Customer Company Size
Large Corporate
Region
- America
Country
- United States
Product
- Blue Yonder’s slow mover forecasting & replenishment capability
- Blue Yonder forecasting and replenishment solutions
Tech Stack
- Luminate Planning platform
Implementation Scale
- Enterprise-wide Deployment
Impact Metrics
- Cost Savings
- Productivity Improvements
- Customer Satisfaction
Technology Category
- Analytics & Modeling - Predictive Analytics
- Functional Applications - Inventory Management Systems
Applicable Industries
- Automotive
Applicable Functions
- Logistics & Transportation
- Warehouse & Inventory Management
Use Cases
- Predictive Maintenance
- Inventory Management
Services
- System Integration
About The Customer
FleetPride is the largest independent distributor of aftermarket heavy-duty truck and trailer parts in the United States. The company operates a network of five regional distribution centers and 260 branch locations across 45 states. To provide a superior level of service, FleetPride has localized assortments across their network to ensure that customers get what they need, when and where they need it. However, the company was struggling with managing its inventory, particularly slow-moving items that sell less than one unit per month, which accounted for 70% of their inventory.
The Challenge
FleetPride, the largest independent distributor of aftermarket heavy-duty truck and trailer parts in the United States, was facing a significant challenge with its inventory management. Approximately 70% of their inventory, which includes a wide variety of items from small nuts and washers to transmissions and axles, sells less than one unit per month. This resulted in a high level of excess and obsolete (E&O) inventory, particularly at the local branch level. Traditional forecasting methods were not effective for these slow-moving items, as they often represented forecasts as a fraction, creating a misleading picture of demand. FleetPride was using work-arounds to support their slow mover business needs because purpose-built slow mover solutions were not previously available.
The Solution
To address this challenge, FleetPride implemented Blue Yonder’s slow mover forecasting & replenishment capability within the Blue Yonder forecasting and replenishment solutions it had already deployed. The solution uses detailed store SKU history and sophisticated algorithms to create realistic supply chain plans for slow movers. This allows retailers and suppliers to better understand what inventory should be purchased, ensuring that all on-hand inventory at the branch is considered. The system gave FleetPride better visibility to all items, allowing them to order more effectively and decrease fast mover inventory. For medium-moving SKUs, the system reduced inventory levels as expected. Interestingly, better visibility to demand actually led them to increase inventory at some branches while decreasing inventory at others in order to provide higher services levels to all of its customers.
Operational Impact
Quantitative Benefit
Case Study missing?
Start adding your own!
Register with your work email and create a new case study profile for your business.
Related Case Studies.
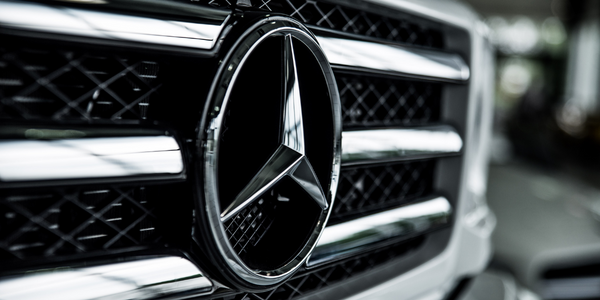
Case Study
Integral Plant Maintenance
Mercedes-Benz and his partner GAZ chose Siemens to be its maintenance partner at a new engine plant in Yaroslavl, Russia. The new plant offers a capacity to manufacture diesel engines for the Russian market, for locally produced Sprinter Classic. In addition to engines for the local market, the Yaroslavl plant will also produce spare parts. Mercedes-Benz Russia and his partner needed a service partner in order to ensure the operation of these lines in a maintenance partnership arrangement. The challenges included coordinating the entire maintenance management operation, in particular inspections, corrective and predictive maintenance activities, and the optimizing spare parts management. Siemens developed a customized maintenance solution that includes all electronic and mechanical maintenance activities (Integral Plant Maintenance).
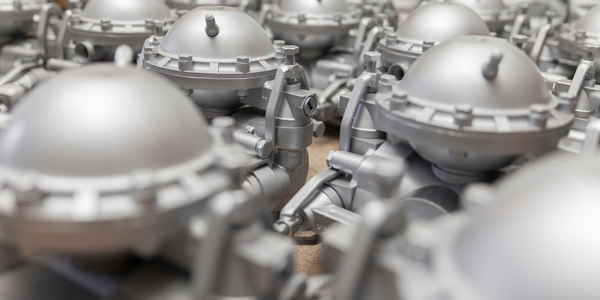
Case Study
Monitoring of Pressure Pumps in Automotive Industry
A large German/American producer of auto parts uses high-pressure pumps to deburr machined parts as a part of its production and quality check process. They decided to monitor these pumps to make sure they work properly and that they can see any indications leading to a potential failure before it affects their process.