Technology Category
- Sensors - Gas Sensors
- Sensors - Utility Meters
Applicable Industries
- Education
- Mining
Use Cases
- Onsite Human Safety Management
- Virtual Training
Services
- System Integration
- Training
About The Customer
OilStates Industries is a major global provider of integrated energy systems and solutions. The company provides the means for customers to build and operate high-performance offshore fields. They deliver reliable, cost-effective solutions to meet drilling and workover, production, lifting, and mooring challenges. With its headquarters in Aberdeen, UK, OilStates Industries operates across 25 international locations. The company is a significant player in the Mining, Oil, and Gas industry, offering a range of modules including Permit to Work, Incidents, Audits, Risk, Training, Contractors, Chemical & CoSHH, PPE, and Plant.
The Challenge
OilStates Industries, a major global provider of integrated energy systems and solutions, was facing a significant challenge in managing their safety data. The safety team was relying on paper and Excel spreadsheets to record their safety data, which was proving to be both inefficient and costly. The lack of a centralized solution meant that risk assessments, audits, checklists, training records, accident/incident reports, and plant records remained separate and scattered. This not only made it difficult to keep track of all the data but also posed a challenge in viewing training compliance for multiple sites. The paper-focused system was not conducive to the efficient management of safety data across the company's 25 international locations.
The Solution
OilStates Industries adopted the EcoOnline software system to address their safety data management challenges. The modules in the EcoOnline system are interconnected, allowing for shared data across the system. This means that if an incident occurs, the Health and Safety (H&S) team can quickly access relevant information such as the training the involved parties had, the risk assessments that were performed, and when a piece of plant had been inspected. The EcoOnline Training module provides the H&S team with a complete view of employee training throughout the entire organization. It keeps management informed of when training certificates are due to expire and whether a training course has been completed, thereby enhancing the efficiency and effectiveness of safety data management.
Operational Impact
Case Study missing?
Start adding your own!
Register with your work email and create a new case study profile for your business.
Related Case Studies.
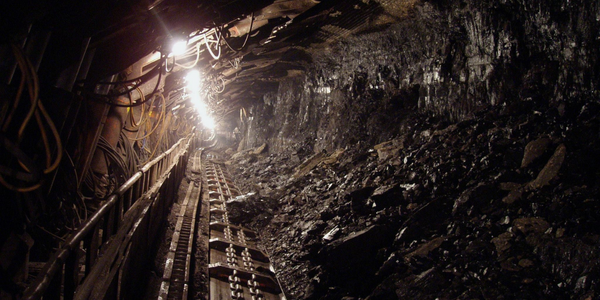
Case Study
Underground Mining Safety
The goal was to produce a safety system to monitor and support underground mining operations; existing systems were either too simple (i.e. phone line) or overly complex and expensive, inhibiting deployment, and providing little-to-no support in event of an accident. Given the dangerous nature of the mining work environment and the strict regulations placed on the industry, the solution would have to comply with Mine Safety and Health Administration (MSHA) regulations. Yet the product needed to allow for simple deployment to truly be a groundbreaking solution - increasing miner safety and changing daily operations for the better.
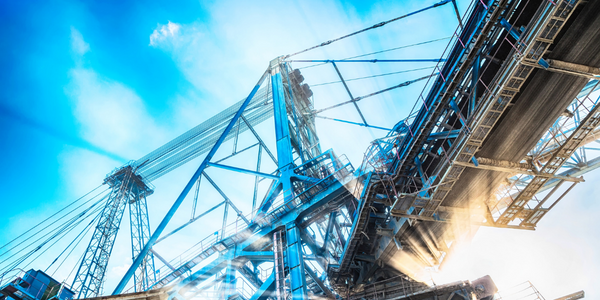
Case Study
Mining Firm Quadruples Production, with Internet of Everything
Dundee Precious Metal’s flagship mine, in Chelopech, Bulgaria, produces a gold, copper, and silver concentrate set a goal to increase production by 30%. Dundee wanted to increase production quality and output without increasing headcount and resources, improve miner safety, and minimize cost.
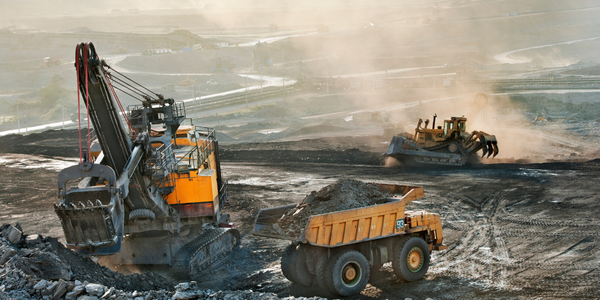
Case Study
Fastenal Builds the Future of Manufacturing with MachineMetrics
Fastenal's objective was to better understand their machine downtime, utilization, quality issues, and to embrace cutting-edge manufacturing technology/process improvement capabilities to bring their team to the next level. However, there was a lack of real-time data, visualization, and actionable insights made this transition impossible.
