Engineering Design Using a Small Autonomous Robot for Student Education at Aichi University Technology
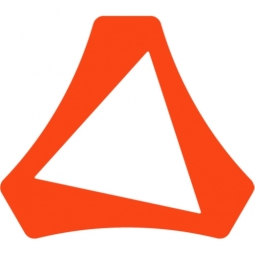
Technology Category
- Sensors - GPS
- Sensors - Haptic Sensors
Applicable Industries
- Construction & Infrastructure
- Education
Applicable Functions
- Product Research & Development
Use Cases
- Autonomous Robots
- Autonomous Transport Systems
Services
- Testing & Certification
About The Customer
Founded in 2000, Aichi University Technology (AUT) is an educational institution that focuses on providing comprehensive practical education for engineering design. As part of their educational approach, they have implemented various programs that allow students to acquire practical skills and knowledge. In 2017, they created an Internet of Things (IoT) special course for student engineers, recognizing the importance of IoT in future robot design. They also participate in events like A Rocket Launch for International Student Satellites (ARLISS) to provide their students with real-world design challenges.
The Challenge
The importance of practical education for industrial engineering has been gaining recognition globally. Aichi University Technology (AUT) in Japan has been implementing many effective educational programs for students to acquire practical skills and knowledge. Among these, robot designing is one of the most effective for engineering design. As part of this initiative, AUT participated in a demonstration test competition aiming for future Mars exploration - A Rocket Launch for International Student Satellites (ARLISS). The challenge was to design an autonomous robot that could be launched from a rocket, land safely, and then autonomously travel to a specified target. The design process involved the use of computer-aided tools (CAD, CAM, CAE) and the evaluation of the stress in the robot’s structure.
The Solution
The design process of the autonomous robot involved several steps. The basic design was based on a sketch drawing using imagination and original ideas. After the basic design was performed by sketches, the detailed design was decided by concrete dimensions and 3D imaging using a CAD system. The prototype parts were manufactured using CAM and a 3D printer. After assembling the prototype, the practical design process was produced through extraction of the problem and creation of the improvement from evaluation tests. The robot body was designed by “monocoque” structure of CFRP, and two wheels were made using the urethane sponge for the impact absorber. The material of the sponge wheels was selected by means of evaluation of the impact absorber at touchdown using an acceleration sensor. For the final designed robot, HyperWorks was used for structural analysis to understand whether or not the robot meets the requirements.
Operational Impact
Case Study missing?
Start adding your own!
Register with your work email and create a new case study profile for your business.
Related Case Studies.
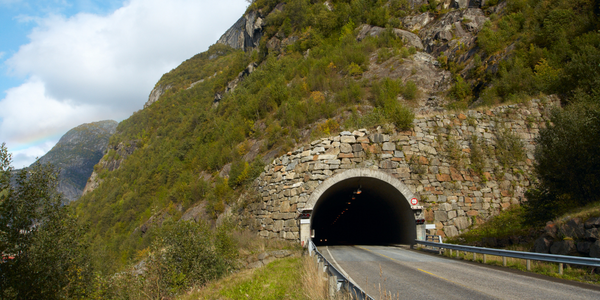
Case Study
IoT System for Tunnel Construction
The Zenitaka Corporation ('Zenitaka') has two major business areas: its architectural business focuses on structures such as government buildings, office buildings, and commercial facilities, while its civil engineering business is targeted at structures such as tunnels, bridges and dams. Within these areas, there presented two issues that have always persisted in regard to the construction of mountain tunnels. These issues are 'improving safety" and "reducing energy consumption". Mountain tunnels construction requires a massive amount of electricity. This is because there are many kinds of electrical equipment being used day and night, including construction machinery, construction lighting, and ventilating fan. Despite this, the amount of power consumption is generally not tightly managed. In many cases, the exact amount of power consumption is only ascertained when the bill from the power company becomes available. Sometimes, corporations install demand-monitoring equipment to help curb the maximum power demanded. However, even in these cases, the devices only allow the total volume of power consumption to be ascertained, or they may issue warnings to prevent the contracted volume of power from being exceeded. In order to tackle the issue of reducing power consumption, it was first necessary to obtain an accurate breakdown of how much power was being used in each particular area. In other words, we needed to be able to visualize the amount of power being consumed. Safety, was also not being managed very rigorously. Even now, tunnel construction sites often use a 'name label' system for managing entry into the work site. Specifically, red labels with white reverse sides that bear the workers' names on both sides are displayed at the tunnel work site entrance. The workers themselves then flip the name label to the appropriate side when entering or exiting from the work site to indicate whether or not they are working inside the tunnel at any given time. If a worker forgets to flip his or her name label when entering or exiting from the tunnel, management cannot be performed effectively. In order to tackle the challenges mentioned above, Zenitaka decided to build a system that could improve the safety of tunnel construction as well as reduce the amount of power consumed. In other words, this new system would facilitate a clear picture of which workers were working in each location at the mountain tunnel construction site, as well as which processes were being carried out at those respective locations at any given time. The system would maintain the safety of all workers while also carefully controlling the electrical equipment to reduce unnecessary power consumption. Having decided on the concept, our next concern was whether there existed any kind of robust hardware that would not break down at the construction work site, that could move freely in response to changes in the working environment, and that could accurately detect workers and vehicles using radio frequency identification (RFID). Given that this system would involve many components that were new to Zenitaka, we decided to enlist the cooperation of E.I.Sol Co., Ltd. ('E.I.Sol') as our joint development partner, as they had provided us with a highly practical proposal.
