Technology Category
- Analytics & Modeling - Machine Learning
- Analytics & Modeling - Predictive Analytics
Applicable Industries
- Automotive
- Education
Applicable Functions
- Human Resources
- Product Research & Development
Use Cases
- Predictive Maintenance
- Time Sensitive Networking
Services
- Data Science Services
- Training
About The Customer
Ford Motor Company is a Fortune 50 automotive company that operates plants all over the world and produces millions of vehicles every year. Quality, efficiency, and time-to-market are all critical to its profitability and sales growth. More than 30 years ago, Ford began working with Altair to support the company’s product development activities. Today, the company employs Altair software globally to support the development of Ford cars, trucks, and heavy equipment. In many production facilities, there are multiple sheet metal stamping processes available to form nested and individual parts. These include progressive, transfer and tandem press lines.
The Challenge
Sheet metal stamping is a crucial process in the automotive manufacturing industry, with a variety of tool, die, and process combinations used to create a diverse range of components. Traditionally, identifying the optimal stamping process for a specific part design has been a labor-intensive and time-consuming task, heavily reliant on the knowledge and skill level of the stamping engineer. Ford Mexico sought to address this issue by documenting successful metal stamping production runs over a five-year period. The goal was to capture in-house domain knowledge and best practices to expedite the selection of the best stamping process for future production runs. This would enable increased plant efficiency and part quality, reduction of scrap material, and the ability to rapidly train new personnel. However, the challenge lay in the growing design complexity, non-conventional material types, and numerous process combinations that could challenge even the most experienced process engineer, necessitating a labor and material intensive trial-and-error prove-out process.
The Solution
Ford Mexico approached Altair to explore the possibility of applying Altair’s machine learning and predictive analytics solution, Knowledge Studio, to support their business objectives. Using the data Ford had collected for over 3,000 stamping processes identified as being representative of future requirements, Ford’s stamping domain experts and Altair’s solution architects collaborated to develop an accurate, reliable machine learning model with Knowledge Studio. Knowledge Studio offers 15 different machine learning models allowing users to explore, select and train the model that best fits their data. Using subsets of the data, the team ran a series of tests to determine which was most effective. With an accuracy rate of over 90%, the decision tree model produced the most consistent results. The machine learning algorithm provided Ford with results that are close to 100% accurate when combined with all the other datapoints.
Operational Impact
Quantitative Benefit
Case Study missing?
Start adding your own!
Register with your work email and create a new case study profile for your business.
Related Case Studies.
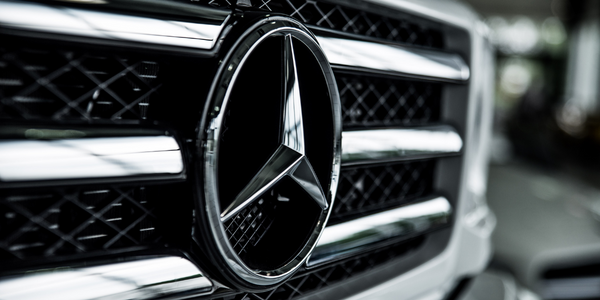
Case Study
Integral Plant Maintenance
Mercedes-Benz and his partner GAZ chose Siemens to be its maintenance partner at a new engine plant in Yaroslavl, Russia. The new plant offers a capacity to manufacture diesel engines for the Russian market, for locally produced Sprinter Classic. In addition to engines for the local market, the Yaroslavl plant will also produce spare parts. Mercedes-Benz Russia and his partner needed a service partner in order to ensure the operation of these lines in a maintenance partnership arrangement. The challenges included coordinating the entire maintenance management operation, in particular inspections, corrective and predictive maintenance activities, and the optimizing spare parts management. Siemens developed a customized maintenance solution that includes all electronic and mechanical maintenance activities (Integral Plant Maintenance).
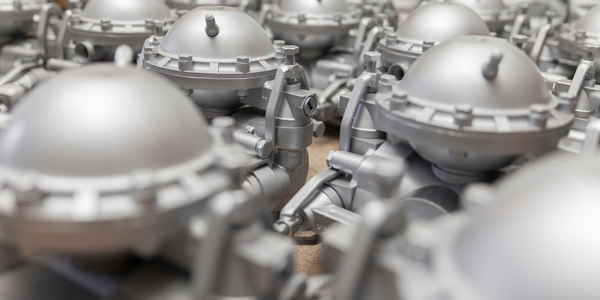
Case Study
Monitoring of Pressure Pumps in Automotive Industry
A large German/American producer of auto parts uses high-pressure pumps to deburr machined parts as a part of its production and quality check process. They decided to monitor these pumps to make sure they work properly and that they can see any indications leading to a potential failure before it affects their process.