Customer Company Size
Large Corporate
Region
- Africa
Product
- IsoMetrix EHS
- IsoMetrix Environmental Sustainability
- IsoMetrix Land Access and Resettlement
- IsoMetrix Social Engagement Management
Tech Stack
- Data Collection
- Data Analysis
- Data Visualization
- Multi-language Support
Implementation Scale
- Enterprise-wide Deployment
Impact Metrics
- Productivity Improvements
- Digital Expertise
Technology Category
- Analytics & Modeling - Data-as-a-Service
Applicable Industries
- Mining
Applicable Functions
- Discrete Manufacturing
- Quality Assurance
Use Cases
- Asset Health Management (AHM)
- Infrastructure Inspection
- Regulatory Compliance Monitoring
Services
- System Integration
- Training
About The Customer
Endeavour Mining is a multinational gold mining company operating predominantly in West Africa. One of the world’s top ten senior gold producers and the largest in West Africa, Endeavour Mining operates eight mines throughout Burkina Faso, Cote d’Ivoire (Ivory Coast) and Senegal. The company also has a portfolio of advanced development projects and exploration assets on the Birimian Greenstone Belt, across the region. Endeavour Mining has a workforce of 7000 employees and is listed on the London Stock Exchange (LSE) and Toronto Stock Exchange (TSX).
The Challenge
Endeavour Mining, a multinational gold mining company operating predominantly in West Africa, was facing difficulties collecting data from its various mining sites spread throughout West Africa. The existing data being collected was not sufficiently comprehensive nor was it being received timeously enough to satisfy the organization. It also did not suit its reporting purposes with regards to the increasingly important ESG measures and standards which are now typical throughout the industry. Furthermore, the company was saddled with an outdated EHS software system that did not offer the functionality and ease-of-use that Endeavour Mining desired. Finally, the organization needed a software package with multi-language support that catered for users with a primary language other than English.
The Solution
Endeavour Mining implemented IsoMetrix’s EHS solution, followed just a few months later by its Environmental Sustainability solution. This means that Endeavour Mining can now record detailed data pertaining to inspections, observations, incident management, audits and suggestions within its EHS solution and water, air, waste and noise measurements within its Environmental Sustainability solution. IsoMetrix’s software was praised by Endeavour Mining for its ease of use in making data available, and the way in which it lays out its system data in a series of user-friendly dashboards. As IsoMetrix is a roles-based system, data is available only to those who have authorized access. Endeavour Mining appreciates how managers can, utilizing the dashboards, see how their sites are doing across a range of measures, as well as where trends lie and if any issues have arisen, using real-time drilldowns.
Operational Impact
Case Study missing?
Start adding your own!
Register with your work email and create a new case study profile for your business.
Related Case Studies.
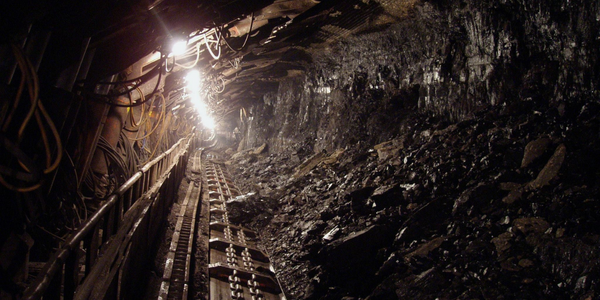
Case Study
Underground Mining Safety
The goal was to produce a safety system to monitor and support underground mining operations; existing systems were either too simple (i.e. phone line) or overly complex and expensive, inhibiting deployment, and providing little-to-no support in event of an accident. Given the dangerous nature of the mining work environment and the strict regulations placed on the industry, the solution would have to comply with Mine Safety and Health Administration (MSHA) regulations. Yet the product needed to allow for simple deployment to truly be a groundbreaking solution - increasing miner safety and changing daily operations for the better.
