Customer Company Size
Large Corporate
Region
- America
- Asia
- Europe
Country
- United States
Product
- SAP Supplier Relationship Management
- SAP Spend Performance Management
- SAP SRM-MDM Catalog
- Ariba Contract Management
- Ariba eSourcing
Tech Stack
- SAP ERP
- SAP ERP Human Capital Management
Implementation Scale
- Enterprise-wide Deployment
Impact Metrics
- Cost Savings
- Productivity Improvements
Technology Category
- Application Infrastructure & Middleware - Data Exchange & Integration
- Functional Applications - Enterprise Resource Planning Systems (ERP)
Applicable Industries
- Chemicals
Applicable Functions
- Procurement
Use Cases
- Supply Chain Visibility
- Demand Planning & Forecasting
Services
- System Integration
- Software Design & Engineering Services
About The Customer
FMC Corporation is a specialty chemicals manufacturing company headquartered in Philadelphia, Pennsylvania. The company operates its businesses in three segments: FMC Agricultural Solutions, FMC Health and Nutrition, and FMC Minerals. FMC serves customers through a network of business units within each of its geographic regions. This approach has served the company well for marketing, sales and product development, combining global scale with local knowledge and flexibility. However, the business model also led to decentralized processes around indirect procurement – the sourcing of goods and services for use by internal stakeholders – which dulled visibility and operational efficiency.
The Challenge
FMC Corporation, a specialty chemicals manufacturing company, was facing challenges with its indirect procurement processes. The company's decentralized approach to procurement across its global business units made it difficult to manage and control how employees purchased goods and services. This lack of visibility and operational efficiency prevented FMC from leveraging its global scale to negotiate better deals with suppliers, and made it difficult for the company to understand and manage total procurement spend effectively. The company needed a solution that would allow it to take control over global sourcing and spending, and manage global procurement more efficiently through standardized, automated processes.
The Solution
FMC worked with IBM Global Business Services to implement a standardized source-to-pay process, built on SAP solutions, unifying the way employees in various locations procure supplies and services. The company created a center-led organization that would act as a hub for global sourcing and procurement. With the new organization in place, attention turned to introducing a standardized, scalable platform for managing the entire source-to-pay process, through the eProcure project. The new platform would allow FMC to manage global procurement more efficiently through standardized, automated processes. Additionally, the solution would drive greater spend visibility by offering a single picture of actual purchasing behavior, prices and suppliers across all FMC business units and regions. FMC took a phased approach to the implementation, working with IBM Global Business Services and other partners to roll out the source-to-pay system on a region-by-region basis.
Operational Impact
Quantitative Benefit
Case Study missing?
Start adding your own!
Register with your work email and create a new case study profile for your business.
Related Case Studies.
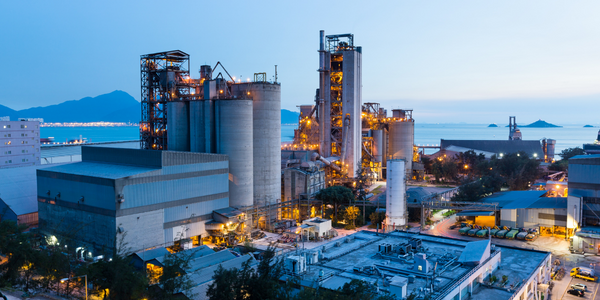
Case Study
Honeywell - Tata Chemicals Improves Data Accessibility with OneWireless
Tata was facing data accessibility challenges in the cement plant control room tapping signals from remote process control areas and other distant locations, including the gas scrubber. Tata needed a wireless solution to extend its control network securely to remote locations that would also provide seamless communication with existing control applications.

Case Study
Advanced Elastomer Systems Upgrades Production
In order to maintain its share of the international market for thermoplastic elastomers AES recently expanded its Florida plant by adding a new production line. While the existing lines were operating satisfactorily using a PROVOX distributed control system with traditional analog I/O, AES wanted advanced technology on the new line for greater economy, efficiency, and reliability. AES officials were anxious to get this line into production to meet incoming orders, but two hurricanes slowed construction.
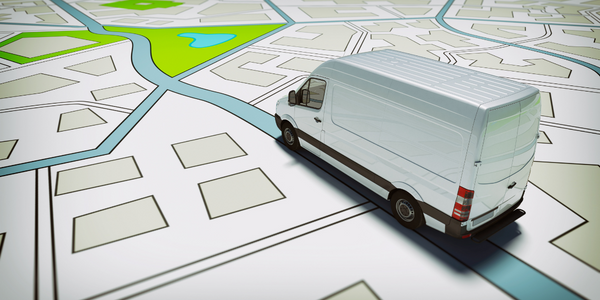
Case Study
Wireless GPS Tracking & Security Monitoring
Enhancing the security of hazardous freight and ensuring compliance with Homeland Security’s Transportation Security Administration mandate that all trains carrying chemicals capable of creating a toxic inhalation condition are equipped with on-board safety monitoring systems.
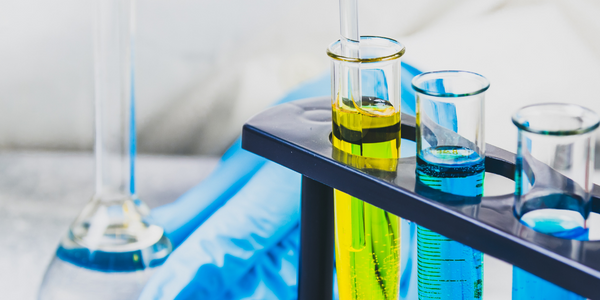
Case Study
Field Device Asset Management For Chemical Company in China
Chinese chemical subsidiary of multinational corporation serves customers throughout the world. Sales offices and research and technology centers are strategically located to provide rapid response to customer requests. Just two workers were assigned to maintain thousands of intelligent instruments in three production units, so they could do little more than react to device issues as they appeared. This costly maintenance method inevitably led to unexpected downtime when a critical instrument failed. Plant management recognized the need to change from reactive to predictive maintenance for all assets, including instruments and control valves, but help was needed in implementing such a technology-based initiative.
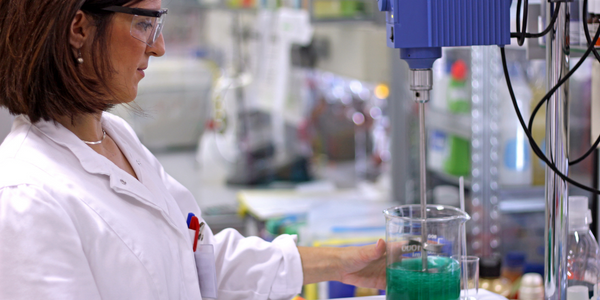
Case Study
Industrial Workforce Mobility for Improved Safety & Operations
Huntsman Corporation, a global manufacturer and marketer of differentiated chemicals, undertook an aggressive program to eliminate injuries, product defects, and environmental releases at their Port Neches facility. Termed “Project Zero”, this program required a completely mobile solution to empower operations and maintenance personnel to capture defects, track work progress and make process and safety related decisions in real-time.