Technology Category
- Functional Applications - Transportation Management Systems (TMS)
- Sensors - Utility Meters
Applicable Industries
- Chemicals
- Transportation
Applicable Functions
- Logistics & Transportation
- Warehouse & Inventory Management
Use Cases
- Traffic Monitoring
- Transportation Simulation
Services
- System Integration
About The Customer
Evonik Industries AG is one of the world’s leading specialty chemicals companies. The company's services unit, Evonik Technology & Infrastructure GmbH, is responsible for managing site operations, utilities, waste, technical services, and logistics. The Logistics department manages the complete supply chain, including the receipt of raw material, warehousing, and the shipping of finished products. In 2015 alone, the company transported 5,531,000 tons of hazardous goods by air, sea, rail, or road. The company is committed to the Responsible Care Initiative for the global chemistry industry and aspires to continuously improve and ensure the safety of all parties and supply chains involved.
The Challenge
Evonik Industries AG, a leading specialty chemicals company, has a critical need for risk management due to the nature of its operations. The company's services unit, Evonik Technology & Infrastructure GmbH, is responsible for managing site operations, utilities, waste, technical services, and logistics. The Logistics department manages the complete supply chain, including the receipt of raw material, warehousing, and the shipping of finished products. In 2015 alone, the company transported 5,531,000 tons of hazardous goods by air, sea, rail, or road. The company has its own transport risk analysis system, but it needed a more comprehensive solution to ensure the safety of all parties and supply chains involved. The transportation of hazardous goods needs to be well planned and monitored to minimize the impact of disturbances such as traffic jams or accidents on route. To keep risks under control, Evonik needed a full picture of the status of goods in transit and the ability to intervene with the best alternative solution if necessary.
The Solution
Evonik adopted Everstream Analytics, a cloud-based supply chain risk management platform, to improve transparency and responsiveness in its logistics processes. The solution complements the organization’s existing tools by supporting the evaluation of different transportation options and optimizing current risk monitoring procedures. It provides a way to visualize and evaluate vulnerabilities at every point in the supply chain, along with 24/7 near real-time monitoring of relevant incidents. The system assesses more than 35 different risk categories, from operational risks like customs delays to climate-related factors like blizzards and other severe weather events. Evonik has integrated all its relevant supply chain data into the Everstream Analytics platform. Using aggregated data from an extensive database of historical incidents, Everstream generates heat maps and visualizes the incident density and severity to highlight risk hotspots. Incident Monitoring also gives near real-time notifications should accidents, delays, strikes, or other disruptions arise.
Operational Impact
Quantitative Benefit
Case Study missing?
Start adding your own!
Register with your work email and create a new case study profile for your business.
Related Case Studies.
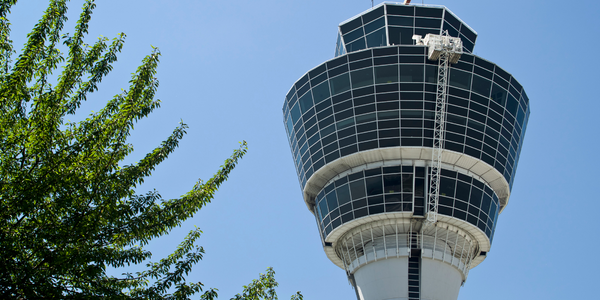
Case Study
Airport SCADA Systems Improve Service Levels
Modern airports are one of the busiest environments on Earth and rely on process automation equipment to ensure service operators achieve their KPIs. Increasingly airport SCADA systems are being used to control all aspects of the operation and associated facilities. This is because unplanned system downtime can cost dearly, both in terms of reduced revenues and the associated loss of customer satisfaction due to inevitable travel inconvenience and disruption.
