced significant challenges in attracting talent for niche engineering roles. Despite being a key player behind many big-name brands, Celestica struggled with brand awareness, which affected their ability to attract applicants in a competitive market. The company needed a solution that would support automated follow-ups, help build their talent brand through outreach, and provide analytics to understand what was working and where they needed to optimize. The recruiters were caught up in daily urgencies, often sending off a single email and not having the time or resources to follow up. The company urgently needed a tool that would address their specific needs and not just offer generic features.
The Solution
Celestica found their solution in Gem, a tool that offered a consultative approach to their challenges. Gem mapped Celestica's process and provided data on how much time the team was spending on sourcing and outreach, and what was possible in terms of time-savings and efficiency. The tool integrated seamlessly with Celestica's Applicant Tracking System (ATS), SuccessFactors, and the onboarding process was smooth with minimal intervention from Celestica's HRIS team. Gem's impact was immediate, with the company filling positions that had been open for over a year within the first 30 days of using the tool. The tool also provided valuable data that gave Celestica's recruiting organization new visibility into their process, including diversity hiring efforts. Gem also positively impacted the hiring manager experience, increasing engagement and collaboration.
Operational Impact
Quantitative Benefit
Case Study missing?
Start adding your own!
Register with your work email and create a new case study profile for your business.
Related Case Studies.
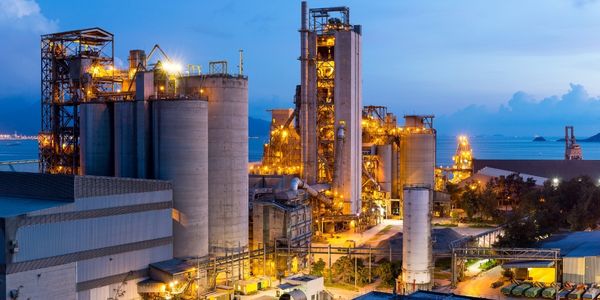
Case Study
System 800xA at Indian Cement Plants
Chettinad Cement recognized that further efficiencies could be achieved in its cement manufacturing process. It looked to investing in comprehensive operational and control technologies to manage and derive productivity and energy efficiency gains from the assets on Line 2, their second plant in India.
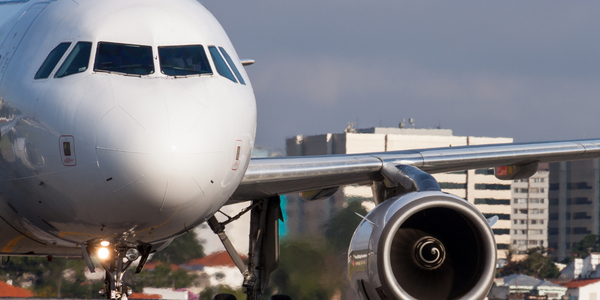
Case Study
Airbus Soars with Wearable Technology
Building an Airbus aircraft involves complex manufacturing processes consisting of thousands of moving parts. Speed and accuracy are critical to business and competitive advantage. Improvements in both would have high impact on Airbus’ bottom line. Airbus wanted to help operators reduce the complexity of assembling cabin seats and decrease the time required to complete this task.
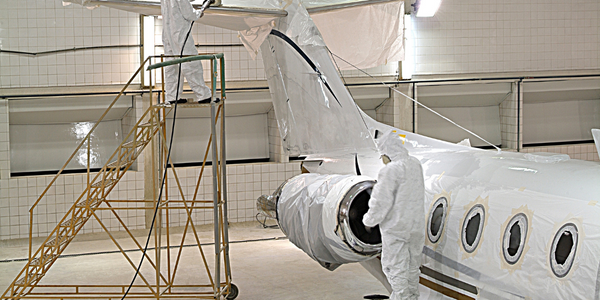
Case Study
Aircraft Predictive Maintenance and Workflow Optimization
First, aircraft manufacturer have trouble monitoring the health of aircraft systems with health prognostics and deliver predictive maintenance insights. Second, aircraft manufacturer wants a solution that can provide an in-context advisory and align job assignments to match technician experience and expertise.
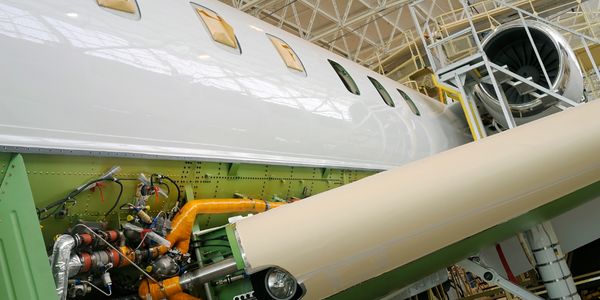
Case Study
Aerospace & Defense Case Study Airbus
For the development of its new wide-body aircraft, Airbus needed to ensure quality and consistency across all internal and external stakeholders. Airbus had many challenges including a very aggressive development schedule and the need to ramp up production quickly to satisfy their delivery commitments. The lack of communication extended design time and introduced errors that drove up costs.
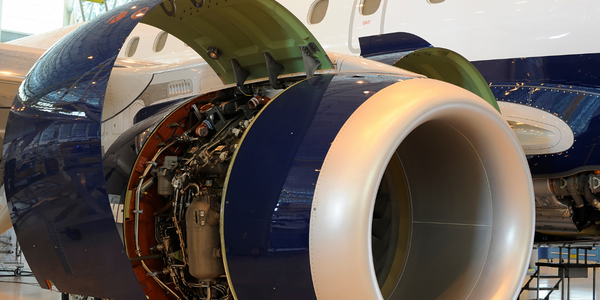
Case Study
Accelerate Production for Spirit AeroSystems
The manufacture and assembly of massive fuselage assemblies and other large structures generates a river of data. In fact, the bill of materials for a single fuselage alone can be millions of rows of data. In-house production processes and testing, as well as other manufacturers and customers created data flows that overwhelmed previous processes and information systems. Spirit’s customer base had grown substantially since their 2005 divestiture from Boeing, resulting in a $41 billion backlog of orders to fill. To address this backlog, meet increased customer demands and minimize additional capital investment, the company needed a way to improve throughput in the existing operational footprint. Spirit had a requirement from customers to increase fuselage production by 30%. To accomplish this goal, Spirit needed real-time information on its value chain and workflow. However, the two terabytes of data being pulled from their SAP ECC was unmanageable and overloaded their business warehouse. It had become time-consuming and difficult to pull aggregate data, disaggregate it for the needed information and then reassemble to create a report. During the 6-8 hours it took to build a report, another work shift (they run three per day) would have already taken place, thus the report content was out-of-date before it was ever delivered. As a result, supervisors often had to rely on manual efforts to provide charts, reports and analysis.