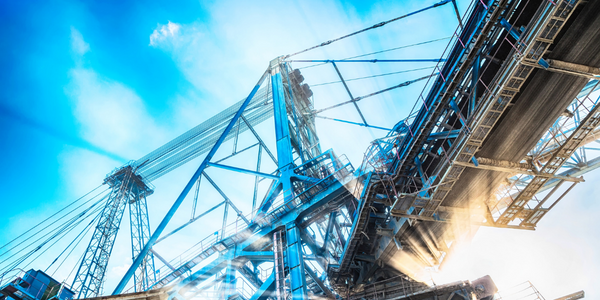
Case Study
Mining Firm Quadruples Production, with Internet of Everything
Dundee Precious Metal’s flagship mine, in Chelopech, Bulgaria, produces a gold, copper, and silver concentrate set a goal to increase production by 30%. Dundee wanted to increase production quality and output without increasing headcount and resources, improve miner safety, and minimize cost.
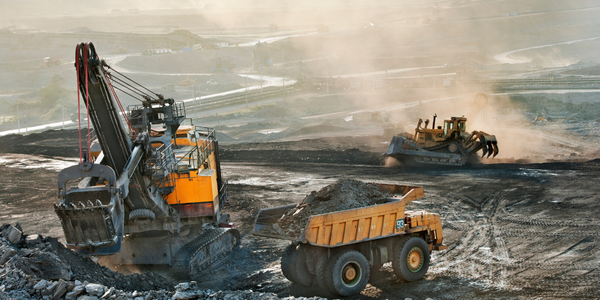
Case Study
Fastenal Builds the Future of Manufacturing with MachineMetrics
Fastenal's objective was to better understand their machine downtime, utilization, quality issues, and to embrace cutting-edge manufacturing technology/process improvement capabilities to bring their team to the next level. However, there was a lack of real-time data, visualization, and actionable insights made this transition impossible.
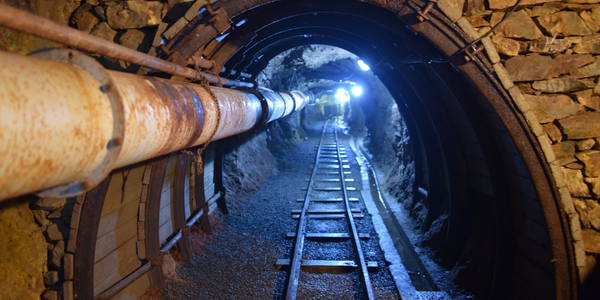
Case Study
Joy Mining Systems
Joy equipment faces many challenges. The first is machine integration and control. The business end of the machine has a rapidly-spinning cylinder with 6-inch diamond-studded cutting teeth. It chews through rock at rates measured in tens of tons per minute. The system grinds through the rock in front, creating a rectangular mine tunnel. Hydraulic lifters support the ceiling as the machine moves forward. Automated drills and screws drive 3-ft long screws into the ceiling to stabilize it. The rock and coal fall into a set of gathering "fingers" below the cutting cylinder. These fingers scoop up the rock and coal and deposit it onto a conveyor belt. The conveyor passes under the machine and out the back. A train of conveyor belt cars, up to a mile long, follows the cutter into the mine. The rock shoots along this train at over 400 feet per minute until it empties into rail cars at the end. Current systems place an operator cage next to the cutter. Choking dust (potentially explosive), the risk of collapse and the proximity of metal and rock mayhem make the operator cage a hazardous location.
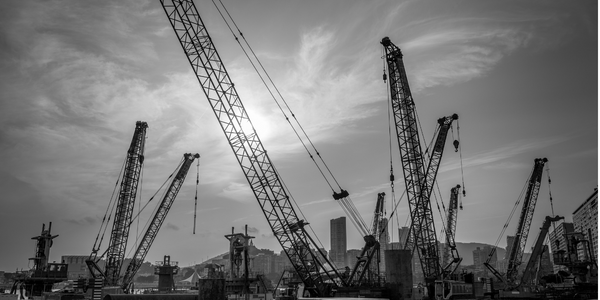
Case Study
Improved Monitoring in Industrial Manufacturing Facility
When your crane is moving tons of magma-hot iron, you can’t afford an unexpected failure. McWane Ductile knew monitoring the crane motor metrics within their facility could help prevent a mechanical failure that would strand an enormous bucket of molten metal overhead. Unfortunately, their legacy wired monitoring system couldn’t work with moving objects in this extreme environment. If they could integrate wireless capabilities into their existing equipment they could extend their monitoring capabilities without starting over from scratch.