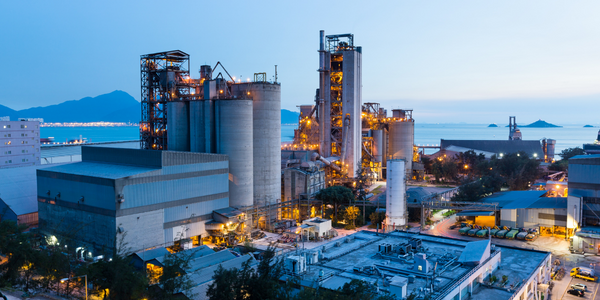
Case Study
Honeywell - Tata Chemicals Improves Data Accessibility with OneWireless
Tata was facing data accessibility challenges in the cement plant control room tapping signals from remote process control areas and other distant locations, including the gas scrubber. Tata needed a wireless solution to extend its control network securely to remote locations that would also provide seamless communication with existing control applications.
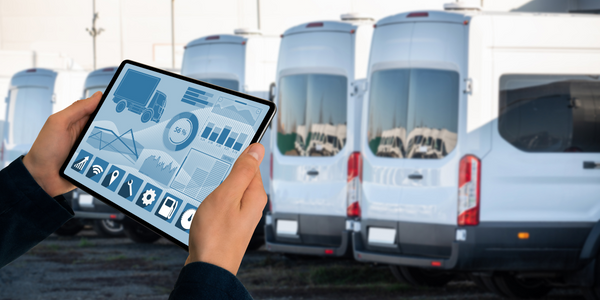
Case Study
IoT-based Fleet Intelligence Innovation
Speed to market is precious for DRVR, a rapidly growing start-up company. With a business model dependent on reliable mobile data, managers were spending their lives trying to negotiate data roaming deals with mobile network operators in different countries. And, even then, service quality was a constant concern.
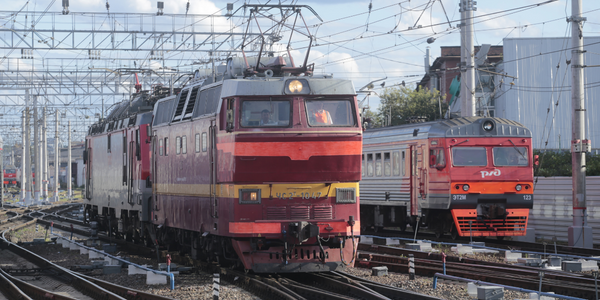
Case Study
Digitize Railway with Deutsche Bahn
To reduce maintenance costs and delay-causing failures for Deutsche Bahn. They need manual measurements by a position measurement system based on custom-made MEMS sensor clusters, which allow autonomous and continuous monitoring with wireless data transmission and long battery. They were looking for data pre-processing solution in the sensor and machine learning algorithms in the cloud so as to detect critical wear.
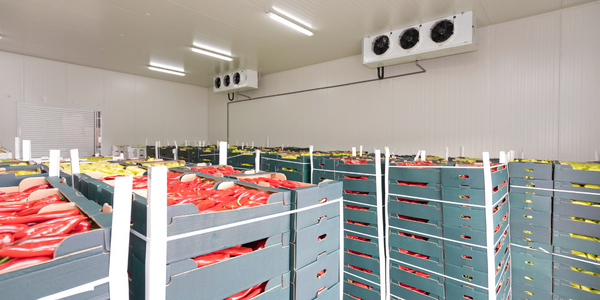
Case Study
Cold Chain Transportation and Refrigerated Fleet Management System
1) Create a digital connected transportation solution to retrofit cold chain trailers with real-time tracking and controls. 2) Prevent multi-million dollar losses due to theft or spoilage. 3) Deliver a digital chain-of-custody solution for door to door load monitoring and security. 4) Provide a trusted multi-fleet solution in a single application with granular data and access controls.

Case Study
Advanced Elastomer Systems Upgrades Production
In order to maintain its share of the international market for thermoplastic elastomers AES recently expanded its Florida plant by adding a new production line. While the existing lines were operating satisfactorily using a PROVOX distributed control system with traditional analog I/O, AES wanted advanced technology on the new line for greater economy, efficiency, and reliability. AES officials were anxious to get this line into production to meet incoming orders, but two hurricanes slowed construction.