Technology Category
- Sensors - Haptic Sensors
- Sensors - Utility Meters
Applicable Industries
- Oil & Gas
Applicable Functions
- Product Research & Development
- Quality Assurance
Use Cases
- Additive Manufacturing
- Time Sensitive Networking
Services
- Training
About The Customer
The customers in this case study are global leaders in the manufacturing of pressure vessels and heat exchangers. They operate in the vessel manufacturing, industrial gas, petrochemical, and oil and gas industries. Their operations involve pressure vessels, heat exchangers, tanks, and air coolers. Their objective is to simplify vessel stress analysis and achieve optimized and compliant designs in the least amount of time. They have large production requirements and need to speed up the modeling and drawing process, as well as the calculation and cost estimation time for their plant vessels, while staying in compliance with international design standards and codes.
The Challenge
Global leaders in the manufacturing of pressure vessels and heat exchangers are faced with the challenge of meeting large production requirements. They need to accelerate the modeling and drawing process, as well as the calculation and cost estimation time for their plant vessels, while adhering to international design standards and codes. Additionally, they are required to reduce the time taken to bid for proposals generated for their clients. The challenge is to find a solution that increases design efficiency, saves engineering hours, and ensures confidence in vessel design while improving competitiveness through improved design quality.
The Solution
Many of these manufacturers have turned to Bentley’s AutoPIPE Vessel, a vessel design and analysis application, to meet their needs. The application is chosen for its reliability, speed, ease of use, optimization and calculation capabilities, and the ability to produce detailed drawing deliverables. AutoPIPE Vessel’s processing speed allows the design team to analyze more complex models in less time. Automated detailed drawings reduce manual drawing time and rework, delivering accurate and safe designs with fewer resource hours. The software supports numerous regional and global standards, including pressure vessel design codes and regional wind, seismic, wave, and blast loading codes. It also allows the use of new and older design codes, and material standards from any year, improving flexibility for re-rating and revamping of existing vessels. This helps to shorten design time and rework by eliminating guesswork, and reduces training time by providing a single, easy-to-use application for global projects.
Operational Impact
Quantitative Benefit
Case Study missing?
Start adding your own!
Register with your work email and create a new case study profile for your business.
Related Case Studies.
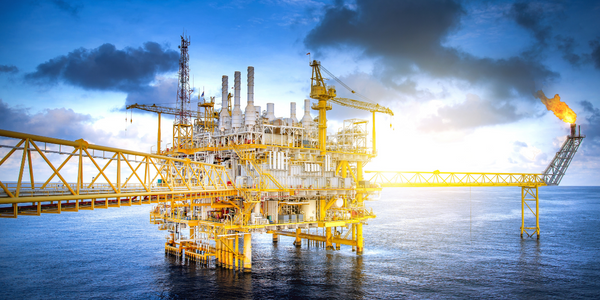
Case Study
Taking Oil and Gas Exploration to the Next Level
DownUnder GeoSolutions (DUG) wanted to increase computing performance by 5 to 10 times to improve seismic processing. The solution must build on current architecture software investments without sacrificing existing software and scale computing without scaling IT infrastructure costs.
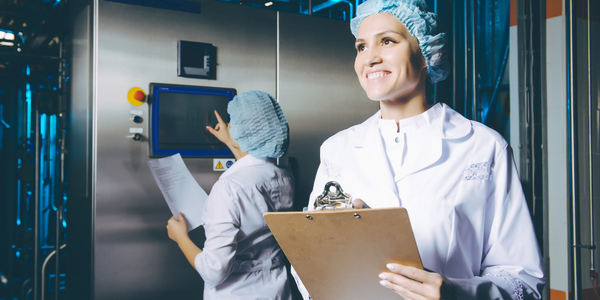
Case Study
Remote Wellhead Monitoring
Each wellhead was equipped with various sensors and meters that needed to be monitored and controlled from a central HMI, often miles away from the assets in the field. Redundant solar and wind generators were installed at each wellhead to support the electrical needs of the pumpstations, temperature meters, cameras, and cellular modules. In addition to asset management and remote control capabilities, data logging for remote surveillance and alarm notifications was a key demand from the customer. Terra Ferma’s solution needed to be power efficient, reliable, and capable of supporting high-bandwidth data-feeds. They needed a multi-link cellular connection to a central server that sustained reliable and redundant monitoring and control of flow meters, temperature sensors, power supply, and event-logging; including video and image files. This open-standard network needed to interface with the existing SCADA and proprietary network management software.
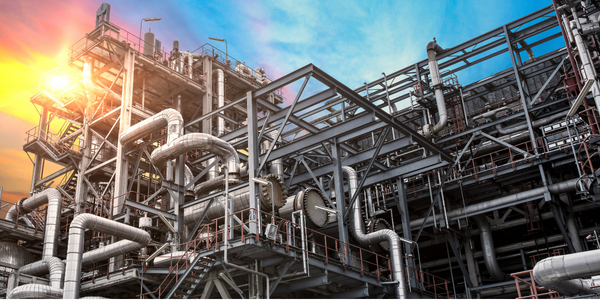
Case Study
Refinery Saves Over $700,000 with Smart Wireless
One of the largest petroleum refineries in the world is equipped to refine various types of crude oil and manufacture various grades of fuel from motor gasoline to Aviation Turbine Fuel. Due to wear and tear, eight hydrogen valves in each refinery were leaking, and each cost $1800 per ton of hydrogen vented. The plant also had leakage on nearly 30 flare control hydrocarbon valves. The refinery wanted a continuous, online monitoring system that could catch leaks early, minimize hydrogen and hydrocarbon production losses, and improve safety for maintenance.