Customer Company Size
SME
Region
- America
Country
- United States
Product
- Sage 100 ERP
- Sage 100 ERP Bill of Materials
- Sage 100 ERP Material Requirements Planning
- Sage 100 ERP Inventory Management
- Sage 100 ERP e-Business Manager
- Sage 100 ERP Business Alerts
Tech Stack
- ERP
- e-Business
- Business Alerts
Implementation Scale
- Enterprise-wide Deployment
Impact Metrics
- Productivity Improvements
- Customer Satisfaction
Technology Category
- Functional Applications - Enterprise Resource Planning Systems (ERP)
Applicable Functions
- Discrete Manufacturing
- Sales & Marketing
Use Cases
- Manufacturing System Automation
- Supply Chain Visibility
Services
- System Integration
About The Customer
Craftique is a high-end furniture manufacturing company based in Mebane, North Carolina. Unlike most of its competitors, Craftique adapts individual items to customers’ exact specifications. Customers order through high-end furniture stores, selecting details such as post, headboard, foot, and drawer pulls, and finish to fit their décor. While each product is unique, suite components are made simultaneously for greatest consistency and premium quality control. The company has one location and employs 95 people.
The Challenge
A change of management at Craftique in 1997 prompted a thorough operational audit. The existing business software was clearly inadequate, especially with major growth on the horizon. The firm’s CPAs recommended Sage 100 ERP, offered through an expert reseller. The reseller showed Craftique how it could start with basic accounting functions and then add on other financial and business modules as warranted in the future. It was a good thing that Craftique brought in Sage 100 ERP when it did. The company’s sales more than doubled in just three years, and having powerful business systems in place was crucial to success.
The Solution
Craftique implemented Sage 100 ERP, starting with basic accounting functions and then adding on other financial and business modules as warranted in the future. This included the Sage 100 ERP Bill of Materials, Material Requirements Planning, and Inventory Management modules—and more recently e-Business Manager and Business Alerts. The Sage 100 ERP system has given Craftique much greater control over its business. Reports on elapsed manufacturing time, inventory information, and delivery statistics have improved efficiency dramatically. Sage 100 ERP e-Business Manager has provided a welcome solution, allowing store representatives to check manufacturing and delivery status online whenever they like. Better service was also the main reason behind Craftique’s implementing the Sage 100 ERP Business Alerts module. No longer are territory sales representatives notified of orders by snail mail. Instead, information goes out automatically using email.
Operational Impact
Quantitative Benefit
Case Study missing?
Start adding your own!
Register with your work email and create a new case study profile for your business.
Related Case Studies.
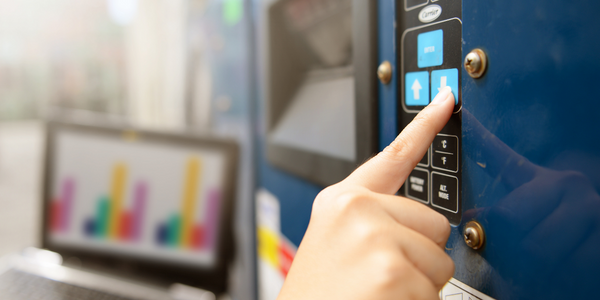
Case Study
Remote Temperature Monitoring of Perishable Goods Saves Money
RMONI was facing temperature monitoring challenges in a cold chain business. A cold chain must be established and maintained to ensure goods have been properly refrigerated during every step of the process, making temperature monitoring a critical business function. Manual registration practice can be very costly, labor intensive and prone to mistakes.
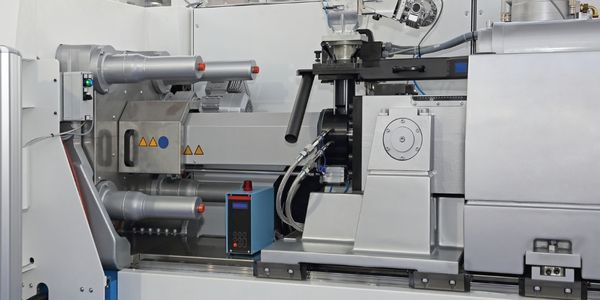
Case Study
Plastic Spoons Case study: Injection Moulding
In order to meet customer expectations by supplying a wide variety of packaging units, from 36 to 1000 spoons per package, a new production and packaging line needed to be built. DeSter wanted to achieve higher production capacity, lower cycle time and a high degree of operator friendliness with this new production line.
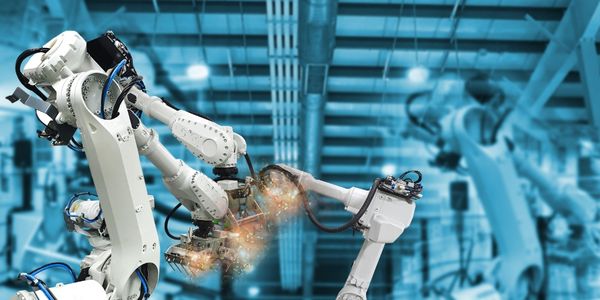
Case Study
Robot Saves Money and Time for US Custom Molding Company
Injection Technology (Itech) is a custom molder for a variety of clients that require precision plastic parts for such products as electric meter covers, dental appliance cases and spools. With 95 employees operating 23 molding machines in a 30,000 square foot plant, Itech wanted to reduce man hours and increase efficiency.
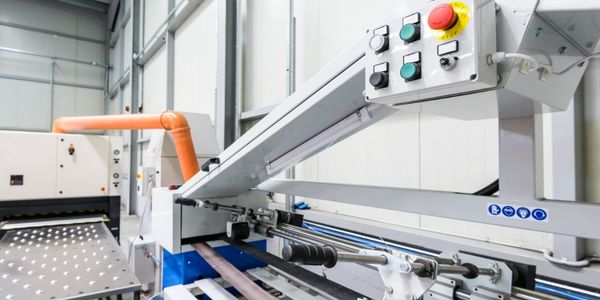
Case Study
Fully Automated Visual Inspection System
Tofflon has developed a fully automatic machine that uses light to inspect vials, medicine bottles, or infusion containers for glass fragments, aluminum particles, rubber grains, hairs, fibers, or other contaminants. It also detects damaged containers with cracks or inclusions (microscopic imperfections), automatically removing faulty or contaminated products. In order to cover all production processes for freeze-dried pharmaceuticals, Tofflon needed to create an open, consistent, and module-based automation concept.
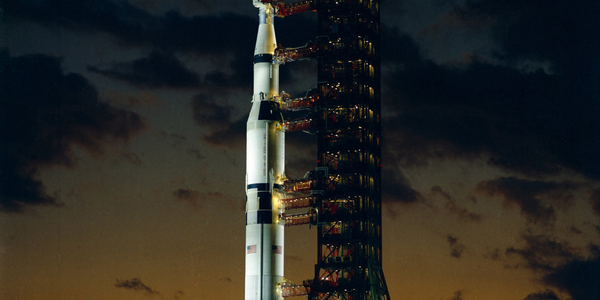
Case Study
SAP Leonardo Enabling Rocket Science
At times, ULA has as many as 15 different operating systems dedicated to overlapping processes, such as rocket design, testing, and launch. Multiple systems created unnecessary costs and unwanted confusion among workers at offices, factories, and launch sites in different location. In order to improve collaboration and transparency during vital activities that directly influence mission success, ULA wanted to improve data sharing and streamline manufacturing processes.