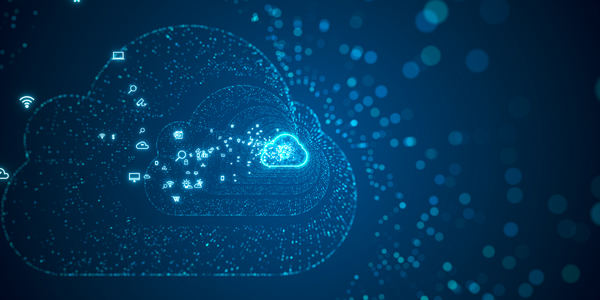
Case Study
Splunk Partnership Ties Together Big Data & IoT Services
Splunk was faced with the need to meet emerging customer demands for interfacing IoT projects to its suite of services. The company required an IoT partner that would be able to easily and quickly integrate with its Splunk Enterprise platform, rather than allocating development resources and time to building out an IoT interface and application platform.
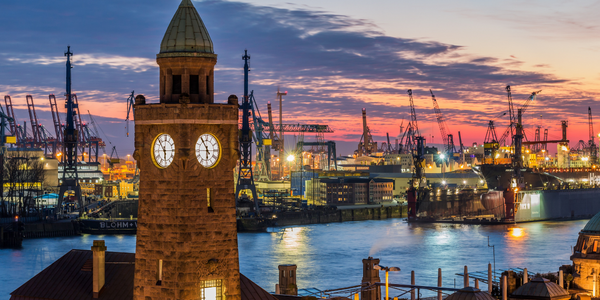
Case Study
Bridge monitoring in Hamburg Port
Kattwyk Bridge is used for both rail and road transport, and it has played an important role in the Port of Hamburg since 1973. However, the increasing pressure from traffic requires a monitoring solution. The goal of the project is to assess in real-time the bridge's status and dynamic responses to traffic and lift processes.
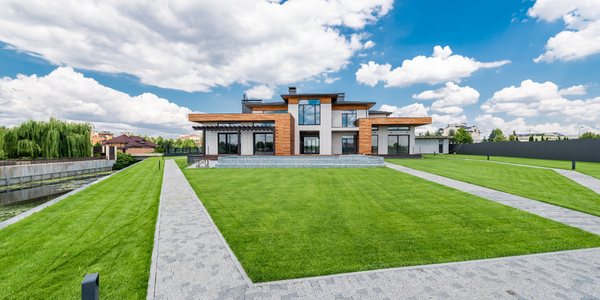
Case Study
Bellas Landscaping
Leading landscaping firm serving central Illinois streamlines operations with Samsara’s real-time fleet tracking solution: • 30+ vehicle fleet includes International Terrastar dump trucks and flatbeds, medium- and light-duty pickups from Ford and Chevrolet. Winter fleet includes of snow plows and salters.
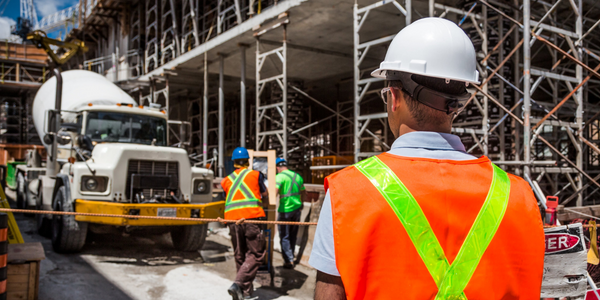
Case Study
Condition Based Monitoring for Industrial Systems
A large construction aggregate plant operates 10 high horsepower Secondary Crusher Drive Motors and associated conveyor belts, producing 600 tons of product per hour. All heavy equipment requires maintenance, but the aggregate producer’s costs were greatly magnified any time that the necessary maintenance was unplanned and unscheduled. The product must be supplied to the customers on a tight time schedule to fulfill contracts, avoid penalties, and prevent the loss of future business. Furthermore, a sudden failure in one of the drive motors would cause rock to pile up in unwanted locations, extending the downtime and increasing the costs.Clearly, preventative maintenance was preferable to unexpected failures. So, twice each year, the company brought in an outside vendor to attach sensors to the motors, do vibration studies, measure bearing temperatures and attempt to assess the health of the motors. But that wasn’t enough. Unexpected breakdowns continued to occur. The aggregate producer decided to upgrade to a Condition Based Monitoring (CBM) sensor system that could continually monitor the motors in real time, apply data analytics to detect changes in motor behavior before they developed into major problems, and alert maintenance staff via email or text, anywhere they happened to be.A wired sensor network would have been cost prohibitive. An aggregate plant has numerous heavy vehicles moving around, so any cabling would have to be protected. But the plant covers 400 acres, and the cable would have to be trenched to numerous locations. Cable wasn’t going to work. The aggregate producer needed a wireless solution.