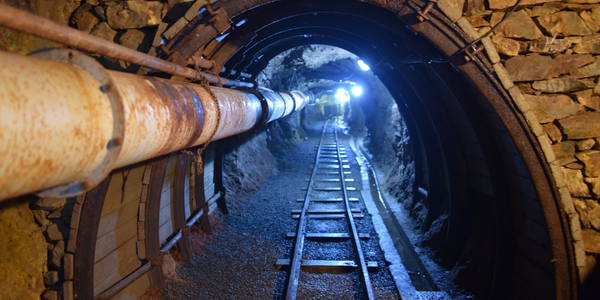
Case Study
Joy Mining Systems
Joy equipment faces many challenges. The first is machine integration and control. The business end of the machine has a rapidly-spinning cylinder with 6-inch diamond-studded cutting teeth. It chews through rock at rates measured in tens of tons per minute. The system grinds through the rock in front, creating a rectangular mine tunnel. Hydraulic lifters support the ceiling as the machine moves forward. Automated drills and screws drive 3-ft long screws into the ceiling to stabilize it. The rock and coal fall into a set of gathering "fingers" below the cutting cylinder. These fingers scoop up the rock and coal and deposit it onto a conveyor belt. The conveyor passes under the machine and out the back. A train of conveyor belt cars, up to a mile long, follows the cutter into the mine. The rock shoots along this train at over 400 feet per minute until it empties into rail cars at the end. Current systems place an operator cage next to the cutter. Choking dust (potentially explosive), the risk of collapse and the proximity of metal and rock mayhem make the operator cage a hazardous location.
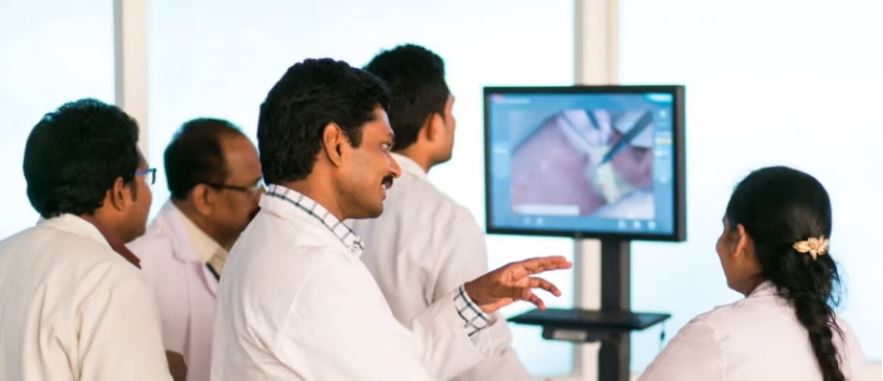
Case Study
Revolutionizing Medical Training in India: GSL Smart Lab and the LAP Mentor
The GSL SMART Lab, a collective effort of the GSL College of Medicine and the GSL College of Nursing and Health Science, was facing a challenge in providing superior training to healthcare professionals. As clinical medicine was becoming more focused on patient safety and quality of care, the need for medical simulation to bridge the educational gap between the classroom and the clinical environment was becoming increasingly apparent. Dr. Sandeep Ganni, the director of the GSL SMART Lab, envisioned a world-class surgical and medical training center where physicians and healthcare professionals could learn skills through simulation training. He was looking for different simulators for different specialties to provide both basic and advanced simulation training. For laparoscopic surgery, he was interested in a high fidelity simulator that could provide basic surgical and suturing skills training for international accreditation as well as specific hands-on training in complex laparoscopic procedures for practicing physicians in India.
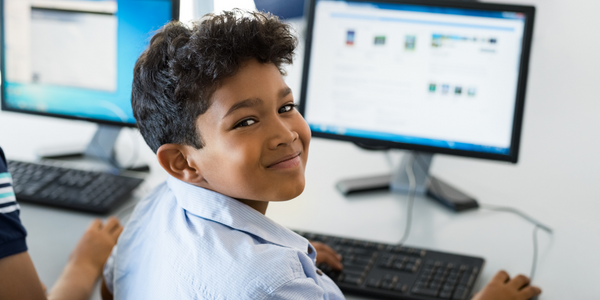
Case Study
IoT platform Enables Safety Solutions for U.S. School Districts
Designed to alert drivers when schoolchildren are present, especially in low-visibility conditions, school-zone flasher signals are typically updated manually at each school. The switching is based on the school calendar and manually changed when an unexpected early dismissal occurs, as in the case of a weather-event altering the normal schedule. The process to reprogram the flashers requires a significant effort by school district personnel to implement due to the large number of warning flashers installed across an entire school district.